Yes, you can use a welding helmet for plasma cutting. It is crucial to ensure that the helmet has the appropriate shade rating.
Plasma cutting, a process used to cut through various types of metal, demands specific safety measures, just like welding does. Using the correct protective gear is vital for the safety of the operator. A welding helmet comes in handy as it shields the user’s face and eyes from the intense light and heat generated by plasma cutting.
It’s important to choose a welding helmet with the right shade level, typically between #8 and #13, which offers adequate protection during the cutting process. Also, make sure the helmet meets ANSI standards to guarantee the best protection against UV and IR radiation. Good visibility and comfort should also be considered when selecting a helmet for extended periods of use during plasma cutting tasks.
Welding Helmets Vs. Plasma Cutting
When working with high-intensity processes like welding and plasma cutting, safety becomes paramount. It’s crucial to understand the gear needed for each task to ensure maximum protection. Although welding helmets and plasma cutting share similar appearances, diving into their key differences reveals essential information for their proper use.
Key Differences
The primary differences between welding helmets and plasma cutting come down to the type of protection they offer. Shade levels, sensors, and overall design vary significantly:
- Shade Levels: Welding helmets come with varying shade levels suitable for different welding processes.
- Sensors: Helmets for welding often have sensors that detect arc start and adjust the darkness accordingly.
- Design: Plasma cutting does not typically require the same level of shading, which affects helmet design.
Suitability For Plasma Cutting
Can you use a welding helmet for plasma cutting? The answer hinges on the helmet’s features:
Feature | Welding Helmet | Plasma Cutting |
---|---|---|
Shade Level | High shade for welding | Lower shade acceptable |
Sensors | Auto-darkening for arc | May not be necessary |
Weight | Varies | Lightweight preferred |
For plasma cutting, consider helmets designed specifically for the task. They provide appropriate shading and are lightweight for ease of movement.
A welding helmet with adjustable shades might be suitable for plasma cutting, depending on the plasma cutting activity’s intensity. Nonetheless, it is always best to use the right tool for the job to ensure safety and effectiveness.
Understanding Plasma Cutting
Welcome to the fascinating world of plasma cutting, a process that is both powerful and precise. As a versatile tool in the metal fabrication industry, plasma cutting has revolutionized the way we cut through materials. Before delving into the protective equipment needed, such as welding helmets, let’s gain a clearer understanding of plasma cutting.
Basic Principles
Plasma cutting works by sending an electric arc through a gas that is passing through a constricted opening. The gas can be air, nitrogen, argon, or even oxygen. This process creates a high-temperature stream of ionized gas called plasma, which easily melts metal under its path. Plasma cutting achieves quick, clean cuts with minimal effort.
- Electric arc: Generates high heat to create plasma.
- Compressed gas: Gas becomes ionized and conducts electricity.
- High-temperature plasma: Seamlessly cuts through metal.
Types Of Plasma Cutting
There are various types of plasma cutting methods available, each suitable for different kinds of tasks and materials.
- Conventional Plasma Cutting: Suited for general purpose cutting, using air as the plasma gas.
- High Definition Plasma Cutting: Offers enhanced precision and quality, ideal for intricate patterns and fine details.
- Dual Gas Plasma Cutting: Utilizes a combination of gases to optimize quality and efficiency for specific materials.
Type | Gases Used | Applications |
---|---|---|
Conventional | Air | General cutting |
High Definition | Nitrogen, Hydrogen | Fine detailing |
Dual Gas | Oxygen, Argon | Specialized tasks |
Each type of plasma cutting offers unique advantages. Understanding these differences is key to picking the right method for a project.
Features Of Welding Helmets
Understanding the features of welding helmets is essential, whether for professional welding or plasma cutting. These helmets safeguard the eyes, face, and neck from hazardous radiation, heat, and sparks. Let’s examine some key features that set high-quality welding helmets apart, making them versatile for multiple applications, including plasma cutting.
Auto-darkening Technology
Auto-darkening welding helmets are a game-changer in eye protection. These helmets come with lenses that automatically adjust the darkness to protect your eyes from intense light. They respond in a fraction of a second, blinking from light to dark as soon as the welding arc is struck. This technology allows for seamless transitions without ever lifting the helmet. Below are prime benefits:
- Safety: Protects instantly against harmful light.
- Efficiency: No need to stop and start to adjust the shade.
- Accuracy: Improves work as users can see clearly before starting.
These features make auto-darkening helmets suitable for plasma cutting, providing consistent protection.
Convenience And Comfort
Wielding tools for extended periods requires comfort. Welding helmets are designed with user comfort in mind. They offer adjustable headbands to fit different head sizes and reduce neck strain. Lightweight materials prevent fatigue during long hours of work. Other features include:
- Breathability: Ample air flow to reduce heat and fog.
- Balanced Design: Minimizes pressure points on the head.
- Padding: Cushions for added comfort.
These elements combine to deliver a welding helmet that you can wear comfortably through long tasks like plasma cutting. It ensures productivity is high and fatigue is low.
Protection And Safety
When working with plasma cutters, your safety is paramount. The intense heat and light produced during cutting can be harmful. Using a welding helmet is not just a personal preference; it’s essential. It ensures your face, eyes, and neck are shielded from the hazards of plasma cutting.
Protection Against Uv/ir
The intense light from plasma cutting includes ultraviolet (UV) and infrared (IR) rays. These rays can damage your eyes. A welder’s helmet with the right shade lens can block these harmful rays. It helps keep your vision safe.
Choose a helmet with a lens shade that matches the intensity of the plasma cutting task. The right lens will protect your eyes effectively.
Heat And Impact Resistance
Plasma cutting generates heat and sparks. A welding helmet can withstand this heat. It protects your face and neck from sparks, spatter, and molten metal.
Welding helmets are also built to resist impact. They guard against flying debris which might occur during cutting. This dual protection ensures you work confidently, knowing you’re well protected.
Wearing the right protective gear is a non-negotiable for plasma cutting work. A welding helmet is a versatile tool that provides invaluable protection.
Always confirm that your helmet meets the required safety standards. Ensure it can withstand the specific hazards associated with plasma cutting before use.
Limitations Of Welding Helmets
Using a welding helmet for plasma cutting might seem like a good idea. It’s essential to understand the limitations. These helmets are made mainly for welding tasks. Plasma cutting has different requirements. Below, we delve into the specific issues one might face.
Visibility And Clarity Issues
Visibility is crucial for precision in plasma cutting. A standard welding helmet could restrict your ability to see clearly. Here’s why:
- Shade Levels: The darkness of the glass in welding helmets is for intense light from welding. Plasma cutting produces less light. This could mean the helmet is too dark.
- Color Recognition: Welding helmets can alter colors. This can lead to errors in following cut lines.
- Field of View: Helmets intended for welding often have a narrower viewing area. A wider view is better for plasma cutting to see the workspace.
Susceptibility To Damage
Welding helmets can get damaged during plasma cutting. To protect your gear, consider the following points:
Helmet Feature | Plasma Cutting Impact |
---|---|
Lens Coating | Molten metal can speckle and weaken the coating. |
Outer Shell | Heat and sparks can warp or melt specific materials. |
Sensors | Plasma arc could fail to trigger auto-darkening sensors consistently. |
A helmet that is not designed for the job may result in increased costs. More frequent replacements or repairs could be needed. Choose gear that matches the plasma cutting environment for best performance and durability.
Benefits Of Using A Welding Helmet For Plasma Cutting
Utilizing a welding helmet during plasma cutting offers substantial eye protection against the intense light and UV rays emitted in the process. It ensures safety and enhances precision, making a welder’s experience both secure and efficient.
Plasma cutting is a crucial task in metal fabrication. It involves super-heated, electrically ionized gas to slice through metal. Proper protection for your eyes is essential. A welding helmet is not just for welding. It offers several advantages for plasma cutting too. This guide highlights key benefits of using a welding helmet during plasma cutting.
Cost-effectiveness
A welding helmet is a smart investment for plasma cutting tasks. Here’s why:
- Saves money by serving dual purposes for welding and plasma cutting.
- Eradicates the need to buy separate safety gear for each task.
- Long-lasting protection, reducing the frequency of replacements.
Versatility
Multi-functionality stands out with a welding helmet:
Features | Benefits |
---|---|
Auto-darkening | Automatically adjusts to light, useful for varied tasks |
Adjustable Shades | Protection tailored to different plasma cutting intensities |
Comfortable Fit | Wear for long periods, ideal for extensive projects. |
A helmet designed for welding caters to different environments and materials. This adaptability makes it an all-around choice for safety.
Considerations Before Using A Welding Helmet For Plasma Cutting
Plasma cutting is a process that requires precision and protection. A welding helmet can often serve double-duty during these tasks. But, it’s crucial to evaluate several factors before using a welding helmet for plasma cutting. These considerations ensure safety and effectiveness while you work.
Regulatory Compliance
Safety comes first in any form of metal fabrication. Confirm that your welding helmet meets specific safety standards before using it for plasma cutting. These standards are there to protect your eyes and face from the intense light and heat generated during the cutting process. Look for helmets that meet ANSI Z87.1 standards, which ensure that the helmet provides the necessary protection for the eyes and face.
Manufacturer Recommendations
Your welding helmet’s manufacturer provides guidelines for proper use. Adhere to these recommendations to ensure optimal performance and longevity of your helmet. The manufacturer can confirm if your helmet is suitable for the specific demands of plasma cutting. They typically list the recommended shade levels for various tasks. Using the correct shade level is critical to protecting your vision from the bright plasma arc.
Remember to check the helmet’s lens reaction time and whether it can keep up with the quick on-off cycles of plasma cutting. Quick reaction times prevent eye strain and provide clearer visibility. Follow the manufacturer’s maintenance tips to maintain the helmet’s protective features and overall functionality.
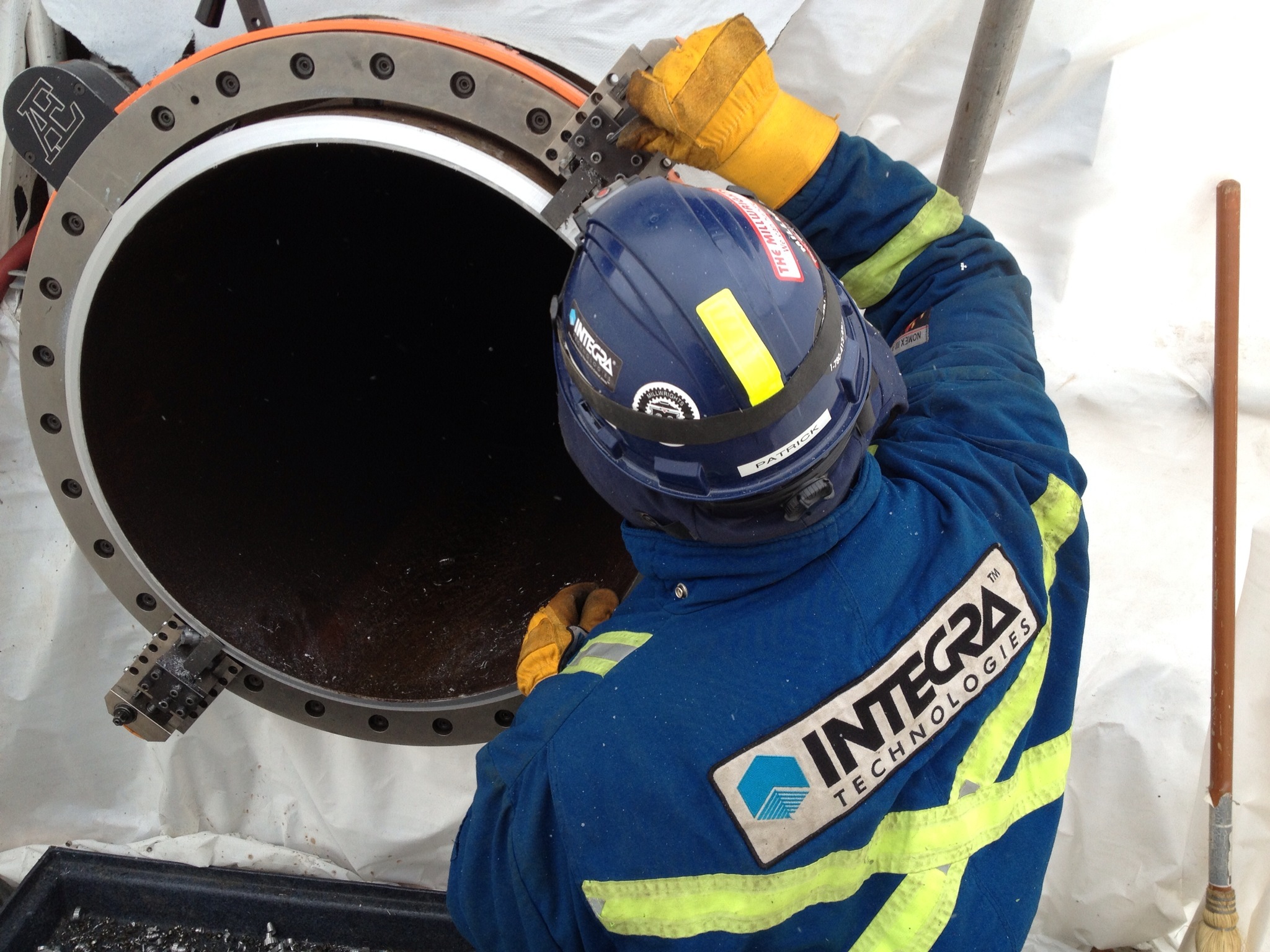
Credit: www.integratechnologies.com
Alternative Safety Gear For Plasma Cutting
When it comes to plasma cutting, proper safety gear is vital. While a welding helmet can provide some protection, there are dedicated items specially designed for this task. Understanding different options helps pick the right protective equipment. Let’s look at some of these alternatives.
Plasma Cutting ShieldsPlasma Cutting Shields
Plasma cutting shields are key in protecting your face and eyes. These shields are light and easy to handle. Choosing the right plasma cutting shield can mean the difference between a safe work environment and a perilous one. Look for shields that:
- Have a face-fit design for maximum coverage.
- Offer a clear view with minimal distortion.
- Are adjustable to suit various head sizes.
Specialized Eye Protection
Specific eye gear is vital in shielding against intense light and heat. Good eye protection during plasma cutting includes:
Goggle Type | Features |
---|---|
Shade 5 glasses | Standard darkening to keep eyes safe |
Auto-darkening lenses | React to light intensity for optimal visibility |
Choose glasses that are comfortable and fit snugly. Ensure they meet safety standards for the highest level of protection.
Best Practices For Using A Welding Helmet In Plasma Cutting
When taking on plasma cutting projects, eye protection is vital. A welding helmet can double as safety gear in plasma cutting if you follow best practices for optimal safety and equipment care. An appropriate helmet shields your eyes from the intense light and ultraviolet rays. Let’s delve into the specifics of how to properly use a welding helmet during plasma cutting.
Adjustment Of Sensitivity Settings
Getting the sensitivity settings right on your welding helmet is crucial when plasma cutting. These settings control how your helmet’s lens reacts to the light produced during the cutting process. Follow these steps:
- Locate the sensitivity adjustment knob on your helmet.
- Set the helmet to handle the plasma cutter’s brightness.
- Start with a lower sensitivity level and increase as needed.
- Test the settings to ensure the helmet darkens properly.
Maintenance And Care
Proper maintenance ensures your welding helmet lasts long and provides adequate protection. Always keep your helmet clean and inspect it regularly:
- Use a soft cloth to wipe the lens after each use.
- Check for cracks or damage.
- Store the helmet in a safe, dust-free place.
- Replace any worn-out parts immediately.
By maintaining your welding helmet, you can rely on it for consistent protection while plasma cutting.

Credit: bakersgas.com
Challenges And Solutions
Plasma cutting presents unique challenges for welders. Proper protection is critical. Yet, many wonder if a welding helmet suffices. Let’s explore solutions to the challenges of fume and particle exposure, and managing heat during plasma cutting.
Fume And Particle Protection
Plasma cutting generates toxic fumes and particles. Welding helmets are designed to shield your eyes and face. But they may not fully protect against these hazards. A solution is to ensure the helmet has a proper filtration system. Look for helmets with an air-purifying respirator feature, which will filter the air you breathe.
- Check helmet specifications: It must meet ANSI Z87.1 standards.
- Opt for integrated respiratory protection: Helmets with built-in respirators offer added safety.
Heat Management
Plasma cutting emits intense heat, which could make the helmet uncomfortable. Modern welding helmets come with features to counteract this. For better heat management:
- Choose helmets with adjustable airflow: This helps in dissipating heat.
- Use helmets with heat-resistant materials: This ensures the helmet withstands high temperatures.
- Wear breathable protective clothing: This reduces the risk of heat stress.
Feature | Benefit |
---|---|
Auto-Darkening Filter (ADF) | Protects eyes from harmful radiation and glare |
Respiratory Protection | Filters toxic fumes and particles |
Heat-Resistant Construction | Withstands intense heat from plasma cutting |
Adjustable Airflow | Manages heat build-up within the helmet |
Case Studies
Exploring real scenarios reveals the viability of welding helmets in plasma cutting. This section delves into various case studies, highlighting successful applications and lessons learned.
Successful Applications
Many professionals have successfully used welding helmets while performing plasma cutting tasks. The following instances demonstrate this fact:
- Automotive Repair Shops: Technicians often wear welding helmets during plasma cutting to protect their eyes from the intense light.
- Metal Art Creators: Artists who work with metals frequently opt for welding helmets to shield their faces and necks from sparks.
- Industrial Manufacturing: Strict safety protocols enforce the use of full-face protection, including welding helmets, for plasma cutting.
Lessons Learned
Every case study imparts valuable insight. Here are some key takeaways:
- Proper Helmet Adjustment: Users learned the importance of correctly setting the shade level on their welding helmets to prevent eye strain.
- Comfort Matters: A comfortable fit is essential for efficiency and safety during extended use.
- Regular Maintenance: Clean lenses and timely helmet inspections contribute to better visibility and protection.
Innovations In Welding Helmets
Innovations in Welding Helmets have revolutionized how welders approach their craft, particularly when it comes to plasma cutting. The need for robust, adaptable safety gear has led to the development of advanced welding helmets, packed with features designed for both safety and convenience. These smart helmets cater to diverse processes, like plasma cutting, enhancing the user experience.
Advanced Features
Welding helmets today are not just about protection; they are about enhancing the welder’s capabilities and ease of use. Modern helmets come with:
- Auto-darkening filters that adjust to the intensity of the light.
- Adjustable shades that offer flexibility based on the type of work.
- Built-in respirators that provide fresh air and keep welders safe from fumes.
- Lightweight, durable materials for extended comfort during long hours of work.
- Sensitivity controls that allow for precise adjustments to various welding environments.
Integration With Plasma Cutting Systems
The progressive integration of welding helmets with plasma cutting systems stands out as a significant milestone. This integration has enabled:
- Real-time data transmission about the cutting process directly to the helmet’s display.
- Evolved control settings for managing the plasma cutter’s output through helmet-mounted interfaces.
- Enhanced safety features that recognize the different requirements of plasma cutting compared to welding.
These integrated helmets offer a unified solution that significantly improves safety and functionality for plasma cutting tasks, streamlining the welder’s work process.
The Future Of Personal Protective Equipment
The advancements in Personal Protective Equipment (PPE) are revolutionizing safety practices across various industries. For activities such as plasma cutting, the right protection for your eyes and face is crucial. Innovative PPE not only ensures safety but also enhances efficiency and comfort, making it a critical aspect of modern workflow.
Trends In Ppe Technology
PPE technologies are evolving rapidly, influenced by strides in material science and digital innovation. Here’s what’s currently trending:
- Smart Helmets: Incorporating heads-up displays for real-time information.
- Lightweight Materials: Advanced composites offering durability without the bulk.
- Improved Filtration Systems: Enhanced respiratory protection against fine particulates.
- Auto-Darkening Lenses: Instant adjustment to the light levels in welding helmets for plasma cutting.
Adaptation To Industry Changes
Safety equipment must keep up with the ever-evolving industrial landscape. Plasma cutting, for example, requires specific attributes in PPE:
Industry Change | PPE Adaptation |
---|---|
Increased Use of Automation | Integration of electronic components in helmets |
Rising Safety Standards | More rigorous testing and certifications for helmets |
Diversification of Welding Techniques | Multi-functional helmets suitable for various applications |
Enhanced Focus on Comfort | Ergonomic designs for long-term use without discomfort |
The PPE of tomorrow is about more than just safety; it’s about integrating seamlessly with the worker’s environment and adapting to their needs. As we move forward, expect to see these trends continue to grow and shape the way we think about protecting ourselves during jobs like plasma cutting.
Training And Education
Entering the world of metal fabrication, skills and knowledge form the foundation. Whether you und the importance of choosing the rigorld f plasma cutting or welding, proper training and education are vital.
Proper Use And Maintenance
Maintaining your welding helmet is not just about longevity; it’s about safety. To use a welding helmet for plasma cutting, follow these steps:
- Read the manual: Understand your helmet’s features.
- Clean your helmet: Wipe the lenses after use.
- Inspect regularly: Check for damages or wear.
- Store safely: Keep your helmet in a dry place.
These practices ensure that your helmet protects you every time. Also, attend training sessions to stay updated on new maintenance techniques.
Risk Awareness
Safety comes first in metal work. Know the risks to stay safe.
- Burns: Plasma cutting creates intense heat.
- Eye damage: Bright arc rays can harm.
- Inhalation risks: Fumes and gases can be toxic.
Education on these dangers is critical. Wear the right gear and use good practices to protect yourself.
Expert Insights
Welding helmets protect your eyes and face while joining metals together. But is it the same when you cut metals with plasma? Experts shed light on this topic, ensuring your safety doesn’t compromise.
Opinions From Industry Experts
- A welding helmet can be used for plasma cutting – Industry Pro.
- Ensure proper shade settings – Safety Specialist.
- Auto-darkening helmets preferred – Welding Expert.
Recommendations
Seeking professional advice gives the best practice. Let’s delve into their recommendations:
Feature | Recommended Setting |
---|---|
Shade Level | #5 to #9 for plasma cutting |
Lens Reaction Time | 1/20,000 sec. or faster |
UV/IR Protection | 100% at all times |
Comfort | Lightweight with an adjustable fit |
Always verify the helmet meets ANSI Z87.1 standards for the best protection.
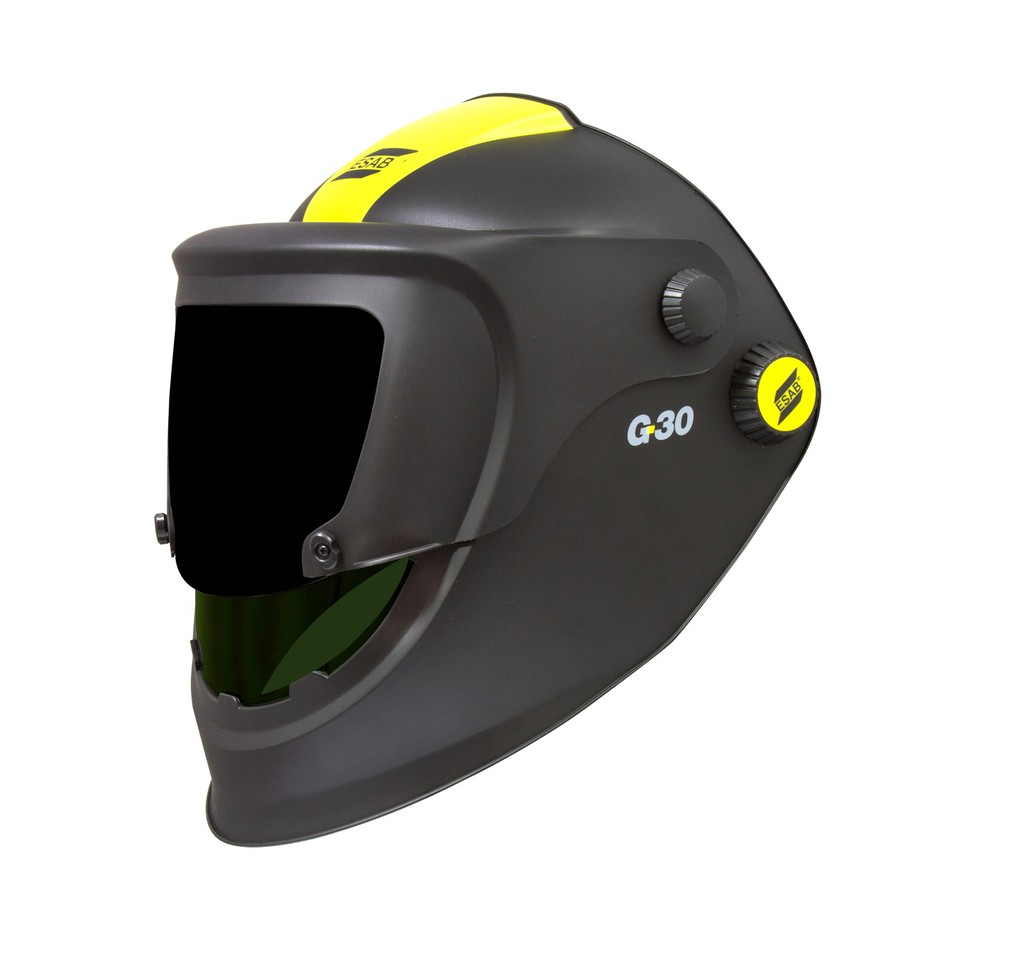
Credit: www.hsmsearch.com
Frequently Asked Questions On Can You Use A Welding Helmet For Plasma Cutting
Is A Welding Helmet Suitable For Plasma Cutting?
Yes, a welding helmet can be suitable for plasma cutting. However, ensure it has the appropriate shade level (at least shade #8) to protect your eyes from the bright plasma cutting arc.
Do You Need A Special Helmet For Plasma Cutting?
You don’t need a special helmet exclusively for plasma cutting, but you do require a helmet with the right shade setting. Helmets with auto-darkening shades ranging from #5 to #9 are recommended for plasma cutting.
What Are The Safety Benefits Of Using Welding Helmets In Plasma Cutting?
Welding helmets provide eye protection from harmful UV and IR radiation and flying debris, which are common hazards during plasma cutting. It ensures that your face is shielded and reduces the risk of injuries.
How Do You Adjust A Welding Helmet For Plasma Cutting?
To adjust a welding helmet for plasma cutting, set the shade level to suit the brightness of the plasma arc, typically a #5 to #9 for most cutting tasks, and ensure the headband fits securely to avoid slippage during use.
Conclusion
Safety should always be a priority in any cutting process. A welding helmet can serve well for plasma cutting, offering the necessary protection and clear vision. Remember to check the shade settings and ensure your helmet meets safety standards before getting started.
Proper gear leads to better, safer work every time.