TIG welding often provides stronger, higher quality welds than MIG welding. TIG welds are particularly prominent in applications requiring precision and strength.
Delving into the world of welding, one commonly confronts the question of the relative strength between TIG (Tungsten Inert Gas) and MIG (Metal Inert Gas) welding. As two prevalent techniques, each offers unique advantages, catering to different needs within the welding sector.
TIG welding excels by using a non-consumable tungsten electrode to produce the weld, which allows for stronger, cleaner joins. This method’s precision and control make it ideal for high-quality applications in aerospace, sculptural art, and piping systems. MIG welding, on the other hand, is known for its speed and ease as it uses a continuously feeding wire, making it a go-to for projects requiring efficiency and cost-effectiveness. Despite the situational preferences, TIG’s mastery in strength and precision remains a cornerstone in specialized welding tasks.

Credit: medium.com
Historical Background
The origins of welding processes intrigue many. The profound impact they’ve had on fabrication industries is undeniable. Understanding how TIG and MIG welding began offers insights into their strengths today.
Origin Of Tig Welding
TIG welding’s birth dates back to the 1940s. Its name, Tungsten Inert Gas, reveals its components. A tungsten electrode creates the weld in this process. The surrounding inert gas protects the weld from contamination.
- Invented for aircraft manufacturing during World War II.
- Boosted the strength of airplane parts.
- Allowed for precise, high-quality welds on crucial components.
Renowned for precision, TIG welding paved the way for aerospace and other industries demanding accuracy.
Origin Of Mig Welding
MIG welding emerged around the same time as TIG. Standing for Metal Inert Gas, it also uses an inert gas shield. However, a wire electrode melts into the weld, creating the joint.
Year Developed | Purpose | Impact |
---|---|---|
1940s | Designed for joining non-ferrous materials. | Changed mass production with its efficiency. |
Valued for speed and ease, MIG welding revolutionized how industries approached production.
Process And Technique
Understanding the Process and Technique is crucial when comparing TIG and MIG welding. Welders often debate which method is stronger. Let’s delve into their processes and techniques to see how they stack up.
Tig Welding Process
TIG welding, or Tungsten Inert Gas welding, uses a tungsten electrode to produce the weld. The welder holds a torch in one hand and a filler rod in the other. Argon gas shields the weld area from contaminants.
Mig Welding Process
On the other hand, MIG welding, or Metal Inert Gas welding, involves feeding a wire electrode continuously. This wire melts and joins materials together. MIG uses a mix of argon and carbon dioxide to protect the weld.
Techniques For Tig Welding
- Control the Heat: Use a foot pedal or thumb control to manage the heat input precisely.
- Clean Thoroughly: Prep the base metal and filler rod to prevent contamination.
- Consistent Movement: Move the torch steadily to create even welds.
Techniques For Mig Welding
- Maintain a Stable Speed: Keep wire feed speed consistent for uniform welds.
- Correct Angle: Hold the torch at an appropriate angle for proper penetration.
- Test Settings: Adjust voltage and tension before starting on the workpiece.
Strength And Durability
Understanding the strength and durability of TIG and MIG welding is critical. These factors determine the longevity and reliability of welded structures. Let’s explore these aspects in depth for both TIG and MIG welds.
Strength Of Tig Welds
TIG welding, known for precision, creates strong bonds in metals. It uses tungsten electrodes which heat metals and form a robust weld. Metals fuse without filler materials sometimes, making the welds very pure. Here’s why TIG welds are strong:
- Low contamination risk due to the inert gas shield.
- High-temperature control allows for stronger welds.
- Welds are consistent and clean.
Strength Of Mig Welds
MIG welding excels in versatility and speed. It involves feeding a wire electrode continuously to form the weld. This technique has its strengths:
- Good for thick and thin metals.
- Faster process for longer welds.
- Simple to learn and apply, leading to fewer errors.
Durability Of Tig Welds
Durability is where TIG welding shines. It’s often used where weld integrity is paramount. Quality TIG welds resist wear and tear due to:
- Controlled heat yielding stable welds.
- Strong resistance to corrosion.
- Excellent for high-stress applications.
Durability Of Mig Welds
MIG welds also offer impressive durability, suitable for many applications:
Factor | Impact on Durability |
---|---|
Speed | Quick welds can lead to good bond strength. |
Versatility | Welds a variety of metals effectively. |
Wire Electrode | Continuous feed creates consistent welds. |
Application And Versatility
Understanding the right welding process is crucial for the success of any metal fabrication project. Often, the choice comes down to two popular methods – TIG (Tungsten Inert Gas) and MIG (Metal Inert Gas) welding. Each technique shines in varied settings. Let’s explore their applications and versatility.
Applications Of Tig Welding
The precision of TIG welding makes it the go-to for tasks requiring fine detailed work or high-quality finishes. Its applications include:
- Aerospace components
- Decorative pieces
- Repair work on small parts
- Creation of intricate art sculptures
Applications Of Mig Welding
MIG welding, known for its speed and efficiency, covers a broad spectrum of uses:
- Automotive production and repairs
- Construction projects
- Shipbuilding
- Heavy-duty metal fabrication
Versatility Of Tig Welding
TIG welding is incredibly versatile, with its ability to join a wide range of metals:
Metal Type | Usage |
---|---|
Stainless Steel | Food processing equipment |
Aluminum | Bicycle frames |
Magnesium | Aerospace parts |
It also allows for the complexity of welding dissimilar metals together.
Versatility Of Mig Welding
Due to its straightforward approach, MIG welding accommodates beginners and professionals alike. Its versatility is linked to various factors:
- Quicker learning curve for new welders
- Adaptable to both thin and thick metals
- Indoor and outdoor usage with the appropriate setup
MIG welding simplifies the process for many projects and is a staple in multiple industries.
Quality And Precision
Understanding the strength of welds involves more than just the method used. The quality and precision of welds are key factors that determine their strength and reliability. Both TIG (Tungsten Inert Gas) and MIG (Metal Inert Gas) welding have unique advantages. Exploring these will reveal which method leads to superior welds.
Quality Of Tig Welds
TIG welding is known for its high-quality finishes. It uses a non-consumable tungsten electrode to produce the weld. This method allows welders to carefully control the heat and the weld pool. This precision results in strong and clean welds without spatter.
- Less distortion in the metal being welded.
- Superior aesthetic quality with neat and smooth welds.
- Ability to weld thin materials effectively.
Quality Of Mig Welds
MIG welding is faster and can handle thicker materials. It uses a continuous wire feed, which acts as a filler material. MIG is great for mass production. Consider the following points:
Parameter | MIG Welding |
---|---|
Weld strength | Consistent for thicker materials |
Speed | Quick and efficient |
Usability | Suitable for beginners |
Precision In Tig Welding
In TIG welding, the heat input can be finely tuned. This allows for intricate work on delicate projects. Critical components that require meticulous attention to detail often rely on TIG welding. Some advantages include:
- Controlled penetration for thin workpieces.
- Ability to work with a wide range of metals.
- Minimal weld defects leading to fewer reworks.
Precision In Mig Welding
MIG welding offers a balance between speed and precision. The continuous wire feed creates consistent beads and can be adjusted for different thicknesses. Some key points include:
- Effectiveness with long, straight welds or curved ones.
- Good for projects not requiring extreme precision.
- High productivity in less critical applications.
Cost And Efficiency
Understanding the cost and efficiency of welding methods is crucial. Tig and Mig are popular, but which is more cost-effective and efficient?
Cost Comparison Between Tig And Mig Welding
When choosing between TIG (Tungsten Inert Gas) and MIG (Metal Inert Gas) welding, cost matters.
TIG welding is known for its precision. Its equipment is pricier due to specialized tools. MIG welding, on the other hand, moves faster and doesn’t demand as much skill, making it generally less expensive.
- TIG welders: Higher upfront investment
- MIG welders: More affordable, consumables cost less
Type of Welding | Equipment Cost | Consumables Cost |
---|---|---|
TIG Welding | Higher | Higher |
MIG Welding | Lower | Lower |
Efficiency Comparison Between Tig And Mig Welding
The efficiency of TIG versus MIG welding has distinct differences.
TIG welding is meticulous and perfect for delicate jobs. It ensures precision but at a slower pace. Conversely, MIG welding is all about speed. It suits large-scale projects where time is of the essence.
- TIG: Best for complexity not rushed
- MIG: Ideal for quicker, repetitive welds
Type of Welding | Job Precision | Speed |
---|---|---|
TIG Welding | High | Low |
MIG Welding | Medium | High |
Welding Speed And Productivity
Understanding welding speed and productivity is crucial when comparing TIG to MIG welding. Each method has its strengths and best use cases. Let’s dive into how quickly and efficiently you can weld with TIG and MIG.
Welding Speed In Tig Welding
TIG welding is known for its precision. Because of this, it is not the fastest welding technique. In TIG welding, welders add filler metal by hand. This process requires great skill and focus.
Welding Speed In Mig Welding
MIG welding excels in speed. A wire feeding system pushes filler metal through the wand. This means a continuous weld can be made without stopping. MIG welding allows for faster completion of projects.
Productivity In Tig Welding
TIG welding’s slow speed might make it seem less productive. But its strength lies in the quality of the weld. This method is perfect for intricate and high-quality jobs. Such jobs need attention to detail.
Productivity In Mig Welding
The faster welding speed of MIG increases overall productivity. This allows for a higher output of welds in a given time. MIG is often chosen for large-scale or time-sensitive projects where speed is key.
Aspect | TIG Welding | MIG Welding |
---|---|---|
Speed | Slower | Faster |
Productivity | High-quality, less quantity | More quantity, efficient |
- TIG is precise and high-quality.
- MIG is quick and efficient.
- Choose TIG for precision.
- Choose MIG for speed.
Skill Requirement
The art of welding requires precision and skill, whether you lean towards TIG (Tungsten Inert Gas) or MIG (Metal Inert Gas) welding. Each type necessitates a distinct set of abilities. Understanding the skills needed for TIG and MIG welding can steer you toward the method better aligned with your abilities or the skills you aim to develop.
Skills Needed For Tig Welding
TIG welding is renowned for its demanding skill set. Patience and a steady hand are paramount.
- Coordination: Synchronize your hand movements with the filler material.
- Concentration: Pay close attention to details for prolonged periods.
- Control: Maintain a consistent arc length.
- Precision: Weld at the right speed and angle.
These skills contribute to the high quality and cleanliness of TIG welds, making them ideal for intricate projects.
Skills Needed For Mig Welding
On the other hand, MIG welding is more forgiving and can be picked up relatively quickly. Skills for successful MIG welding include:
- Basic machine setup: Understand voltage and wire speed settings.
- Steadiness: Move your hand smoothly to create even welds.
- Positioning: Hold the welding gun correctly to ensure proper bead formation.
- Adjustment: Adapt to different metals and thicknesses.
MIG welding offers flexibility and speed, making it a go-to for varied projects and beginners.
Whether you choose TIG or MIG welding, developing the right skills ensures strong, effective welds and the ability to tackle diverse projects with confidence.
Advantages Of Tig Over Mig
The debate between TIG and MIG welding is common among professionals and hobbyists alike. When we talk about precision and finish, TIG welding takes the lead.
Advantages Of Tig Welding
- Greater Control: TIG welding offers superior control over the welding process, which leads to neater, stronger welds.
- Cleaner Process: TIG does not produce splatter or sparks, leaving a clean finish without the need for extra cleanup.
- Versatility: It can weld a wider variety of metals, including thin materials and different alloys.
- Better Aesthetics: Offers high-quality, precise welds that look better.
- No Flux: TIG doesn’t require flux, which means no risk of entrapment in the weld metal.
- Precision: Excellent for intricate or detailed work.
Comparison With Mig Welding
TIG Welding | MIG Welding |
---|---|
Higher precision | Faster production rate |
Cleaner and aesthetically pleasing finishes | More forgiving on dirty or rusty metals |
Requires more skill and practice | Easier for beginners to learn and use |
More control allows for stronger welds | Good for larger and thicker materials |
Advantages Of Mig Over Tig
When choosing between MIG and TIG welding, it’s vital to know their strengths. MIG welding stands out due to its simpler learnability and faster speeds, making it a popular choice in various applications.
Advantages Of Mig Welding
MIG welding, widely known as Gas Metal Arc Welding (GMAW), offers several distinct benefits:
- Faster Production: MIG welding is generally much quicker than TIG welding.
- Easier to Learn: It’s user-friendly and less complex, a benefit for beginners.
- Versatile: Works on a vast range of metals and thicknesses.
- Less Cleanup: Produces fewer weld splatter compared to other methods.
Comparison With Tig Welding
TIG welding offers precision, but MIG prevails in speed and ease. Let’s compare:
MIG Welding | TIG Welding |
---|---|
Great for long welds on thick materials | Best for thin materials and detailed work |
Lower cost of operation | Higher-cost equipment and operation |
Easy to master | Takes time and skill to perfect |
In summary, MIG welding tops TIG in production speed and operational simplicity. It suits a broad array of projects, making it an optimal method for both novices and professionals.
Limitations Of Tig
Tungsten Inert Gas (TIG) welding excels in precision and aesthetics, but it’s not without limits. Understanding these limitations helps welders choose the right process for their project. Below is a detailed look into the constraints encountered with TIG welding.
Limitations Of Tig Welding
- Slower Process: TIG welding takes more time than MIG or other methods, making it less suitable for high-volume production.
- High Skill Level Required: Mastering TIG welding demands significant practice and skill, which can pose a challenge for beginners.
- Equipment Cost: The initial setup for TIG welding is generally pricier due to the need for specialized equipment.
TIG welding also encounters operational restrictions. Find out what these are and how they might affect your project:
Operational Limitation | Impact on Welding |
---|---|
Sensitivity to Contaminants: | Cleanliness is crucial. Any contamination can lead to poor quality welds. |
Material Limitations: | Not all metals can be easily TIG welded. This could limit material options. |
It’s also important to consider the physical demands of TIG welding:
- Physical Effort: TIG welding requires a steady hand and concentration over extended periods.
- Heat Control: Precise heat control is necessary, which can be challenging to maintain throughout the weld.
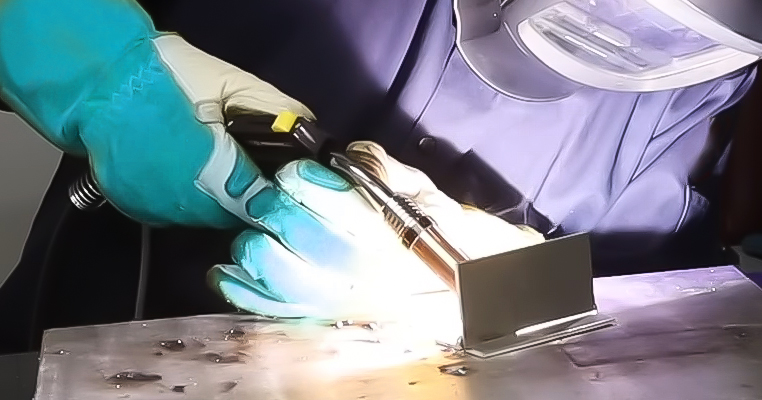
Credit: blog.red-d-arc.com
Limitations Of Mig
Exploring the world of welding reveals various methods, each with its strengths. Metal Inert Gas (MIG) welding is popular for its speed and ease. Still, it comes with limitations that might sway a professional’s choice towards Tungsten Inert Gas (TIG) welding for certain jobs. In the following sections, we’ll delve into the specific limitations of MIG welding.
Limitations Of Mig Welding
MIG welding offers convenience but faces challenges.
- Control and Precision: MIG can struggle with thin metals. TIG provides superior precision.
- Outdoor Use: Wind disrupts MIG’s gas shielding, affecting weld quality. TIG is less sensitive to the wind.
- Aesthetics: MIG welds aren’t as neat. For clean, visually appealing welds, TIG is the winner.
- Materials: MIG is mainly for steel and aluminum. TIG handles more types, like titanium and copper.
- Positional Welding: MIG welds overhead or in tight spaces are tough. TIG welders find it easier to manage.
MIG welding is fast, it lacks the finesse that TIG welding offers. This breakdown showcases where MIG might fall short, emphasizing how TIG can be a stronger option depending on the project’s needs.
Safety Considerations
When talking about welding, safety is as vital as the strength of the weld. Two popular methods, TIG and MIG welding, each come with their specific safety measures. Knowing these can protect you from hazards.
Safety Measures For Tig Welding
- Wear proper gear: Use a helmet with an appropriate shade level.
- Use gloves: Heat-resistant gloves prevent burns.
- Ventilation is key: Ensure the area is well-ventilated to avoid toxic gases.
- Electrical safety: Inspect equipment for defects before starting.
- Avoid water: Keep your work area dry to prevent electric shocks.
Safety Measures For Mig Welding
- Protect skin and eyes: Full coverage clothing and auto-darkening helmets shield from UV rays.
- Breath safely: Use masks or respirators to filter out fumes.
- Manage sparks: Remove flammable materials to prevent fire.
- Check connections: Ensure gas and electrical connections are secure.
- Stay grounded: Always check the work clamp connection.

Credit: www.nexair.com
Environmental Impact
In the welding world, the battle of strength between TIG and MIG is well-known. Yet, the environmental impact each method leaves behind matters just as much. Both TIG and MIG welding processes use different materials and gases. This affects the air we breathe and our planet’s health. Let’s dive into the specific environmental footprints of TIG and MIG welding.
Environmental Impact Of Tig Welding
TIG welding, or Tungsten Inert Gas welding, stands out for its cleaner process. It uses a tungsten electrode that doesn’t consume itself during welding. This results in fewer emissions. Non-consumable electrodes mean less waste material. The most common gas for TIG welding is Argon, which is not toxic.
- Less ozone generation: emits lower levels of ozone.
- No spatter: reduces clean-up waste.
- Minimal fumes: TIG creates fewer fumes than MIG.
Environmental Impact Of Mig Welding
MIG welding, or Metal Inert Gas welding, is known for its speed and efficiency. But, it can have a larger environmental impact. Consumable wire electrodes are used, producing more waste. MIG often uses a mixture of Argon and Carbon Dioxide. Carbon Dioxide emissions contribute to greenhouse gasses.
- Higher ozone levels: MIG tends to produce more ozone.
- Waste from spatter: leads to excess material waste.
- Increased fumes: associated with the metal wire used.
Choosing between TIG and MIG welding will depend on your project. But keep in mind the environmental impacts too. Smart choices help protect our planet.
Future Trends
As the world of welding evolves, both TIG and MIG welding face exciting changes. These innovations promise to enhance welding capabilities and broaden the applications of each technique. Let’s explore the technological advancements steering these forms of welding into the future.
Technological Advancements In Tig Welding
TIG welding stands at the threshold of revolution. New power sources equipped with intelligent controls will define its future. They promise efficiency and higher quality welds. These advancements tackle historical challenges in TIG welding, such as slow welding speeds and the high skill level required.
- Automatic control systems to regulate arc stability and reduce operator error.
- Advanced pulse welding technology improves weld consistency and appearance.
- Precise heat input controls minimize material deformation and stress.
Technological Advancements In Mig Welding
MIG welding technology rapidly evolves to meet the needs of modern manufacturing. Innovations focus on increasing productivity, ease of use, and weld quality. As a result, MIG welding is becoming more versatile and accessible.
- Wire feed systems that adjust to the welder’s technique for efficient operation.
- Synergic welding machines that simplify setting adjustments while offering superior control.
- New materials in wires and gases provide enhanced weld properties.
Both TIG and MIG welding benefit from these advancements. These improvements lead to stronger and more reliable welds in various industries. As technology develops, both techniques will have their strengths. The choice between them depends on job requirements and welder preference.
The future of welding looks bright as these two methods continue to evolve side by side. The ultimate goal is to deliver top-notch results across all welding applications.
Recommendations
Welcome to the comprehensive guide on whether TIG is stronger than MIG welding. Making the right choice between these two types can be a game-changer for your projects. Here are expert recommendations when it comes to choosing between TIG and MIG welding.
Recommendations For Choosing Tig Welding
Consider TIG welding for projects that require:
- Precision and finesse in areas such as aerospace or sculpture.
- Control over heat, which is crucial for thin materials to prevent warping.
- Clean and high-quality finishes without the need for sanding or grinding.
- Working with a variety of metals, including aluminum, stainless steel, and more.
Select TIG when appearance matters and you can sacrifice on speed for quality.
Recommendations For Choosing Mig Welding
Opt for MIG welding when your project involves:
- Thicker materials that can handle higher heat input.
- Speed as a priority, especially in production environments.
- Projects that require long, continuous welds without interruptions.
- Less complex welding positions, ideal for learners and new welders.
MIG is best when efficiency and straightforward operations are key.
References
Understanding the strength of welding processes is crucial for anyone involved in metal fabrication. This section will provide reliable references, allowing an insightful comparison between TIG (Tungsten Inert Gas) welding and MIG (Metal Inert Gas) welding.
Citations And Sources
The data and insights discussed stem from authoritative texts and studies.
- Welding Handbook: A comprehensive guide by the American Welding Society.
- Metallurgical Analysis: Journals and papers provide depth on metal characteristics.
- Industrial Standards: ASTM and ISO norms give us benchmarks for strength.
These materials form a solid foundation for comparing TIG and MIG welding’s effectiveness. Knowing the strength of each technique helps ensure the right application in any scenario.
Further Reading
Delving into the world of welding, one might wonder is TIG stronger than MIG? The answer isn’t simple and requires further exploration to fully grasp the nuances of each welding process. This section aims to provide additional insight through carefully selected resources.
!– Additional Resources For In-depth Understanding —
For readers eager to learn more about TIG vs MIG welding, a range of resources is available.
- Books: Welding Essentials – A guide that covers different welding processes.
- Videos: Online tutorials provide step-by-step welding techniques.
- Articles: Industry publications offer technical comparisons.
Use these materials to build a strong foundation in welding knowledge. Tables comparing TIG and MIG strengths are particularly useful. They break down complex information into easy-to-digest facts.
!– Tig Vs. Mig Strengths Comparison Table —
TIG Welding | MIG Welding |
---|---|
High precision | Quicker process |
Stronger welds for thin materials | Higher deposition rates |
This table summarizes key factors that may influence whether TIG or MIG is the stronger option based on certain criteria.
!– Exploration Through Online Forums And Groups —
Join online forums and groups that focus on welding. You’ll find firsthand experiences and expert insights.
- Reddit: Subreddits like r/Welding contain user discussions and advice.
- Facebook Groups: Connect with professionals and enthusiasts.
- LinkedIn: Follow industry leaders who share their expertise.
These platforms often feature question-and-answer sessions that can clarify your doubts.
Frequently Asked Questions For Is Tig Stronger Than Mig
What Is The Strength Difference Between Tig And Mig?
TIG welding often provides higher quality, stronger welds than MIG welding due to the control over the weld that it offers. The precision and cleanliness that TIG lends to the welding process make it ideal for delicate or critical weld joints.
Can Tig Welding Be As Fast As Mig?
TIG welding is typically slower than MIG welding because it requires more precision and control, which takes additional time. MIG is preferred for projects needing higher production speeds without the need for intricate welds.
What Materials Can Tig And Mig Both Weld?
Both TIG and MIG welding processes can weld a variety of materials including steel, stainless steel, and aluminum. However, TIG is preferred for thinner gauge and highly aesthetic materials, while MIG is efficient for thicker materials.
Is Tig Welding More Versatile Than Mig?
TIG welding is more versatile when it comes to different types of metals. It can handle a wider range of material types and thicknesses, including both ferrous and non-ferrous metals.
Conclusion
As we’ve explored, both TIG and MIG welding have their merits. Your project’s demands dictate the optimal choice. TIG offers precision and strength for delicate tasks, while MIG excels at efficiency and ease for larger-scale work. Embrace the right technique for superior construction and enduring results.
Remember, skill enhances the method’s potency.