For welding aluminum using TIG, a pure tungsten electrode or one alloyed with zirconium is ideal. These electrodes provide stability and ease during the aluminum TIG welding process.
Selecting the right TIG (Tungsten Inert Gas) electrode for aluminum is crucial for achieving strong, clean welds. Such precision work calls for electrodes that can sustain aluminum’s thermal conductivity and oxide formation tendencies. Pure tungsten electrodes, known for their green color band, are traditionally used for their capacity to form a clean, balled tip, which is beneficial for aluminum’s welding characteristics.
Alternatively, zirconium-alloyed electrodes, typically identified by a brown color band, are gaining popularity due to their resistance to contamination and longevity. These electrodes help welders achieve precise and defect-free results in aluminum welding applications, making them essential for high-quality work in various industries such as aerospace, automotive, and manufacturing. Selecting a suitable electrode diameter and type is essential, as it influences arc stability and welding performance.
Properties Of Aluminum
Understanding aluminum’s unique properties is key for TIG welding. With distinct characteristics, aluminum demands specific electrodes for best results. Let’s explore these properties.
High Thermal Conductivity
Aluminum’s high thermal conductivity means it heats up and cools down quickly. This trait requires welders to adjust their technique. Heat control is crucial. Skilled welders use AC balance to manage this challenge.
- Fast heat transmission can lead to warping.
- Welders must use filler material to compensate for the heat.
Oxide Layer
The oxide layer on aluminum is both a blessing and a curse. It prevents corrosion but hinders welding. This layer has a higher melting point than the aluminum beneath.
- Clean the oxide layer before welding.
- Use AC TIG welding to break up the oxide layer.
Types Of Tungsten Electrodes
Choosing the right tungsten electrode is crucial for successful TIG welding, especially with aluminum. Each type of electrode delivers different characteristics. Let’s explore the types of tungsten electrodes used for aluminum welding.
Thoriated Electrodes
Thoriated electrodes stand out for their longevity and ease of use. They contain thorium, which enhances electron emission. Here’s what welders need to know:
- Durability: Last longer than other electrodes.
- Arc Stability: Provide stable arc starts.
- Heat Resistance: High melting point suits high-heat tasks.
Please note you must handle thoriated electrodes with care, due to the low-level radioactivity of thorium.
Lanthanated Electrodes
Lanthanated electrodes are known for their versatility and performance. They are excellent for welding aluminum. Here’s why welders prefer them:
- Easy Arc Starting: Start arcs easily at low amperage levels.
- Stable Welding: Work well across different amps.
- Non-Radioactive: Safer, eco-friendly choice.
Ceriated Electrodes
Ceriated electrodes are great for projects requiring a delicate touch. They are suitable for short welding cycles. Below are the key benefits:
- Low-Emission: Yield minimal arc wander.
- Low-Amperage Welding: Ideal for thin materials.
- Energy-Efficient: Operate well with low current.
With all three types, it’s important to choose the right size and shape for your specific aluminum welding project.
Selecting The Right Tungsten Electrode
Selecting the Right Tungsten Electrode is crucial for TIG welding aluminum. Choosing poorly can result in a weak weld or equipment damage. Learn the right electrode to get strong, clean welds.
Aluminum Alloy Grade
Different grades of aluminum require specific electrodes. We’ll match these with ideal electrodes.
- 1xxx Series: Pure aluminum, choose a pure tungsten rod.
- 2xxx Series: Copper alloy, use ceriated or thoriated type.
- 5xxx Series: Magnesium blend, zirconiated electrodes work best.
- 6xxx Series: Silicon alloy, aim for a lanthanated tungsten.
Ac Or Dc Welding
AC and DC welding use different electrodes. Ensure compatibility:
Type | AC | DC |
---|---|---|
Pure Tungsten | Good | Poor |
Ceriated | Acceptable | Excellent |
Zirconiated | Best | Not Suitable |
Lanthanated | Excellent | Excellent |
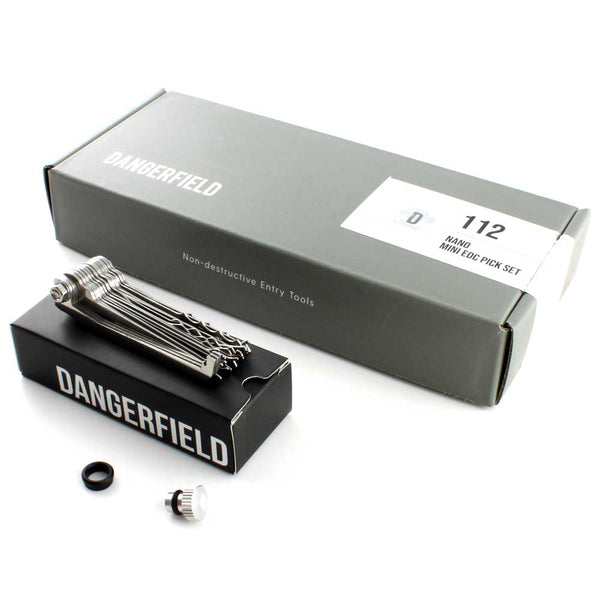
Credit: www.lockpickworld.com
Thoriated Tungsten Electrodes
When TIG welding aluminum, electrode selection is crucial for success. Thoriated tungsten electrodes stand out among options due to their performance. These electrodes contain thorium oxide, which enhances electron emission and arc stability.
Pros Of Thoriated Tungsten Electrodes
The use of thoriated tungsten electrodes offers several advantages for TIG welding. The following are key benefits:
- Improved arc starts lead to easier initiation of the welding process.
- Better current carrying capacity enables handling of higher amperages.
- Durable electrode life reduces the frequency of replacements.
- The electrodes provide a stable arc crucial for high-quality welds.
Cons Of Thoriated Tungsten Electrodes
Despite their benefits, thoriated electrodes have certain drawbacks:
- They contain radioactive materials which require safe handling and disposal.
- Cost is higher compared to some non-radioactive alternatives.
- Sharpening these electrodes can pose health risks due to thorium exposure.
- Specialized equipment is necessary for safe grinding.
Lanthanated Tungsten Electrodes
When it’s time to TIG weld aluminum, choosing the right electrode ensures a clean, strong weld. Lanthanated tungsten electrodes are a popular choice. They contain lanthanum oxide, which helps with arc stability and starting. Users find these electrodes versatile for both AC and DC welding, which makes them suitable for aluminum.
Pros
- Good Arc Stability: Lanthanated electrodes provide a steady arc with minimal flicker or wandering.
- Low Erosion Rate: They wear down slowly, saving time and money on replacements.
- Easy Arc Starting: Ideal for beginners, they make initiating the arc effortless.
- Non-Radioactive: Safer option as they do not contain thorium.
Cons
- Cost: Lanthanated electrodes can be more expensive than other types.
- Color Coding: The blue tip may be less familiar to some, causing confusion with other electrodes.
- Sensitivity to Contaminants: Performance can suffer if not kept clean or if used with impure argon.
Ceriated Tungsten Electrodes
Choosing the right TIG electrode is crucial when welding aluminium. Ceriated tungsten electrodes offer specific advantages for this task. These electrodes contain about 2% cerium oxide, which enhances their performance during the welding process. Here’s an in-depth look at ceriated tungsten electrodes and their use in aluminium welding.
Pros
- Stable arc: Ceriated electrodes provide a stable arc which is essential for high-quality welds.
- Low amperage requirement: They work well at low amperages, making them ideal for welding thin aluminium.
- Non-radioactive: Unlike thoriated electrodes, ceriated electrodes are non-radioactive, posing less health risk.
- Good arc starts: Ensures easy arc starts, reducing the risk of welding defects.
- Versatile use: Suitable for both AC and DC welding processes.
Cons
- Shorter life span: Tends to have a shorter life span compared to other electrodes.
- Higher cost: More expensive than some other electrodes, leading to increased welding costs.
- Limited availability: May not be as readily available as other types of tungsten electrodes.
- Grinding difficulty: Requires careful grinding to prepare a proper tip, which can be challenging.
- Sensitivity to contamination: More prone to contamination, requiring cleaner operation procedures.
Other Considerations
When welding aluminum with TIG, the right electrode isn’t the only factor for a strong weld. Let’s explore two key considerations: electrode diameter and gas choice.
Diameter Of Electrode
Selecting the correct electrode diameter for aluminum is crucial. It affects the current you can use and the heat input. Here’s a simple guide:
Electrode Diameter (inches) | Current Range (Amps) |
---|---|
0.040″ | 15-80 |
1/16″ | 70-150 |
3/32″ | 150-250 |
1/8″ | 225-400 |
5/32″ | 300-500 |
Choose a diameter that matches your machine’s current range and the aluminum thickness.
Gas Selection
The right shielding gas is essential for a clean weld. For welding aluminum, Argon is king. It influences cleanliness and penetration. Here’s what you need:
- Pure Argon – The go-to choice for general welding.
- Argon-Helium Mix – For thicker sections, gives deeper penetration.
Ensure a consistent and adequate gas flow to protect the weld area from airborne contaminants. Match the gas flow rate to the job, usually between 15-30 cubic feet per hour (CFH).
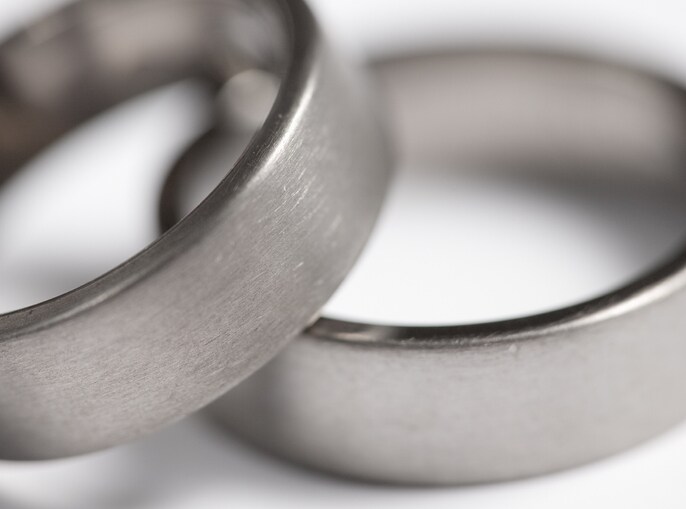
Credit: www.thermofisher.com
Preparation And Storage Of Electrodes
The right preparation and storage of TIG electrodes are vital for high-quality welds. TIG welding for aluminum requires electrodes that create clean, strong, and precise welds. Proper grinding and storage techniques ensure electrodes remain in top condition. Let’s unpack these must-know tips.
Grinding Techniques
Grinding your TIG electrodes is a precision task. Use a dedicated tungsten grinder or a grinding wheel for tungsten to avoid contamination. Align the grind direction with the length of the electrode. This practice reduces the risk of weld contamination and improves arc stability. Remember to grind in a well-ventilated area to avoid inhaling any hazardous material. Always wear protective equipment to keep safe while working on electrodes.
A finer grind is ideal for aluminum since it forms a sharp point. This helps focus the arc for better control. It is critical to maintain consistency in the angle, typically between 15 to 30 degrees, for optimal arc performance on aluminum.
Storage Precautions
Storing TIG electrodes correctly extends their lifespan and maintains their performance. Keep them in a dry, clean, and dedicated storage area. Containers should be labeled according to electrode type and material for easy identification. Humidity can damage electrodes, causing them to become brittle or contaminated. Using airtight containers with desiccants helps to protect them from moisture.
Regularly check your storage environment. Maintain a consistent, moderate temperature to prevent any condensation that might form as a result of temperature fluctuations.
Ensuring you have the appropriate grinding technique and storage measures in place will make your TIG welding experience with aluminum more successful. The preparation of your electrodes can make all the difference in achieving the desired welding results.
Best Practices For Tig Welding Aluminum
TIG welding aluminum requires precision and proper technique to achieve high-quality welds. Issues like contamination or incorrect gas flow can weaken the joint. The following best practices will help you master aluminum TIG welding.
Cleanliness Of Base Metal
Clean aluminum ensures a strong weld. Before welding, take these steps:
- Remove oil and grease with a dedicated solvent.
- Eliminate oxide layers by brushing with a stainless steel brush.
- Wipe the surface clean with a lint-free cloth.
Shielding Gas Flow Rate
Shielding gas protects the weld from atmospheric contamination. Use these guidelines for setting the flow rate:
Material Thickness | Flow Rate (CFH) |
---|---|
< 1/8″ | 10 – 15 |
1/8″ – 1/2″ | 15 – 20 |
> 1/2″ | 20 – 25 |
Adjust the flow rate depending on torch size and weld configuration. Consistent practice ensures skilled weld quality.
Challenges When Welding Aluminum
Aluminum might look smooth and soft, yet welding it is anything but simple. This captivating metal poses unique challenges. Understanding them is key to achieving strong, reliable welds.
Hot Cracking
Hot cracking, also known as hot tearing, is a common issue when welding aluminum. As the aluminum cools and solidifies, it can crack. This is because aluminum shrinks more than steel when it cools. To prevent this, welders must choose the right filler material and welding speed. They also need to pre-heat the aluminum in some cases.
- Pre-heating helps reduce the temperature gradient.
- Proper filler material can accommodate the shrinkage.
- Controlled welding speed ensures even heat distribution.
Burn-through
Burn-through is another challenge encountered when welding aluminum. The metal’s high thermal conductivity and low melting point make it tricky to manage heat input. Too much heat causes excessive melting, leading to holes in the weld. Adjusting the amperage and travel speed are crucial for preventing burn-through.
Factor | Action to Prevent Burn-Through |
---|---|
Amp Settings | Lower the amperage to suit the material’s thickness. |
Travel Speed | Increase speed to reduce heat build-up. |
In summary, aluminum requires a careful balance of heat and speed. With the right approach, hot cracking and burn-through become manageable.
Impact Of Electrode On Weld Quality
Choosing the right TIG electrode for aluminum significantly affects weld quality. The material, tip shape, and size of the electrode should match the welding application. This ensures strong, clean welds. Let’s explore how electrodes impact welding quality.
Penetration
Penetration defines how deep the weld enters the base metal. For aluminum, the common choice is a 2% lanthanated (blue) electrode. It conducts heat well, melting the aluminum thoroughly. Proper electrode choice ensures deep penetration without burning through the metal.
- Focused arc for controlled penetration
- Balanced heat prevents excessive penetration
Aesthetics
Weld appearance, or the aesthetic quality, matters too. A pure tungsten (green) electrode gives a stable arc for neat, tidy beads. This creates visually appealing welds on aluminum. It’s the go-to for projects where looks are as important as strength.
- Clean bead appearance
- Minimal weld cleanup
Case Studies
Selecting the right TIG electrode for aluminum welding can be crucial for achieving the best results. Case studies reveal the differences between various electrodes and how they impact welding performance. Here, we explore real-world applications and comparisons to guide you in choosing the most suitable electrode for your aluminum welding needs.
Comparison Of Welds With Different Electrodes
Experts often compare electrodes to understand their effects on weld quality. Common choices for aluminum are pure tungsten and tungsten alloys. Each has unique properties that dictate performance.
Electrode Type | Weld Appearance | Heat Input | Arc Stability |
---|---|---|---|
Pure Tungsten (Green Tip) | Clean with a wide arc | Lower | Good at low amperages |
2% Thoriated (Red Tip) | Narrower arc with focused heat | Higher | Excellent at higher amperages |
2% Lanthanated (Blue Tip) | Balanced between clean and focused | Medium | Very stable at all ranges |
Each electrode brings different outcomes and is preferred in varied scenarios.
Applications In Different Industries
- Aerospace: High precision. 2% Lanthanated for delicate seams.
- Automotive: Robust welds. 2% Thoriated for frames.
- Maritime: Corrosion resistance. Pure Tungsten for ship parts.
- Construction: Versatility needed. 2% Lanthanated for structures.
Industry demands shape electrode choices. Understanding each sector’s needs ensures optimal selection.
Future Trends
The world of TIG welding continues to evolve, with groundbreaking advancements shaping the way we work with aluminium. These trends promise enhanced efficiency and precision in this highly skilled craft. Especially, in the choice and use of TIG electrodes.
Advancements In Tungsten Technology
Recent developments in tungsten electrode technology offer promise for better welds when working with aluminium. New alloys and refined production processes lead to electrodes that last longer and perform more consistently under high-heat conditions.
- Durable coatings reduce wear and contamination.
- Improved grain structure of the tungsten enhances current carrying capabilities.
- Non-radioactive additives improve safety and performance.
Integration With Robotic Welding Systems
Robotic welding systems are becoming increasingly sophisticated. They provide precision that minimizes human error and increases output. Automation integrates with TIG welding, specifically in aluminium applications, making the role of the electrode more crucial than ever.
- Smart sensors detect electrode degradation and prompt replacements.
- Automated systems select optimal electrodes based on material and project.
- Data-driven adjustments fine-tune electrode performance for consistent quality.
Credit: www.barrons.com
Frequently Asked Questions For What Tig Electrode For Aluminium
What Is The Best Tig Electrode For Aluminum?
The best TIG electrode for aluminum welding is typically a pure tungsten or 2% lanthanated tungsten electrode. These electrodes provide a stable arc for clean, strong welds on aluminum material.
Can You Use Thoriated Electrodes For Aluminum?
No, thoriated electrodes are not recommended for aluminum TIG welding. They contain thorium, which doesn’t provide the necessary arc characteristics for welding aluminum effectively.
How Do You Choose Tig Electrode Size For Aluminum?
Electrode size for aluminum TIG welding depends on the amperage and thickness of the material. Generally, a 1/16 to 3/32-inch electrode is used for aluminum. Higher amperage and thicker material typically require a larger electrode.
Why Use Pure Tungsten Electrodes For Aluminum Welding?
Pure tungsten electrodes are used for aluminum welding because they form a clean, balled end that provides good arc stability on AC, which is best for aluminum’s properties.
Conclusion
Selecting the right TIG electrode for aluminum welding is crucial for optimal results. Pure tungsten or zirconiated electrodes are often preferred for their stability and ease of use. Remember to consider thickness, AC settings, and personal welding style. By choosing wisely, you’ll achieve strong, clean welds on all your aluminum projects.
Trust in your expertise and let the quality of your work shine!