No, you cannot effectively weld aluminum with 75% Argon 25% CO2 gas mixture. This combination is more suitable for steel welding.
Welding aluminum requires specific techniques and materials to ensure a strong and reliable join. For aluminum, the ideal shielding gas is 100% argon or a mixture of argon and helium. These inert gases prevent oxidation during the welding process, which is crucial for maintaining aluminum’s integrity.
The 75% Argon 25% CO2 mix, often used for MIG welding mild steel, can cause porosity and lack of fusion when applied to aluminum. For hobbyists and professionals aiming for high-quality aluminum welds, choosing the correct gas and welding method is paramount. Proper equipment and technique adherence can significantly impact the durability and appearance of the weld, making the difference between a successful project and a flawed one.
What Is Aluminum Welding?
Aluminum welding joins two pieces of aluminum using high heat. The welder fuses the materials. This process requires skill and the right equipment.
Definition
Welding aluminum involves creating a bond between aluminum parts. Strong, lightweight, and corrosion-resistant welds result. Specialty gases and tools can optimize the welding experience and outcome.
Process Of Aluminum Welding
Here’s a glance at the steps:
- Preparation: Clean the aluminum. Remove any contaminants. This ensures a strong weld.
- Equipment Setup: Choose the right welder. Set voltage and wire feed speed according to aluminum type.
- Welding: Use appropriate techniques. Weld along the joint of the two pieces. Focus on even heat distribution.
- Cool Down: Let the weld cool. Inspect the joint for quality and strength.

Credit: www.amazon.com
Welding Aluminum With Argon And Co2
Many welders face challenges welding aluminum due to its unique properties. The right mix of shielding gas can make a big difference. Some welders consider welding aluminum with a mix of Argon and CO2. Let’s explore why this might be a good idea, and what you need to know before trying it.
Benefits Of Using Argon And Co2
- Improved stability: The mix can offer stable arc performance.
- Cost-effectiveness: CO2 is less expensive than pure Argon, so the mix reduces costs.
- Better control: The combination can enhance control over the weld pool.
- Versatility: Useful for both thin and thick aluminum sheets.
Properties Of Argon And Co2
Gas | Properties |
---|---|
Argon | Inert, non-reactive, creates a smooth weld with minimal spatter |
CO2 | Active, can penetrate deeply, but may introduce more spatter |
Recommended Ratios For Aluminum Welding
Aluminum welding often requires a shielding gas that is high in Argon content. Most professionals recommend a mix of 100% Argon for the best results. This ensures a clean weld with good penetration.
However, some welders opt for a mixture including CO2 to reduce costs or alter the weld characteristics. Keep in mind that 75% Argon and 25% CO2 mix is typically used for steel rather than aluminum. For aluminum, it can compromise the integrity of the weld.
Consultation with a welding professional is highly recommended before using a 75/25 mix for aluminum. Every project is different and may require a tailored approach.
Understanding Argon And Co2 Gas Mixtures
Welding aluminum requires precision in choosing the right materials and tools. The gas mixture plays a critical role in the welding process, contributing to the quality and strength of the weld. Two commonly used gases are Argon and Carbon Dioxide (CO2). When these gases combine, they create a balance which could be ideal for many welding projects. Let’s delve into the differences between Argon and CO2, and explore why a mixture might just be the best choice.
Difference Between Argon And Co2
The primary gas in most welding processes is Argon. It’s an inert gas, meaning it does not react with metal at high temperatures, which is crucial for maintaining the integrity of the weld. Argon ensures a smooth and clean weld, perfect for aluminum. On the other hand, CO2 is a reactive gas. It can make the welding process more volatile, leading to deeper penetration but also increased spatter, which could be messy. CO2 is generally less expensive than Argon, which can be a factor in choosing a gas mixture.
Why Argon And Co2 Mixture Is Used
Combining Argon and CO2 brings together the best of both worlds. Argon provides stability to the welding arc, while CO2 increases the heat, allowing for better penetration into thicker metals. The 75% Argon and 25% CO2 mixture is popular because it maintains the excellent properties of Argon, while enhancing the weld quality with the edge that the added CO2 provides. Particularly in MIG welding, this mixture can be ideal. It improves the overall welding process, leading to stronger and cleaner welds, especially on materials like steel. For aluminum, however, pure Argon is often the preferable choice to avoid porosity and achieve an impeccable finish.
Gas | Properties | Benefits |
---|---|---|
Argon | Inert, Non-reactive | Smooth, clean welds |
CO2 | Reactive, Greater penetration | Cost-effective, Heavy-duty welding |
Argon-CO2 Mixture | Balance between smoothness and penetration | Ideal for MIG welding on steel |
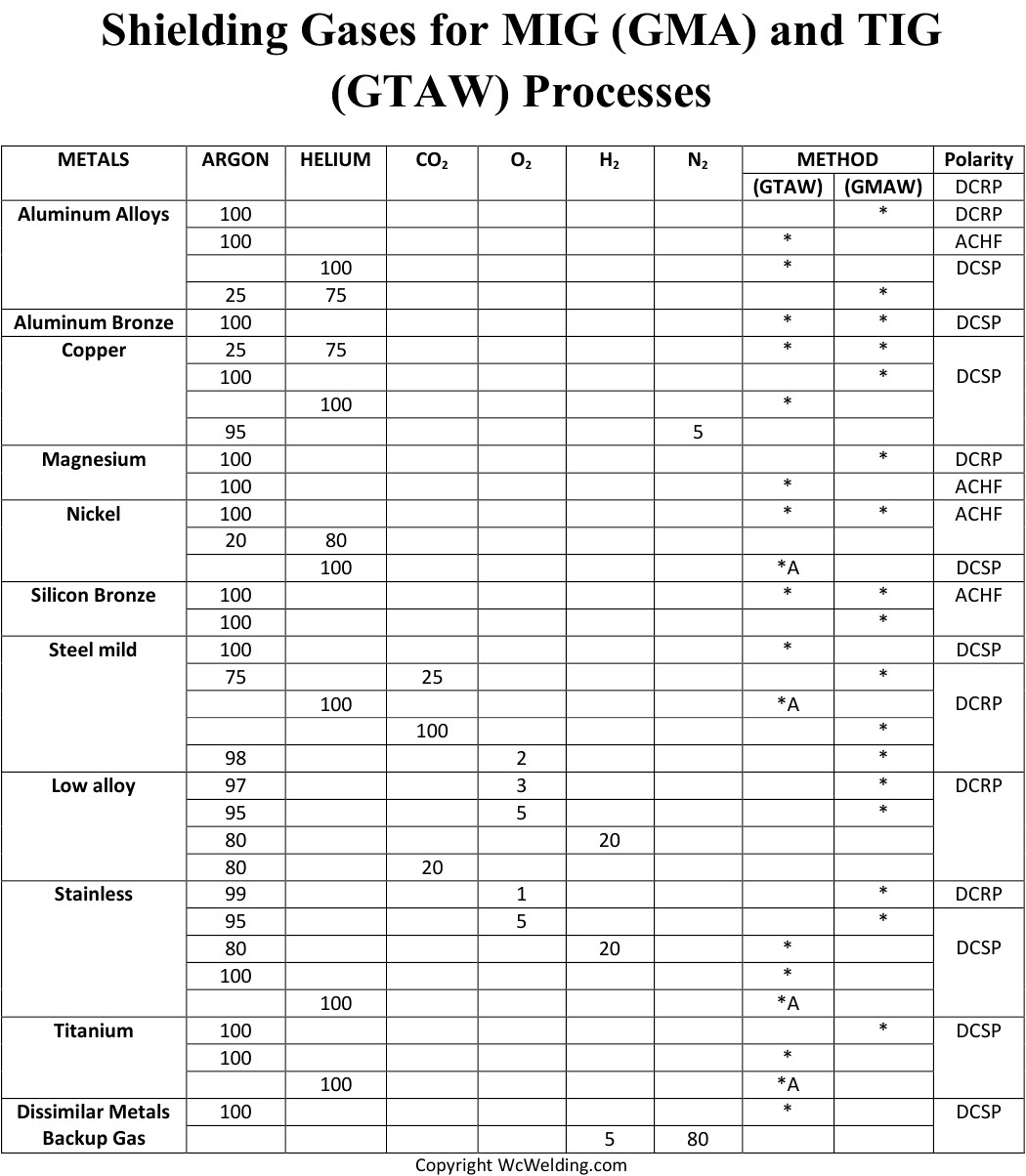
Credit: www.wcwelding.com
Challenges Of Aluminum Welding
Welding aluminum presents unique challenges compared to other metals. Understanding these issues is key to achieving strong and reliable welds. Let’s dive into these challenges.
Thermal Conductivity Of Aluminum
Aluminum’s high thermal conductivity demands extra heat for welding. This causes rapid heat dissipation away from the weld zone.
- Heavier-duty equipment is often necessary.
- Heat input must be closely monitored.
- Technicians need skill in managing weld pool fluidity.
Welders must adapt their techniques and choose appropriate equipment to compensate for these properties.
Oxidation
Aluminum naturally forms a layer of oxide on its surface. The oxide has a higher melting point than the aluminum underneath.
- Removal of this layer prior to welding is essential.
- Welding without removing oxide can lead to impurities in the weld.
- Clean the surface with a stainless steel brush or chemical agents for best results.
This extra step is critical to prevent weld defects and ensure a clean joining process.
Cracking
Aluminum is susceptible to cracking due to its solidification characteristics and thermal expansion. Cracking can occur in different forms:
Type of Cracking | Description |
---|---|
Hot Cracking | Occurs during the solidification phase of the weld. |
Stress Cracking | Happens due to the stresses from thermal expansion and contraction. |
Proper filler material selection and preheating can help mitigate the risk of cracking.
Advantages Of Using 75% Argon And 25% Co2
Advantages of Using 75% Argon and 25% CO2
Welding professionals often favor specific gas mixtures for enhanced results. A combination of 75% Argon and 25% CO2 is popular, especially for welding aluminum. This blend offers a host of benefits, from better penetration to fewer welding challenges.
Improved Penetration
The Argon-CO2 mix significantly boosts the depth and quality of penetration. Welds achieve greater structural integrity due to a more focused arc. This leads to stronger joints and higher-quality work.
Reduced Spatter
Welding can be a messy process, but the Argon-CO2 blend changes that. By reducing spatter, it ensures a cleaner work environment and less post-weld cleanup. This means save time and resources.
Enhanced Weld Pool Control
With this gas mix, welders gain better control over the weld pool. This is crucial for high-quality, precise work. The visibility and control this gas blend provides are unmatched, resulting in superior welding performance.
Tips For Welding Aluminum With 75% Argon And 25% Co2
Welding aluminum poses unique challenges. Mixed gases like 75% Argon and 25% CO2, commonly used for welding steel, might not be the first choice for aluminum. However, with the right tips, you can achieve a quality weld even with this gas mixture.
Proper Gas Flow Rate
Setting the correct gas flow rate is crucial for aluminum welding. Use these steps:
- Connect the gas regulator to the cylinder.
- Open the valve slightly to avoid a surge.
- Adjust your flow rate to 20-30 cubic feet per hour (CFH).
Correct Electrode Selection
Selecting the right electrode ensures a strong weld. For aluminum, use a non-consumable tungsten electrode. The ideal choice is:
- 2% thoriated (red)
- 2% lanthanated (blue)
Grind the electrode to a pointed tip for better arc control.
Welding Techniques
Employ the following techniques for optimal results:
Technique | Benefits |
---|---|
Pulse welding | Reduces heat input, minimizes warping |
Stack of dimes appearance | Indicates controlled heat and feed |
Equipment And Tools For Aluminum Welding
When diving into the world of aluminum welding, choosing the right equipment and tools is crucial. Aluminum requires specific techniques and materials to ensure a strong and durable weld. In this section, we’ll explore the essentials you’ll need for welding aluminum, including the appropriate welding machine, shielding gas, and consumables. Let’s get your workspace equipped for success!
Welding Machine
For aluminum welding, a welding machine with AC (Alternating Current) capability is essential. A popular choice is a TIG (Tungsten Inert Gas) welder. It provides precision and control which aluminum work demands. MIG (Metal Inert Gas) welding can also be an option for thicker aluminum pieces. Look for a machine that offers easy adjustability of amperage and has a high duty cycle for longer welding sessions.
Shielding Gas Cylinder
Shielding gas protects the weld area from atmospheric gases that can affect weld quality. For aluminum welding, 100% argon is the preferred choice over a 75% Argon and 25% CO2 mix. The mix may lead to weld contamination and porosity in aluminum. Ensure the cylinder is certified and equipped with a regulator to accurately control gas flow. Safety when handling gas cylinders is paramount.
Consumables
Consumables are parts of the welding setup that get used up during the welding process. Key consumables include:
- Tungsten electrodes: Make sure these are of the right type and size for aluminum.
- Filler material: Choose a wire or rod that matches the aluminum alloy you’re welding.
- Contact tips and nozzles: Periodically replace these to ensure optimal performance.
- Anti-spatter spray: Keeps the welding area clean from spatter buildup.
For the best results, check manufacturers’ recommendations on consumables for aluminum welding.
Safety Precautions For Aluminum Welding
Working with aluminum requires careful attention to safety. Whether using a 75% Argon 25% CO2 mix or any other gas combination, understanding and abiding by safety protocols is crucial. Proper precautions ensure a safe welding environment. Explore essential safety measures to take during aluminum welding.
Ventilation
Aluminum welding produces fumes that can be harmful if inhaled. It is vital to weld in a well-ventilated area. Here are tips to ensure good ventilation:
- Use local exhaust ventilation at the welding point.
- Ensure cross-ventilation in the work area.
- Consider a fume extraction system if working indoors.
Protective Gear
Wearing the right protective gear is non-negotiable. It helps prevent burns and eye damage. Essential gear includes:
- Auto-darkening welding helmet.
- Fire-resistant gloves.
- Long sleeves and pants to cover skin.
- Leather apron.
- Safety glasses beneath the helmet.
Fire Safety
Aluminum welding can generate sparks that might start a fire. Keep your workspace free of flammable materials. Here’s how you can maintain fire safety:
Fire Safety Checklist |
---|
Keep a fire extinguisher nearby. |
Remove all combustible materials from the welding area. |
Have a fire watch if necessary. |
Inspect the area post-welding for any smoldering materials. |

Credit: yeswelder.com
Frequently Asked Questions On Can You Weld Aluminum With 75% Argon 25% Co2
Can You Use 75/25 Gas For Aluminum Welding?
No, welding aluminum with 75% Argon and 25% CO2 mix is not recommended. This gas mixture can lead to poor quality welds on aluminum because it’s designed for steel. Aluminum welding typically requires 100% Argon or a mix with a higher Argon content to ensure clean, strong welds.
What’s The Best Gas For Tig Welding Aluminum?
The best gas for TIG welding aluminum is pure Argon. It provides a stable arc, good cleaning action, and better heat control when welding aluminum, which is key to producing high-quality welds. Mixtures containing helium may also be used for thicker aluminum pieces.
Why Is 100% Argon Better For Aluminum Welding?
100% Argon is better for aluminum welding because of its inert properties that prevent chemical reactions with the hot metal. It ensures smoother and cleaner welds with better control over the welding puddle compared to mixed gases.
Is A 75/25 Argon Co2 Mix Good For Mig Welding?
While a 75/25 Argon CO2 mix is not suitable for aluminum, it is often used successfully for MIG welding on steel. It provides good arc stability, reduced spatter, and better penetration for steel welding applications.
Conclusion
Welding aluminum presents unique challenges, but choosing the right gas mixture is key. A 75% argon and 25% CO2 blend may not be traditional for aluminum welding, but it can work with the proper technique and expectations set. Remember, success hinges on understanding the materials and refining your approach for optimal results.
Embrace experimentation and safety as you explore this welding option.