To pin and weld the flash hider, secure it to the barrel and weld over the pin to make it permanent. Ensure that the device is aligned before welding.
Pin and welding a flash hider is an essential process for those looking to comply with certain firearms regulations. This technique effectively creates a non-removable attachment of a muzzle device to a rifle barrel. The goal is to meet the legal length requirement for rifles without permanently altering the barrel’s length.
Pinning and welding are considered a complex procedure and should be carried out with precision to maintain the firearm’s functionality and safety. It’s not just about compliance; the correct installation also preserves the rifle’s shooting accuracy. Enthusiasts and gunsmiths alike approach this task with great attention to detail, making sure that the pinning is secure and the welding is clean, ensuring that the firearm meets legal standards while maintaining its efficacy and integrity.
Tools And Materials
Gearing up to pin and weld a flash hider? It’s crucial to gather the right tools and materials beforehand! This ensures a flawless installation. Pinning and welding can look intimidating, but with everything in place, it’s straightforward. Let’s explore what’s essential for the job.
Required Tools
To begin, assembling the necessary tools guarantees a smooth operation. Each has a specific role to make the process seamless. Safety, precision, and reliability hinge on these critical instruments. Here’s what to have ready:
- Drill press: For precise drilling.
- Drill bits: Match these to the pin size.
- Welding machine: A must for the weld.
- Calipers or micrometer: For exact measurements.
- Hammer and punch set: To place the pin.
- Welding mask and gloves: Your safety comes first.
- Files: To smooth any rough edges after pinning.
Materials Needed
With the tools ready, gather these materials to ensure a strong, legal bond between the flash hider and the barrel. Make sure to double-check everything before starting:
- Flash hider: The main component to be installed.
- Crush washer or shims: For proper alignment.
- Pin: To secure the flash hider.
- Welding rods or wire: To create the weld.
- Cleaning solution: For residue-free metal surfaces.
- Marker or tape: To mark drilling points.
Ready your workspace and let’s get to pinning and welding that flash hider with confidence!
Preparation
The art of pinning and welding a flash hider is a meticulous process. Preparation paves the way for a successful installation. Properly preparing the workspace, equipment, and components is vital. Let’s dive into the initial steps to ensure everything is set for a secure and safe attachment of your flash hider.
Safety Measures
Handling firearms and performing modifications demand strict safety protocols. Always check and double-check that the firearm is not loaded. Equipping oneself with safety gear is non-negotiable.
- Wear safety glasses to protect your eyes from metal shavings and sparks.
- Ear protection is essential when working with power tools.
- Keep a fire extinguisher nearby as a precautionary measure.
- Ensure a well-ventilated workspace to avoid inhaling any harmful fumes.
Preparing The Flash Hider
Choosing the correct flash hider and gathering the necessary tools form the foundation of this project. A well-prepped flash hider equates to a smoother installation process.
- Select the appropriate flash hider for your rifle’s calibre and thread.
- Use calipers to measure the diameter of the barrel and threads to ensure a precise fit.
- Clean the threads on the barrel and flash hider to remove any debris or grease.
- Gather the tools you’ll need: a drill, a set of bits, a pin, a welder, and proper tools for securing the firearm.
With safety measures in place and the flash hider prepared, you’re almost ready to begin the pinning and welding process.
Pinning Process
Welcome to the crucial stage in securing a flash hider to your firearm barrel: the Pinning Process. This enduring method ensures a non-removable, ATF-compliant muzzle device. Let’s dive into how to set your flash hider in place properly.
Drilling The Pin Hole
Start with a well-secured barrel and flash hider. Align the flash hider precisely for the best results. Choose a drill bit slightly smaller than your pin. Carefully drill through the flash hider and into the barrel. Ensure the hole is straight and clean.
Inserting The Pin
After drilling, you’ll need to insert your pin. Opt for a solid steel pin for strength. Tap the pin gently into the hole until it sits flush with the flash hider.
Welding Process
The welding process to pin and weld a flash hider is crucial for compliance with firearms regulations. It permanently attaches the muzzle device to the barrel. This guide explains how to apply heat-resistant material and weld the pin effectively. Proper tools and expertise are necessary to ensure a safe and secure attachment.
Applying Heat Resistant Material
Before beginning the welding process, prepare the flash hider and barrel. Apply a heat-resistant material to protect the barrel’s finish. This step maintains the barrel’s integrity during high-heat welding.
- Clean the flash hider and barrel surface.
- Wrap the barrel with a heat-resistant tape.
- Ensure full coverage to prevent heat damage.
Welding The Pin
With the heat-resistant material in place, focus on the pin. The pin secures the flash hider to the barrel. It keeps the device in position during welding.
- Insert the pin into the pre-drilled hole.
- Align the flash hider with the barrel.
- Check for a tight fit to prevent movement.
Now, weld the pin onto the flash hider and barrel. Use a high-precision welding tool for this task. A solid weld is necessary for durability and compliance.
Step | Action | Check |
---|---|---|
1 | Start the weld at the pin’s base | Ensure even distribution of heat |
2 | Continue the bead around the pin | Avoid overheating the area |
3 | Inspect the weld for completeness | Confirm the pin is securely fused |
Finish the process by cleaning the welded area. Remove any excess material to maintain a smooth finish. Exercise great care throughout the welding process to ensure lasting results.
Quality Check
Pin and weld flash hiders are crucial for firearm safety and compliance. Performing a thorough quality check after installation ensures reliability. This section guides you through inspecting your work for excellence.
Inspecting The Weld
Inspecting the weld is the first step in the quality check process. Look for these signs:
- Consistent Weld Patterns: The weld should show uniformity.
- No Cracks or Gaps: A perfect weld has no visible defects.
- Clean Finish: Excess material should not be present around the weld.
Use a magnifying glass to spot any small issues. A smooth, continuous weld indicates a job well done.
Testing Stability
Testing the stability of the flash hider is critical. Follow these steps:
- Physical Check: Try moving the flash hider by hand. It should not budge.
- Visual Inspection: Check alignment with the barrel. Misalignment can affect firearm performance.
A stable, well-aligned flash hider signifies successful pinning and welding. Trustworthy performance in the field begins with meticulous quality control at the workbench.
Troubleshooting
Welcome to the ‘Troubleshooting’ section of our pin and weld flash hider guide. Sometimes, even with the best instructions, things don’t go as planned. Below, you’ll find solutions to common problems and advice on when it’s time to call in the pros.
Addressing Common Issues
Encountering difficulties during a pin and weld job is not uncommon.
- Misalignment: This happens if the hider isn’t straight.
- Pin won’t fit: Sometimes the pin is too large or too small.
- Weld issues: Poor welds can lead to failure.
Fix misalignment by starting over. Remove the hider and realign it.
If the pin doesn’t fit, measure its diameter. Use a pin that matches the hole size.
To address weld problems, clean the area thoroughly. Use the right tools and techniques.
Seeking Professional Help
Sometimes, DIY solutions don’t cut it.
- Safety concerns: Imperfect pin and welds may pose a risk.
- Legal issues: Regulations can be stringent.
- Lack of tools: Professional equipment makes a difference.
Find a licensed gunsmith with experience in pin and weld projects.
They ensure compliance with laws and have the necessary tools.
Experts correct mistakes and provide peace of mind.
Legal Considerations
Modifying firearms requires careful adherence to the law. Each step, from choosing a flash hider to the pinning and welding process, demands compliance with state and federal regulations. It’s essential to know these legal boundaries to avoid penalties or even criminal charges. This guide focuses on what the law says about such modifications and what gun owners need to know.
Understanding State Regulations
Not all states view firearm modifications the same way. Some have stringent rules governing the length of rifles and the types of allowable attachments.
- Check state laws concerning barrel length.
- Identify regulations on flash hiders.
- Verify if a pin and welded muzzle device is permanent.
Pinning and welding can alter a firearm to meet legal length requirements. This is often because regulations define a minimum overall length for a rifle. Knowing your state’s specifics is critical before starting the modification process.
Compliance With Firearm Laws
Federally, firearms are regulated by several laws, including the Gun Control Act and the National Firearms Act. Under these laws, rifles must adhere to specific guidelines to remain compliant. Here’s a brief checklist for compliance:
- Ensure your rifle’s barrel is at least 16 inches long, as required by federal law.
- If pinning and welding, make certain the overall length meets legal standards with the attachment included.
- Document the modification process for future reference and possible inspection.
Always keep the legality front of mind. Seek out a professional gunsmith for modifications like pinning and welding if uncertain. Their expertise ensures both the quality of work and legal compliance.
Comparison With Other Methods
When customizing firearms, options like pin and weld or alternative attachment methods each have pros and cons. This section helps you compare different ways to attach flash hiders to your rifle barrel.
Pinning And Welding Vs. Adhesives
Pinning and welding is a permanent method to secure a flash hider onto a rifle barrel. Unlike using adhesives, this method guarantees durability and compliance with legal length requirements. Adhesives can degrade over time, challenging the reliability of the attachment. The pin and weld process entails drilling, inserting a metal pin, and welding it in place, creating a long-lasting bond unaffected by temperature or solvents.
Pinning And Welding Vs. Threaded Attachments
While threaded attachments offer a simpler attachment method, pinning and welding surpasses them in terms of security. Threaded flash hiders can become loose over time or during recoil. This requires regular maintenance to ensure they stay tight. In contrast, pinning and welding eliminates the possibility of loosening, creating a fixed, non-removable attachment that stands up to heavy use.
Method | Durability | Maintenance | Legality for Length |
---|---|---|---|
Pinning & Welding | High | Low | Compliant |
Adhesives | Medium to Low | High | Varies |
Threaded Attachments | Medium | Medium to High | Non-Compliant |
- Pinning and welding permanence adds compliance and safety.
- Adhesives might fail due to heat or solvent exposure.
- Threaded attachments need checking and might loosen unexpectedly.
- Drill hole in flash hider and barrel.
- Insert metal pin in the hole.
- Weld over the pin to seal the flash hider to the barrel.
Enhancing Aesthetics
When customization meets function, you get a perfectly pinned and welded flash hider that looks sharp. It’s not just about muzzle control; it’s about creating a unique presence for your rifle. The right finish on your flash hider takes your firearm from ordinary to outstanding. The process may seem technical, but the visual payoff is huge.
Options For Finishing
Picking the right finish is crucial for achieving a sleek look. Below, a range of finishes breathe life into your rifle’s aesthetics:
- Black Oxide: Offers a classic matte look.
- Stainless Steel: Shines with a polished, high-end appeal.
- Cerakote: Provides color options for personal flair.
- Nitride: Delivers hardness with a satin sheen.
Each finish has its pros and cons. Select one that complements your rifle’s style and durability needs. The pin and weld process does not limit finish options.
Maintaining The Appearance
Maintenance ensures your rifle stays looking its best. Follow these tips for upkeep:
- Clean Regularly: Wipe down the flash hider after use.
- Touch-Up Kits: Keep one handy for scratches.
- Avoid Harsh Chemicals: They may damage the finish.
Regular maintenance guards against wear and tear. A well-kept flash hider helps the rifle retain its distinctive look for years.

Credit: issuu.com
Benefits Of Pinning And Welding
The process of pinning and welding a flash hider to a firearm brings key advantages. It’s not only about making your rifle look great. It’s also about improving its performance and staying within legal boundaries. Let’s dive into two significant benefits of this technique.
Improved Muzzle Stability
Shooting precision matters when you’re at the range or in competition. By pinning and welding the flash hider, you get a permanent, secure attachment. This limits any movement caused by recoil or vibration. Your performance enhances with a stable muzzle end. Better accuracy and control during rapid fire can make all the difference.
Compliance With Barrel Length Regulations
Without Pinning & Welding | With Pinning & Welding |
---|---|
Potential Legal Issues | Legally Compliant Rifle |
Shorter Barrel Length | Barrel Extends Legally |
Risk of Modification Limits | Enhanced Customization Freedom |
Striking a balance between customization and legal requirements is crucial. In the US, rifles must have a barrel length of at least 16 inches. A flash hider, when pinned and welded, becomes part of the barrel. This extends the barrel length. It often eliminates the need for a lengthy NFA registration process. Ensure legal compliance while enjoying your rifle to its fullest potential.
Risks And Limitations
Knowing how to pin and weld a flash hider is crucial for gun enthusiasts. This process permanently attaches the hider to the barrel. It’s not just about the method; a deeper understanding is necessary. There are risks. We should know these before starting the work.
Potential Damage To Threads
Thread damage is a real risk when pinning and welding a flash hider. Careless work can wreck the barrel’s end. Think about it—barrel threads are fine, precise, and vital. They need a perfect fit with the hider. Rough handling may cause:
- Stripped threads
- Cross-threading
- Irreversible damage
This is not just about looks. Damaged threads can lead to poor device fitment. They may even make the gun unsafe to use.
Incompatibility With Some Muzzle Devices
Not all muzzle devices are the same. Each has a design that might not work well with pinning and welding. Before starting, check if your hider is suitable. Some devices are:
Device Type | Compatibility |
---|---|
Flash Hiders | Often compatible |
Muzzle Brakes | May have issues |
Suppressor Mounts | Rarely suitable |
Choose the right type and make sure it fits. Forcing an incompatible device can also damage your gun. Always consult with professionals if doubt seeps in.
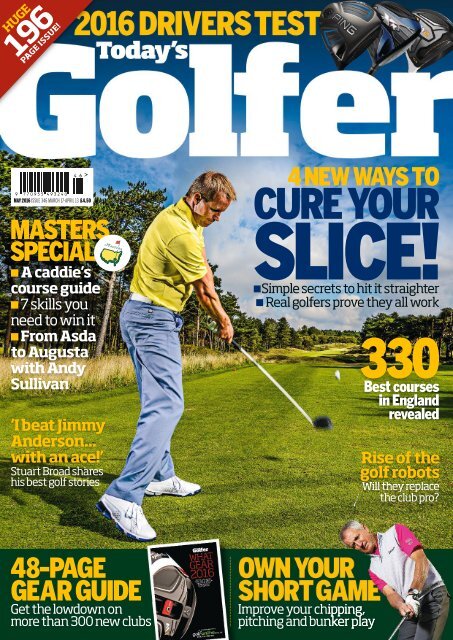
Credit: www.yumpu.com
Cost Analysis
Understanding the costs involved in pinning and welding a flash hider is crucial. It ensures you’re not caught off guard financially. This section breaks down the expenses. It guides you through saving money while achieving the best results.
Comparing Costs Of Different Methods
The market offers multiple ways to secure a flash hider to your firearm. Each method comes with its own price tag.
- DIY Approach: Cost of tools and materials only
- Professional Gunsmith: Labor plus materials
- Off-the-Shelf Kits: One-time purchase
Method | Materials | Labor | Total Cost |
---|---|---|---|
DIY | $20-$50 | $0 | $20-$50 |
Professional | $20-$50 | $50-$100 | $70-$150 |
Kits | $30-$80 | $0 | $30-$80 |
Remember to account for hidden costs. These could include shipping for kits or travel to a gunsmith.
Long-term Economic Benefits
Investing in a pin and weld job extends beyond the initial payment.
- Durability: A professional job might cost more, but it lasts longer.
- Regulation Compliance: Avoid legal fees by meeting state laws.
- Resale Value: A well-done modification can increase your firearm’s market value.
Consider the return on investment. Durable work prevents frequent repairs, saving money over time.
Step-by-step Guide
Ready to secure your flash hider for good? This guide breaks down the pinning and welding process into manageable steps. Follow along for a smooth and compliant installation.
Detailed Instructions For Pinning
First, gather your tools: You’ll need a drill, a vice, a hammer, and a pin. Make sure your workspace is well-lit and organized.
- Secure the firearm in the vice. Ensure it’s tight to avoid movement.
- Align the flash hider with the barrel’s threads. Screw it on by hand until snug.
- Mark the spot on the flash hider where the pin will go. The mark should line up with the barrel’s hole.
- Drill through the marked spot on the flash hider. The hole should align with the barrel’s hole.
- Insert the pin into the hole. Tap it with a hammer until it’s flush with the flash hider.
Detailed Instructions For Welding
With the pin in place, it’s time to weld. You’ll need a welder, protective gear, and proper ventilation.
- Prepare your welder. Set it to the appropriate settings for your material.
- Don your welding mask and gloves for safety.
- Position the welder’s tip over the pin’s end. Aim for a clean contact point.
- Apply the weld. Keep it small and concentrated on the pin and flash hider.
- Inspect your work. Look for a solid weld that fully encapsulates the pin.
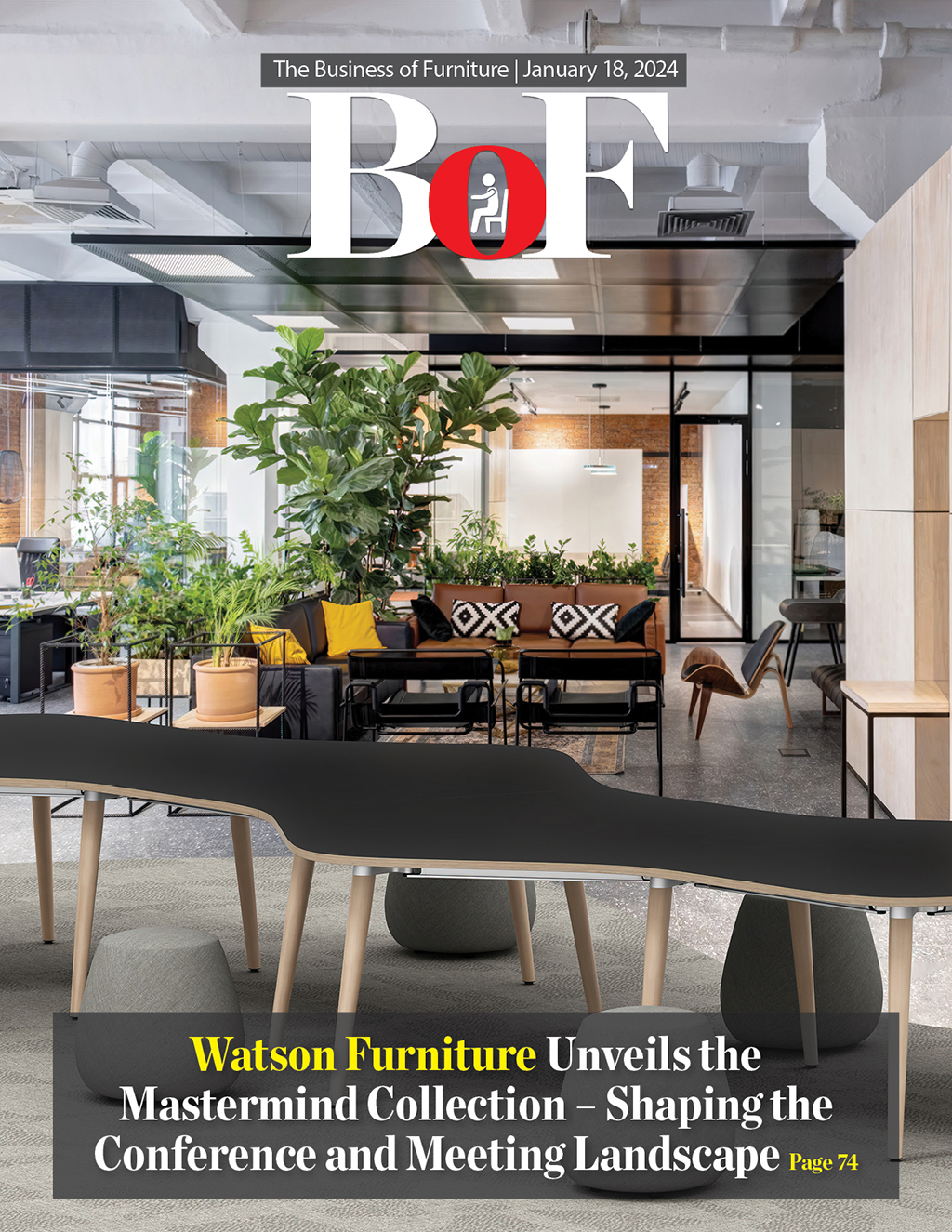
Credit: bellow.press
Case Studies
The process of pinning and welding a flash hider can be intricate. Yet, many have mastered it with flying colors. This section explores real-life situations where skill met challenge. Discover tales of triumph and lessons learned from the trenches of firearm customization. Here’s a deep dive into the case studies of those who ventured into the pin and weld world.
Success Stories
- John’s Precision Rifle: Achieved a shorter barrel without compromising legality.
- Alice’s Home Workshop: Blended artistry with functionality in her rifle’s design.
- Team Competitor’s Edge: Enhanced performance, securing top ranks in competitions.
Challenges Faced And Overcome
Challenge | Solution |
---|---|
Misaligned Pin Holes | Utilized precision drilling tools and fixtures. |
Weld Imperfections | Mastered weld techniques and temperature control. |
Regulatory Compliance | Thoroughly reviewed local firearm laws. |
Future Trends
The ever-evolving firearm industry continuously integrates new technology, leading to significant developments in customization options like pinning and welding flash hiders. Let’s shed light on what the future holds for this sector.
Advancements In Pinning And Welding Technology
With technology progressing rapidly, enthusiasts can expect enhancements in the precision and efficiency of pinning and welding. These advancements may include:
- Automated welding systems for consistent, high-quality joins
- Laser welding techniques offering cleaner, more discreet welds
- Improved pin materials that withstand high temperatures without fail
Innovative tools and equipment will further streamline the process, making DIY projects more accessible to gun owners.
Potential Regulatory Changes
As firearm laws adapt, regulations regarding modifications like pinning and welding flash hiders could shift. Potential changes may involve:
- New certification requirements for those performing the work
- Stricter guidelines on the types of permissible flash hiders
- Documentation and reporting procedures to track modifications
Owners and gunsmiths must stay informed about such regulatory adjustments to remain compliant.
Faqs
Welcome to our FAQs, your one-stop destination for all questions about pinning and welding flash hiders. Here, you will find a thorough breakdown of commonly asked questions alongside expert answers designed to guide you through the pin and weld process.
Common Questions About Pinning And Welding
- What is pinning and welding a flash hider?
A method to permanently attach a flash hider to a rifle barrel.
- Why do gun owners pin and weld flash hiders?
To comply with legal barrel length requirements.
- Can I pin and weld a flash hider myself?
Possible, but requires skill and proper tools.
- Does pinning and welding affect firearm performance?
Generally no impact on performance when done correctly.
- Can a pinned and welded flash hider be removed?
Yes, but requires cutting the weld and removing the pin.
Expert Answers
- Duration for pinning and welding a flash hider:
Varies by skill, typically takes 30 minutes to an hour.
- Tools needed for the process:
- Drill
- Drill bit matching the pin diameter
- Welder
- Calipers or a measuring tool
- Best type of pin for the job:
Steel dowel pins are often used for their strength and durability.
- Legal considerations:
Always check local and federal law before modifying firearms.
- Importance of precise measurement:
Critical for proper alignment and legal compliance.
Frequently Asked Questions For How To Pin And Weld Flash Hider
Can A Gunsmith Pin And Weld?
Yes, a gunsmith can pin and weld components, typically to comply with firearm regulations or to securely attach parts like muzzle devices to a firearm barrel.
Does Flash Hider Have To Be Pinned?
Flash hiders don’t typically require pinning, but local laws may mandate this for certain firearms to comply with regulations. Always check your jurisdiction’s requirements.
Does A 14.5 Barrel Have To Be Pinned?
Yes, a 14. 5-inch barrel typically must be pinned with a muzzle device to meet the legal 16-inch minimum length requirement for rifles under U. S. federal law.
What Does Pinned And Welded Mean?
Pinned and welded refers to a process where a gun barrel and a muzzle device are permanently attached. This technique often ensures compliance with legal barrel length requirements.
Conclusion
Mastering the pin and weld technique for flash hiders is within your grasp. This guide has aimed to demystify the process, ensuring a robust and compliant firearm. Remember, safety and precision are key. Embrace practice and patience, and your skills will flourish.
For firearm longevity and legal peace of mind, perfecting this method is invaluable. Happy shooting!