Choose a welding rod based on the metal type and the required weld strength. Consider compatibility with the base metal and welding position.
Selecting the appropriate welding rod is vital for the integrity and strength of your welds. Welding rods, often called electrodes, are integral to the welding process, acting as a filler material to join metals. The choice hinges on several factors, including the base metal’s properties, the welding position, and the desired strength of the joint.
Most importantly, the electrode must match the metal workpiece to avoid weld defects. Beginners and seasoned professionals alike should always ensure the chosen rod complies with the specifications of the welding task at hand. A well-matched welding rod not only facilitates a smoother welding process but also significantly enhances the durability and quality of the weld.

Credit: bakersgas.com
Understanding Welding Rods
Ready to delve into the world of welding rods? A successful welding job starts with understanding these crucial components. Let’s unravel the mystery of welding rods together, ensuring every project shines with excellence.
What Are Welding Rods?
Welding rods, also known as electrodes, are integral to the welding process. These metal wires join materials by creating a robust, fused connection.
- Stick welding relies on consumable rods.
- TIG welding uses non-consumable rods.
- Each rod has a flux coating to protect the weld area from oxidation and contamination.
Understanding which rod to select is vital for a strong, clean weld.
Importance Of Choosing The Right Welding Rod
Selecting the perfect welding rod is a game-changer. The right rod ensures:
Aspect | Benefit |
---|---|
Material Compatibility | Precise bonding with various metals |
Strength of Weld | Long-lasting, durable connections |
Corrosion Resistance | Welds endure harsh environments |
Metal Thickness | Appropriate penetration and fusion |
Always match the rod to your specific welding task.
Rod Number | Use Case |
---|---|
E6013 | General-purpose welding |
E7018 | High-quality, professional welds |
Consult your project’s requirements before choosing a rod. Check your metal types and the desired weld strength. Look for rods that offer appropriate thickness for your material. This attention to detail promises stellar project outcomes.
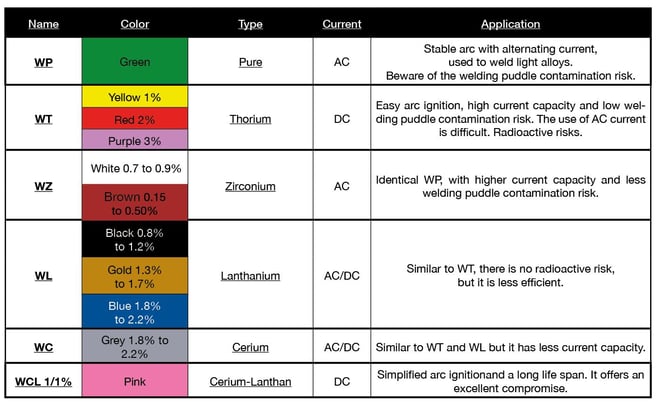
Credit: www.axxair.com
Types Of Welding Rods
Exploring the world of welding involves understanding the tools of the trade, primarily welding rods. These rods play a crucial role in the quality and strength of the weld. Knowing the different types ensures that each project results in a durable and stable structure.
Overview Of Different Types
Welding rods, also known as welding electrodes, come in various types tailored to different needs. Each type boasts unique characteristics suited for specific metal types and welding conditions.
- Bare Electrodes: Require external shielding gas.
- Light Coated Electrodes: Have a light coating, which enhances the stability of the arc.
- Heavy Coated Electrodes: These are covered with a thicker coating for deeper penetration and smoother welds.
- Tungsten Electrodes: Ideal for TIG welding, resistant to high temperatures.
Commonly Used Welding Rods
Some welding rods are widely favored for their versatility and ease of use. Common choices include:
Rod Type | Description | Common Uses |
---|---|---|
E6010 | Deep penetration, works on dirty or rusted metals. | Pipeline welding, shipbuilding. |
E6013 | Medium penetration, easy to control. | General repairs, DIY projects. |
E7018 | Low hydrogen, prevents cracking. | Construction, structural welding. |
Specialized Welding Rods For Specific Applications
For each unique welding challenge, there’s a specialized rod. These specialized electrodes cater to specific industry standards and materials:
- Cast Iron Welding Rods: Designed for cast iron repairs, reducing the risk of cracks.
- Stainless Steel Welding Rods: Best for stainless steel, avoiding corrosion.
- Aluminum Welding Rods: Tailored for aluminum work, ensuring a strong bond.
- Hardfacing Welding Rods: Reinforces surfaces to resist abrasion and wear.
Determining Welding Rod Size
Selecting the appropriate welding rod size is crucial for project success. A rod too small may not penetrate deeply. A rod too large might be difficult to handle. Understanding how to choose the correct rod size ensures strong, durable welds every time.
Factors To Consider
Several key factors influence the choice of welding rod size. Material type, thickness, welding position, and power supply are among the most important.
- Material Type: Different materials weld best with rods that match their properties.
- Thickness: Thick materials require larger rods for proper penetration.
- Welding Position: Overhead welding, for instance, may need smaller rods for better control.
- Power Supply: Your welding machine’s amperage capacity might limit rod size.
Matching Rod Size To Metal Thickness
To match rod size to metal thickness, check the rod’s specifications. The diameter of the rod usually correlates with the metal’s thickness. A basic rule is to use a rod diameter that is about the same as the metal thickness.
Metal Thickness | Rod Diameter |
---|---|
1/8 inch | 1/8 inch |
1/4 inch | 1/4 inch |
1/2 inch | 3/8 inch |
Recommended Rod Sizes For Common Applications
For general purposes, certain rod sizes are frequently recommended:
- For sheet metal: Use 1/16 inch rods.
- Automotive parts: Use 3/32 inch or 1/8 inch depending on thickness.
- Heavy repair or construction: Use 3/16 inch or 1/4 inch rods.
Choosing the right size is a balance between the job requirements and the welder’s skill. It’s always best to refer to the metal’s specifications and consult with experienced welders when uncertain.
Understanding Welding Rod Coatings
Within the art of welding, choosing the right welding rod is crucial. An essential aspect often overlooked is the coating. Coatings significantly influence the welding process and the quality of the final joint. Let’s dive into the world of welding rod coatings.
Purpose Of Coatings
Coatings on welding rods are far from just an aesthetic touch. They’re engineered for protection and performance enhancement. Their primary role is to stabilize the arc, shield the molten weld from contaminants, and shape the characteristics of the weld.
- Enhance arc stability
- Shield against impurities
- Control slag formation
- Alter weld metal properties
Different Types Of Coatings And Their Uses
Diverse environments and materials call for various coatings. Each type comes with its own set of benefits.
Type of Coating | Applications | Benefits |
---|---|---|
Rutile | General-purpose | User-friendly, smooth finish |
Cellulosic | Pipeline welding | Deep penetration, strong arc |
Basic (Low-hydrogen) | High-strength steels | Minimizes porosity, cracks prevention |
Iron Oxide | Sheet metal | High-speed welding, reduces splatter |
Choosing The Right Coating For The Job
Selection necessitates consideration of the job at hand, the base material, and the desired results. Follow these simple steps to select:
- Identify the base metal and its properties.
- Consider the welding position – flat, vertical, or overhead.
- Match coating properties to the welding application.
- Account for environmental conditions, like humidity.
In summary, a well-matched coating ensures a strong weld, easier handling, and superior finish. Always refer to the manufacturer’s specifications and your project’s requirements to make an informed choice.
Considerations For Welding Rod Material
Understanding the material of a welding rod is crucial in achieving a strong and durable weld. The rod you select must match the base metal’s properties, withstand the project’s demands, and suit the welding environment. Let’s explore how to choose the right welding rod material for your welding tasks.
Matching Rod Material To Base Metal
The key to a successful weld lies in selecting a welding rod that perfectly aligns with the base metal. Here are simple steps to ensure compatibility:
- Identify the base metal – Know its composition and grade.
- Match the rod – Use a rod material that complements the metal’s properties.
- Consult charts – Welding charts suggest suitable matches.
Understanding Alloy Rods
Alloy rods are designed for specific applications; understanding them can lead to a superior weld. Consider:
- The preset mix of elements – Each alloy rod has a unique formula.
- Performance factors – Consider strength, crack resistance, and corrosion tolerance.
- Specialized tasks require specialized alloy rods.
Selecting The Appropriate Material For Different Projects
The project’s nature influences your choice of welding rod material. For example:
Project Type | Recommended Rod Material |
---|---|
Outdoor structures | Weather-resistant rods |
High-stress equipment | High-strength alloy |
Decorative pieces | Easy-to-polish material |
Pick a rod that will both perform well and last in the environment where the project will exist.
Understanding Welding Rod Codes
Choosing the right welding rod is crucial for quality welds. The welding rod code on each rod holds key information. It ensures welders pick the appropriate electrode for their project. Understanding what these codes mean simplifies the selection process.
Importance Of Welding Rod Codes
Welding rod codes tell about the rod’s capabilities. They reveal the rod’s strength, suitable positions for welding, and the type of coating it has. This makes choosing the right rod easier and helps prevent welding failures.
Decoding Welding Rod Classification System
The American Welding Society provides a classification system for welding electrodes. This system uses a series of numbers and letters.
Code Part | Meaning |
---|---|
First two or three digits (E.g., 60) | Tensile strength in thousands of pounds per square inch. |
Next digit (E.g., 1) | Positions the rod can be used in. “1” is for all positions. |
Last two digits (E.g., 13) | Type of coating and current suitable for the rod. |
For example, an E6013 code indicates an electrode with a tensile strength of 60,000 psi, suitable for all positions, and a particular type of coating compatible with AC or DC welding currents.
Identifying Suitable Rods For Specific Standards
Every welding job has specific requirements. To select the right rod, match the code to the job’s standards. These include metals types, joint design, and service conditions of the final weldment.
- Match tensile strength: Choose a rod with tensile strength close to or exceeding the base metal.
- Position: Opt for a rod that is labeled for the position required (flat, overhead).
- Coating type: Decide on the proper coating, which affects penetration, slag, and arc stability.
Factors To Consider In Welding Rod Selection
Choosing the right welding rod is essential for a successful weld. The welding rod influences both the welding process and the final weld quality. From the type of welding to the desired weld properties, a wide range of factors come into play. Understanding these factors helps ensure strong, durable, and defect-free welds. Let’s delve into each factor you need to consider.
Type Of Welding
The kind of welding you’ll perform greatly impacts your rod choice. Stick welding, TIG welding, and MIG welding all require different types of rods. For example:
- Stick Welding: Uses consumable electrodes.
- TIG Welding: Requires non-consumable tungsten rods.
- MIG Welding: Involves a continuous feeding wire.
Joint Design
Joint design determines the accessibility and the amount of filler material needed. Evaluate the joint’s geometry before selecting a rod. Consider factors such as:
- Fillet: Requires rods that produce smooth beads.
- Butt: Might need rods that offer deep penetration.
Base Metal
Matching the welding rod to the base metal ensures compatibility and strength. Use a rod with similar mechanical properties to your base metal. For instance:
Base Metal | Recommended Rod |
---|---|
Carbon Steel | E6013, E7018 |
Stainless Steel | E308, E309 |
Welding Position
Position affects rod selection due to gravity and ease of weld. Some rods are specifically designed for certain positions:
- Flat: Almost any rod works.
- Vertical: Need rods with fast freeze characteristics.
Desired Weld Properties
Finally, consider what the completed weld necessitates. Certain rods enhance specific weld properties:
- Strength: Opt for high tensile electrodes.
- Ductility: Choose rods that allow flexibility in the weld.
- Corrosion Resistance: Stainless steel or nickel rods are ideal.

Credit: www.gemathis.com
Choosing The Right Welding Rod For Different Metals
Welding projects demand the right tools. The weld quality depends largely on picking the right welding rod. Metals differ in properties. A suitable welding rod ensures strong bonds between metal pieces. This guide simplifies rod selection for various metals.
Selection For Mild Steel
E6013 is a go-to for welders working with mild steel. This all-position rod features moderate penetration and an easily controlled arc. Its slag also peels off well, making it a user-friendly option for beginners and pros alike.
Selection For Stainless Steel
For stainless steel, E308L rods are suitable. They prevent weld decay thanks to their low carbon content. This rod creates clean welds on 301, 302, and 304 grades, maintaining the metal’s corrosion resistance.
Selection For Aluminum
Aluminum welding calls for specific rod types like the 4043 or 5356 alloys. The 4043 is a preferred choice for general work, offering good fluidity and less sensitivity to weld cracking. The 5356 is stronger but requires higher heat.
Selection For Cast Iron
The NiCl or NiFe type welding rods are excellent for cast iron. They have high nickel content, thus providing flexibility and reducing the risk of cracking. Preheating the cast iron can further optimize results.
Selection For Other Metals
- Bronze: Use a bronze alloy rod suited to the base metal’s composition.
- Copper: A copper-phosphorus rod, like the ERCu filler, offers good flow and a strong joint.
- Hardfacing: Hardfacing rods like the EFeCr-A1 offer abrasion resistance for worn-out equipment.
Special Considerations For Specific Welding Applications
Choosing the right welding rod is crucial for the success and durability of your welding projects. Specific scenarios require special considerations to ensure strong, durable, and defect-free welds. Here are some special considerations for different welding applications.
Welding In High-stress Environments
When welding structures that will face intense stress or impacts, selecting the correct rod is vital.
- Use rods with high tensile strength.
- Look for ‘E7018’ rods for their crack resistance.
Welding Dissimilar Metals
Combining different metals calls for rods that can cope with varied melting points and expansion rates.
- Pick a rod based on the more challenging material.
- Stainless steel to carbon steel? Use ‘309L’ rods.
Welding Thin Metals
Thin materials can warp or burn through unless you use the right rod.
- Lower heat-input rods prevent warping.
- Try ‘E6013’ for controlled penetration.
Welding In Outdoor Conditions
Outdoor welding faces challenges like wind and moisture.
- Shielding gas can be unreliable outdoors.
- Use ‘E6010’ or ‘E6011’ rods for stick welding in the open air.
Welding In Deep Bevels
Deep bevels require electrodes that can reach the bottom and fill the joint completely.
- Choose rods with deep penetration, such as ‘E6010’.
- Multi-pass techniques may be necessary for full coverage.
Budget Considerations
Understanding the impact of your budget on welding projects is vital. Welding rods might seem similar, but prices and performance vary widely. This section will explore how to select the right welding rod without overspending.
Balancing Quality And Cost
Quality welding rods ensure strong welds, but often come at a higher cost. Consider these factors:
- Material compatibility with your project
- Tensile strength needed for the weld
- Type of coating and its impact on the finish
Choose a rod that meets project requirements without excess features to control costs.
Choosing Between Brand Name And Generic Rods
Brand name rods come with reliability but at a premium price. Generic options can be cost-effective, but vary in quality. To decide, check:
- User reviews for performance insights
- Certifications that assure basic quality standards
- Warranty or guarantee offers for peace of mind
Test a small batch of generic rods on non-critical welds to assess suitability.
Evaluating Cost-effectiveness In The Long Run
Cheaper rods can increase overall costs if they lead to frequent rework. Assess the rod’s life span and its impact on workflow. Consider:
Rod Type | Cost | Lifespan | Performance |
---|---|---|---|
Brand Name | Higher | Longer | Consistent |
Generic | Lower | Shorter | Variable |
Select rods that minimize waste and downtime. Investing in quality can save money over time.
Quality Assurance And Certifications
When it’s time to choose a welding rod, the focus shouldn’t just be on the rod’s material and size. Quality assurance and certifications play a vital role in ensuring you get the best results for your welding projects. These elements guarantee the rods meet industry standards and perform under demanding conditions. This section outlines key points to consider for a smart and safe choice.
Recognizing Reliable Brands
Trusted brands stand out in the welding industry. They often have a history of consistent quality and innovation. Look for brands with positive reviews from both professionals and hobbyists. You can rely on user experiences and peer recommendations to gauge a brand’s reputation.
Certifications And Standards To Look For
- American Welding Society (AWS) certification ensures the rod meets specific procedural requirements.
- ISO (International Organization for Standardization) highlights a global standard of quality and efficiency.
- ANSI (American National Standards Institute) sets the benchmark for the safety and quality of welding rods.
These certifications indicate that a welding rod has undergone rigorous testing and meets high-quality standards.
Ensuring Conformance To Safety Regulations
Safety standards protect welders from potential hazards. OSHA (Occupational Safety and Health Administration) provides guidelines that welding rod manufacturers should follow. Ensure the rods are compliant with local safety regulations as well. This conformance signifies the manufacturer’s dedication to user safety and reliability.
Storage And Handling Of Welding Rods
The right storage and handling of welding rods are crucial for maintaining their strength and quality. A welder must know how to keep these materials intact before their application. Proper practices ensure that each welding job begins with the best possible materials, providing the strength and durability needed for the task at hand. Let’s dive into the essentials of storing and handling welding rods.
Proper Storage Conditions
Welding rods require specific conditions to remain in prime condition. Here is how to store them:
- Keep rods dry and cool in a temperature-controlled environment.
- Use sealed containers to prevent exposure to humidity and dust.
- Store away from direct sunlight and heat sources which could cause degradation.
Handling Precautions
Handling welding rods with care is equally important. Follow these guidelines:
- Always wear gloves to protect from oils and moisture from hands.
- Do not bend or drop the rods as this could affect their performance.
- Inspect rods before use for any signs of damage or wear.
Avoiding Moisture And Contamination
Moisture and contamination can weaken welding rods. Implement these strategies:
- Store rods in airtight containers with desiccants to absorb moisture.
- Avoid touching the tip of the rod that enters the weld pool.
- Shield storage areas from environmental contaminants at all times.
Common Welding Rod Selection Mistakes
Selecting the right welding rod is crucial for a strong, durable weld. Choosing poorly can lead to weak joints and wasted effort. Let’s discuss common mistakes welders make during rod selection.
Using The Wrong Rod For The Job
Every welding job is unique and demands a specific rod type. Ignoring this leads to subpar bonds. Welders must consider the base metals and welding positions before deciding. Using the wrong rod can cause cracks or weak welds.
Ignoring Environmental Factors
Environmental conditions affect welding quality. Wind, humidity, and temperature play roles in the welding process. Choose rods that suit the working environment to ensure they perform as expected during the weld.
Neglecting Safety Precautions
Safety should always be a priority. Some rods require special handling due to their composition. Failing to follow safety guides can pose risks to welders. Always read and understand safety data sheets.
Failing To Account For Metal Characteristics
The base metal characteristics are vital. Match the rod to the metal’s properties, like strength and thickness. Incompatible selections can lead to failure in sustaining stress or cause undesired reactions.
Disregarding Rod Storage Conditions
How you store welding rods affects their performance. Moisture and heat can damage rods. Store them in cool, dry places to preserve integrity. Check storage specifications to avoid preventable faults.
Tips For Welding Rod Selection
Choosing the right welding rod is crucial for a successful and strong weld. It affects the quality and the ease of welding. Follow these tips to make the best choice for your project.
Seeking Expert Advice
Seek guidance from professional welders or welding forums. They can provide invaluable insights based on real-world experience. Welding supply stores often have knowledgeable staff to guide you.
Testing Different Rods
- Experiment with various rod types.
- Try them on scrap metal similar to your project material.
- Assess for ease of use and quality of the weld.
Considering Project Requirements
Match the rod to the metal you’re welding. Consider the metal’s type, thickness, and welding position. Each project might need a different type of rod.
Researching Rod Specifications
Add more rows as neededType of Rod | Common Use | Base Metal | Current Type |
---|---|---|---|
E6010 | Pipe Welding | Steel | DC+ |
E7018 | Structural Welding | Steel | AC or DC+ |
Keeping A Rod Selection Chart
Create a chart with information for each rod type. Include details like amperage, position, and material compatibility. This makes future selections easier and quicker.
Welding Rod Selection Faqs
When taking on a welding project, knowing how to choose the right welding rod is vital. Ensuring compatibility and effectiveness, this ‘Welding Rod Selection FAQs’ will guide you to make informed decisions for optimal results in your welding tasks.
Can I Use One Rod For All Metals?
No, one rod does not fit all metals. Different metals have unique properties requiring specific rods. Choosing the correct rod ensures a strong, reliable weld.
Can I Use A Smaller Rod For Thicker Metals?
Using a smaller rod on thicker metals often leads to inadequate penetration and weak joints. Match rod size to metal thickness for best results.
What Happens If I Choose The Wrong Rod?
Selecting the incorrect rod can result in poor weld quality. Issues like cracking, corrosion, or even structural failure can arise on your project.
Are Brand Name Rods Worth The Extra Cost?
Brand name rods typically offer consistent quality and reliability. While more costly, they can provide peace of mind for critical projects.
How Do I Know If A Rod Is Still Usable?
Examine rods for signs of moisture, rust, or damage. Discard compromised rods to avoid flawed welds. Always store rods in a dry environment.
Overview Of Popular Welding Rod Brands
Choosing the right welding rod is crucial for any welding project. The market offers a variety of brands, each with unique features. Knowledge of popular welding rod brands can make or break a project. Here we explore five leading brands that professional welders trust.
Brand A
Brand A stands out with its consistency and performance. Known for durable rods, this brand suits heavy-duty tasks. Welders rely on Brand A for stainless steel and aluminum projects.
Product | Material Compatibility | Application |
---|---|---|
A-100 | Stainless Steel | Construction |
A-200 | Aluminum | Automotive |
Brand B
Brand B is known for its versatility. It offers a wide range of rods, ideal for both beginners and experts. Its rods are perfect for small repairs and DIY projects.
- Easy to use
- Excellent for learning
- Good for home repairs
Brand C
When precision is key, Brand C shines. The rods from Brand C provide clean welds and are preferred for fine metalwork. Artists and decorators love this brand.
- High precision welding
- Minimal splatter
- Great for art projects
Brand D
For those tackling outdoor projects, Brand D’s rods are unmatched. They offer strong resistance to the elements. Use Brand D for outdoor fixtures and garden structures.
- Weatherproof
- Rods can handle rain and sun.
- Durable
- Ideal for long-term outdoor use.
Brand E
Brand E is the top choice for industrial jobs. It offers high-grade rods that withstand extreme conditions. Miners and heavy machinery operators rely on Brand E.
Comparing Welding Rod Prices
Embarking on a welding project but unsure about which welding rod to select? The price can be a deciding factor. This section will guide you through the various price points, what affects them, and how to get the best bang for your buck.
Price Range Of Different Types
Welding rods come in diverse types. Each serves a specific purpose. Here’s an overview:
Type | Price Range |
---|---|
6010 | $10 – $30 per pound |
6011 | $15 – $25 per pound |
6013 | $8 – $22 per pound |
7018 | $20 – $40 per pound |
7024 | $25 – $50 per pound |
Factors Affecting Rod Prices
Different elements sway welding rod prices. Key factors include:
- Material composition: More exotic materials often lead to higher costs.
- Brand reputation: Well-known brands might charge more.
- Rod size and packaging: Larger quantities can result in lower per-unit prices.
- Special features: Such as low-hydrogen or all-position rods may fetch a premium
Value For Money Considerations
Do not judge by price alone. Consider these aspects:
- Match rod to the job: Select a rod that is suited to the workpiece and the welding position.
- Assess longevity: Some rods last longer or perform better, saving money over time.
- Read reviews: User feedback can be a valuable guide to the rod’s performance and worth.
- Bulk purchase: Consider bulk pricing, especially on larger projects.
Smart choices lead to effective welding without unnecessary costs.
Troubleshooting Welding Rod Selection Issues
Struggling with welding rod selection? Proper welding rod selection can make or break your welding job. Choosing the wrong rod can lead to numerous issues, affecting both the efficiency of your work and the integrity of the weld. Let’s troubleshoot common selection problems and find the ideal stick for your project.
Problems With Stickiness
Welding rods sticking to metal could point to a few key issues. A low amperage setting or an incorrect rod angle might be culprits. Here’s a quick fix:
- Check your amperage and adjust higher if necessary.
- Hold the rod at a proper angle, typically between 15 to 30 degrees.
Rod Breakage
Rod breakage can halt production. This often stems from improper storage leading to rod moisture. Keep rods dry using these tips:
- Store in a dry environment.
- Use a rod oven if available.
- Follow the manufacturer’s storage guidelines.
Excessive Spatter
Spatter means more cleanup and could indicate several potential issues. To minimize spatter:
- Opt for the right amperage; too high or too low can cause problems.
- Ensure the rod’s flux has not absorbed moisture.
- Use a consistent work angle and travel speed.
Inconsistent Arc
Inconsistent arcs lead to frustrating welding sessions and can arise from using an incompatible rod type for the material or incorrect terminal settings. Solve it with these steps:
- Match the rod to the base material and job requirements.
- Check your machine’s terminal settings and adjust.
Poor Weld Quality
Poor welds compromise the entire structure. When facing poor weld quality:
Cause | Solution |
---|---|
Incorrect rod size | Select rod size based on material thickness. |
Wrong current type | Choose between AC or DC based on rod and material type. |
Impure metal surfaces | Clean the surface thoroughly before welding. |
Advancements In Welding Rod Technology
Welding is a craft that continually benefits from technological progress. Advancements in Welding Rod Technology make modern welding safer, more efficient, and adaptable to a variety of materials. These developments help welders to tackle a wider range of projects with confidence.
Introduction Of New Materials
Traditional welding rods have seen a revolution with the introduction of new materials. These materials offer improved strength, durability, and heat resistance. Innovations include:
- Rare earth elements that stabilize the arc and improve weld quality.
- Lightweight composites which reduce user fatigue.
- Alloys tailored for specific industries, enhancing performance.
Improved Coating Formulations
The coating of welding rods is essential for protection and performance. New formulations have improved these aspects:
Aspect | Improvement |
---|---|
Arc stability | Coatings now facilitate a more consistent arc. |
Slag control | Enhanced coatings allow for easy slag removal. |
Weld appearance | New coatings contribute to neater, smoother welds. |
Enhanced Welding Performance
At the core of these advancements lies the goal to enhance welding performance. Outcomes include:
- Higher deposition rates, meaning faster welding.
- Better penetration for stronger joints.
- Reduction in welding fumes for a healthier environment.
Future Trends In Welding Rod Selection
As we forge ahead, the world of welding evolves at a rapid pace. Selecting the perfect welding rod is critical for any welding project. Let’s dive into the future trends of welding rod selection that are set to revolutionize the industry.
Automation And Robotics
The advent of automation and robotics in welding is a game-changer. Robots offer precision and consistency, leading to stronger welds. As robots take center stage, the demand for specialized welding rods rises. These rods must meet the rigorous standards set by automated processes. The future holds an emphasis on welding rods that work seamlessly with robotic technology.
Environmentally Friendly Options
Environmental concerns shape the future of welding. Manufacturers now develop eco-friendly welding rods with reduced harmful emissions. These innovative rods promise to lower the carbon footprint of welding activities. Expect to see an increase in these environmentally friendly options, enhancing sustainability in the welding industry.
Integration With Smart Welding Systems
Smart welding systems are emerging as a pivotal trend. Integration capabilities between welding rods and smart systems ensure optimal performance. Real-time data tracking and feedback loops characterize these smart systems. They dictate the choice of welding rods that can communicate and adapt within such intelligent frameworks.
Frequently Asked Questions For How To Choose A Welding Rod
What Size Welding Rod Should I Use?
Select a welding rod size based on the thickness of the materials you’re joining. Generally, use a rod with a diameter that matches the thickness of the metal pieces. For most jobs, rods ranging from 1/16-inch to 1/4-inch in diameter are suitable.
Always refer to the manufacturer’s guidelines for specific projects.
How Do I Choose The Right Electrode?
To choose the right electrode, consider the metal type, welding position, required strength, and joint design. Select an electrode compatible with the base metal and the desired weld quality.
What Rod Is Better 6011 Or 7018?
The choice between 6011 and 7018 welding rods depends on the task. The 6011 rod excels in penetrating rusty or dirty metal, while the 7018 rod is better for clean, precise welds requiring higher strength.
What Are The 2 Characteristics You Should Look For When Selecting An Electrode?
Select electrodes based on material compatibility with the workpiece and the electrode’s conductivity and durability for the intended application.
Conclusion
Selecting the right welding rod is crucial for the success of your welding projects. Understanding the material, thickness, and welding position guides your choice. With careful consideration, the perfect match enhances durability and performance. Embrace these tips for top-notch welding outcomes every time.
Happy welding!