For gas welding, typically a coated steel rod is used. The coating material depends on the welding application and the metals being joined.
Gas welding, often referred to as oxy-fuel welding, relies on a flame produced by a mixture of oxygen and a fuel gas—usually acetylene. It’s a traditional technique still favored for its portability and control in various metal joining tasks. Selecting the correct rod is crucial for a strong and clean weld.
Welding rods for this method come in multiple materials, such as mild steel, high-carbon steel, copper, and aluminum, each coated with a flux to prevent oxidation during the welding process. The choice of rod greatly influences the strength, quality, and durability of the weld. As welders navigate through materials of different thicknesses and types, choosing a rod that complements the base metals ensures better fusion and welding success. Thus, understanding the material compatibility and the specific requirements of your welding job is essential in selecting the right type of rod for gas welding.
Understanding Gas Welding Rods
Gas welding, known for precision and control, uses rods as its filler material. These rods are crucial for joint strength and finish. Let’s dive into what makes up these rods and why flux matters.
Composition Of Gas Welding Rods
Each rod in gas welding has a unique makeup tailored to the task. Knowing these ingredients ensures a strong, clean weld. Here’s a breakdown of what’s inside:
- Carbon Steel – Common in versatile welding scenarios.
- Aluminum – Best for lightweight metals like itself.
- Bronze – Ideal for joining copper or resisting corrosion.
- Stainless Steel – Used for its rust-resistant qualities.
Role Of Flux In Gas Welding
Flux keeps the weld clean. It’s the secret to strong gas welding output. Look at its benefits:
- Prevents Oxidation – Flux covers the weld area, shielding it from air.
- Improves Flow – It allows the filler to move smoothly over the joint.
- Removes Impurities – Acting like a cleaning agent, flux purges the metal.
- Creates Better Bonds – A cleaner weld means a stronger join.
Selection Criteria
Choosing the right rod for gas welding can feel tricky. You must consider various factors to ensure a strong, durable weld. Everything from the material you’re welding to the thickness and joint design plays a crucial role in the rod selection process. Let’s break down these key considerations.
Material Being Welded
Different materials require different types of rods. Each rod is tailored to work best with specific metal types. For steel, you generally use copper-coated rods to ensure a smooth welding experience and a strong bond. Aluminum, on the other hand, needs non-ferrous rods that cater to its unique melting point.
Thickness Of The Material
Thickness influences rod choice. Thin materials need smaller rods to prevent burn-through. For thicker materials, larger rods are better as they need more heat to penetrate effectively. Remember:
- Thin materials: Use rods with diameter 1/16 inch or smaller.
- Thick materials: Go for rods with diameter over 1/8 inch.
Joint Design
The type of joint you’re welding dictates the rod size and type. For butt and fillet welds, use rods that can fill the joint properly. Joints under stress require rods that produce stronger welds to handle the load. Streamline your choices based on joint types:
Joint Type | Rod Requirement |
---|---|
Butt Joint | Medium to large rod |
Fillet Joint | Small to medium rod |
Corner Joint | Medium rod |
Types Of Rods
Choosing the right rod for gas welding is like picking the perfect paintbrush for a masterpiece. Each rod type brings unique features to the welding table. Whether you’re a professional or a hobbyist, understanding rod differences is key for strong, clean welds. Let’s dive into the various rod types available.
Bare Rods
Bare rods are the simplest form used in gas welding. Made from filler metals without any coatings, these rods melt easily. They fuse metals effectively. Remember, they are sensitive to the surrounding atmosphere during the welding process. This can affect the finished weld’s quality. Bare rods are best used with a flux. Flux prevents oxidation and helps produce a cleaner weld.
- Common Bare Rod Metals:
- Copper
- Aluminum
- Mild Steel
- Stainless Steel
Covered Rods
Covered rods, also known as coated rods, have a protective layer. This coating shields the weld area from contaminants. It improves the welding process. These rods come in various types, each designed for specific metals and welding conditions.
They offer better operator control. This reduces splatter. The coating decomposes during welding. It forms a shielding gas that protects the weld. Most importantly, covered rods enhance the strength and quality of the weld.
Type | Coating Material | Features |
---|---|---|
Rutile Rods | Titanium dioxide | Easy to use with smooth arc |
Cellulosic Rods | Cellulose | Deep penetration, suitable for rusty metals |
Low-Hydrogen Rods | Ferrous powders | Minimizes hydrogen, prevents cracking |
Understanding these rod types guides welders. It ensures the right match for the job. Both bare and covered rods carry distinct benefits. They each play important roles in different welding scenarios.
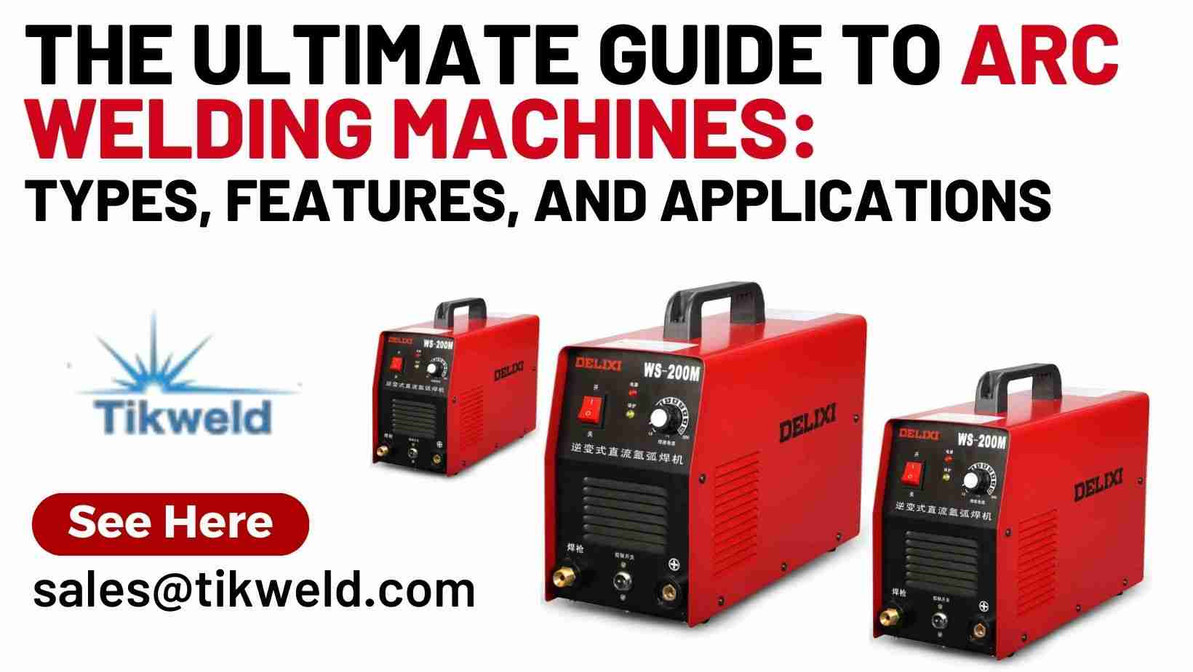
Credit: tikweld.com
Bare Rods
When embarking on the path of gas welding, choosing the right type of rod is crucial. Bare rods stand out in this welding journey for their simplicity and efficacy. These rods lack coating, unlike their covered counterparts, but don’t let their modesty fool you.
Overview Of Bare Rods
At the core of gas welding is the use of a filler metal; enter the bare rod. Standard in nature, these rods are made of wire without flux on their surface. This simplicity means they’re versatile, adaptable to various welding scenarios.
Applications Of Bare Rods
Bare rods serve a variety of purposes, each distinct based on the metal being joined. Let’s delve into their common uses:
- Sheet metal work – preciseness is key, and bare rods excel here.
- Repair jobs – perfect for mending broken items due to their adaptability.
- Joining non-ferrous metals – they’re a go-to for metals like aluminum and copper.
Understanding the right application ensures the strength and quality of the weld. Unique properties of bare rods make them suitable for specific tasks. Indeed, these rods play an integral part in creating strong, lasting joins in metalwork.
Covered Rods
When selecting a rod for gas welding, ‘Covered Rods’ standout for specific applications. These rods come with a special flux coating. This coating plays a critical role during welding. Let’s delve into what makes covered rods a choice for welders.
Overview
Covered rods, also known as coated rods, are used in gas welding processes. The coating on these rods often contains materials that serve multiple purposes. They protect the weld area from contaminants. They also help stabilize the arc and introduce deoxidizers. All these help create a stronger, cleaner weld.
Advantages
- Better Contaminant Protection: The coating shields the molten weld from oxidation and nitrogen absorption.
- Improved Weld Quality: Flux in the coating aids in producing cleaner welds by removing impurities.
- Stabilized Arc: Arc stabilization results in a smoother welding process with less spatter.
Limitations
- Slag Removal: After welding, the user must remove slag, which adds a step to the process.
- Sensitivity to Moisture: Covered rods can absorb moisture, which may lead to weld defects if not stored properly.
- Storage Conditions: These rods require dry storage to maintain their coating integrity.
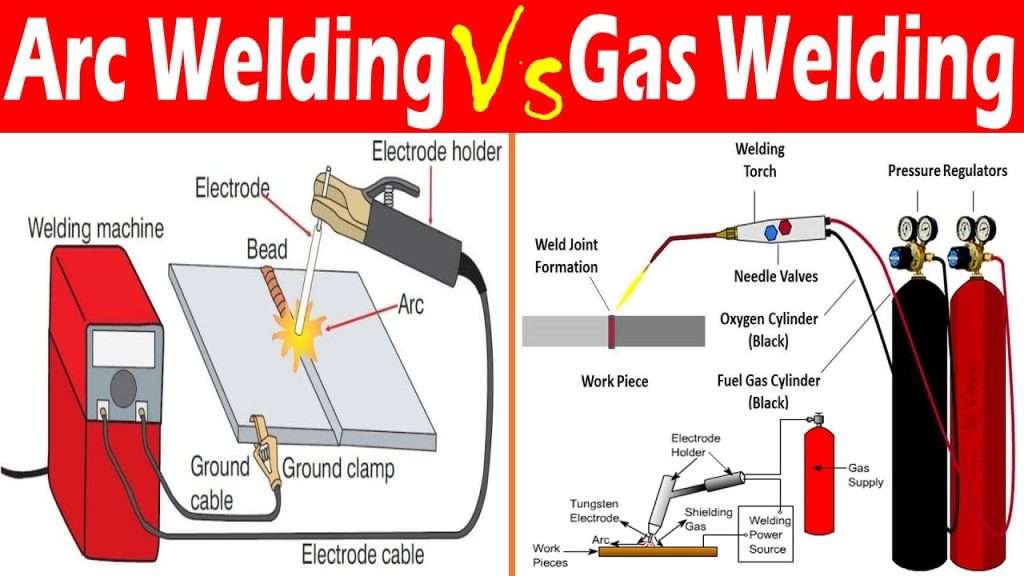
Credit: proleantech.com
Flux Considerations
Selecting the right rod for gas welding involves understanding flux considerations. The right flux can significantly improve welding quality.
Types Of Flux
Flux types vary depending on their chemical composition and intended use. Common variants include:
- Borax-based Flux: Ideal for general-purpose welding, particularly with ferrous metals.
- Boric Acid Flux: Used specifically for welding non-ferrous metals like copper alloys.
- Ammonium Chloride Flux: Common in soldering applications, not recommended for high-strength welds.
Impact On Weld Quality
Flux quality plays a crucial role in the final weld. Here’s why:
Flux Feature | Impact on Weld |
---|---|
Cleanliness | Removes surface impurities, ensuring a stronger bond. |
Stability | Decreases the risk of weld cracking over time. |
Compatibility | Matches with the metal, preventing chemical reactions that weaken the weld. |
A right flux selection means less post-weld cleanup and a visually appealing, reliable joint.
Storage And Handling
When it comes to gas welding, selecting the right rod is only half the battle. Proper storage and handling are just as crucial to ensure your welding projects are safe and effective. Mishandled or poorly stored rods can lead to compromised welds or even accidents. Let’s dive into the best practices for keeping your rods in top shape.
Proper Storage Practices
Storing gas welding rods correctly is vital for their longevity and performance. Here are the key steps:
- Keep rods dry: Moisture is the enemy. Store rods in a dry place.
- Avoid direct sunlight: UV rays can weaken the rod’s coating.
- Maintain temperature: Excessive heat or cold can damage rods. Aim for a consistent temperature.
- Use original containers: They are designed to protect rods from harm.
- Vertical storage: Standing rods upright prevents bending or warping.
- Inventory rotation: Use older stock first to prevent aging.
Handling Precautions
Handling rods with care is essential. Follow these precautions:
- Wear gloves: Protects hands and keeps oils from your skin off the rods.
- Gentle touch: Handle rods with care to avoid damaging the fragile coating.
- Transport safely: Use a secure container to avoid dropping or striking the rods.
- Avoid contaminants: Keep rods away from grease, oil, or any contaminants that could affect the weld.
Mindful storage and careful handling guarantee your gas welding rods are ready when you need them. Stick to these guidelines and maintain top-notch welding performance.
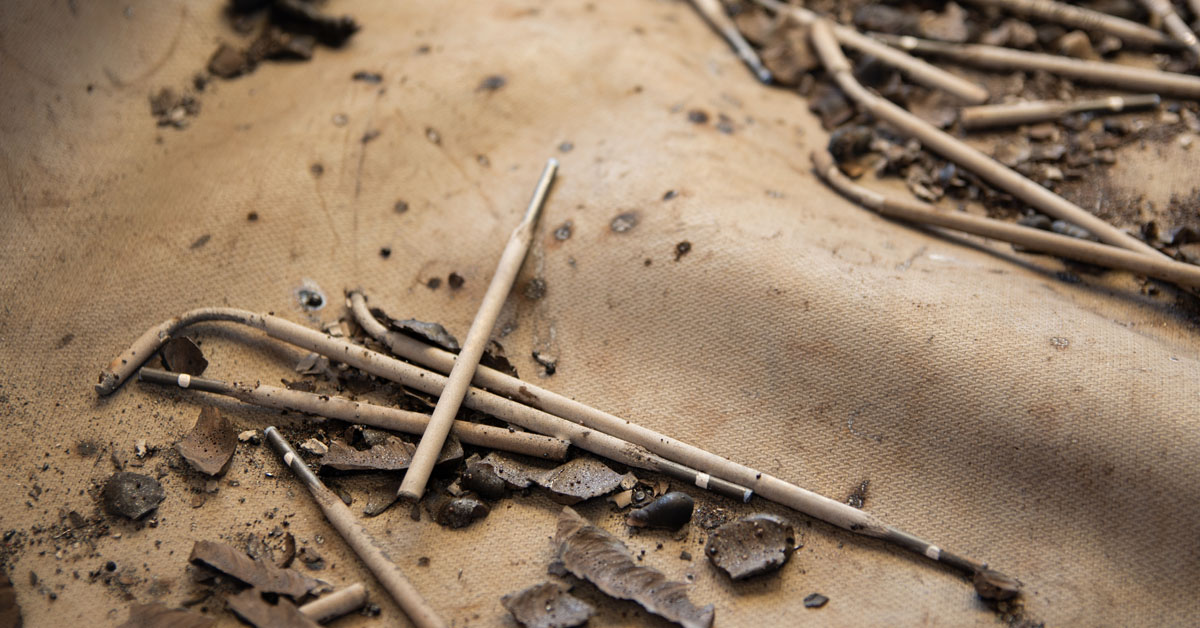
Credit: blog.red-d-arc.com
Safety Precautions
Gas welding requires careful handling. Safety must come first. Welders must be aware of the potential hazards associated with welding. Risks include fumes and gases that can pose serious health issues. Protective measures are essential to ensure safety during welding tasks.
Risk Of Fumes And Gases
Welding can produce hazardous fumes and gases. These substances can lead to health problems. Long-term exposure increases the risk significantly. It is vital to understand these risks.
- Carbon monoxide can cause poisoning.
- Nitrogen oxides can affect lung health.
- Ozone can irritate the respiratory system.
Ventilation is crucial to disperse harmful gases. Respirators may be necessary.
Protective Measures
Action | Purpose |
---|---|
Use respirator masks | Prevent inhalation of harmful substances |
Wear protective clothing | Shield skin from sparks and heat |
Install proper ventilation | Reduce concentration of toxic fumes |
Ensure a safe working environment with these measures. Training on safety protocols is also essential. Keep a first-aid kit handy and know how to use it.
Frequently Asked Questions For What Type Of Rod For Gas Welding?
What Is Gas Welding?
Gas welding, often known as oxy-fuel welding, is a process that uses fuel gases and oxygen to weld and cut metals.
Best Rod Type For Gas Welding?
For gas welding, the most commonly used rods are made from mild steel, known as RG-45 or RG-60.
Does Rod Selection Affect Welding Quality?
Absolutely, choosing the correct rod ensures proper fusion and strength in the weld joint.
Can You Use Tig Rods For Gas Welding?
While possible, TIG rods are generally not recommended for gas welding due their different compositions.
Conclusion
Selecting the right rod for gas welding is crucial for project success. Your choice hinges on the metal type and desired outcome. High-quality, compatible rods ensure durable, clean welds. Remember to prioritize safety and match rods to the specific task at hand.
Equip yourself for welding excellence—make an informed rod selection.