Welding rod numbers indicate the type of welding rod being used and its specific characteristics, such as the type of coating and current to be used. Understanding these numbers is crucial for achieving a successful weld and ensuring safety.
Welding rods are labeled with specific numbers that indicate their composition and intended use. It’s essential to be familiar with these numbers to select the right rod for a particular welding task. By considering the welding rod numbers, welders can ensure that they are using the appropriate rod for the specific type of metal and welding technique they are working with.
This knowledge contributes to producing high-quality welds and maintaining a safe and efficient welding process. Understanding welding rod numbers is a fundamental aspect of the welding profession, and it is essential for welders to grasp their significance to achieve successful welds.
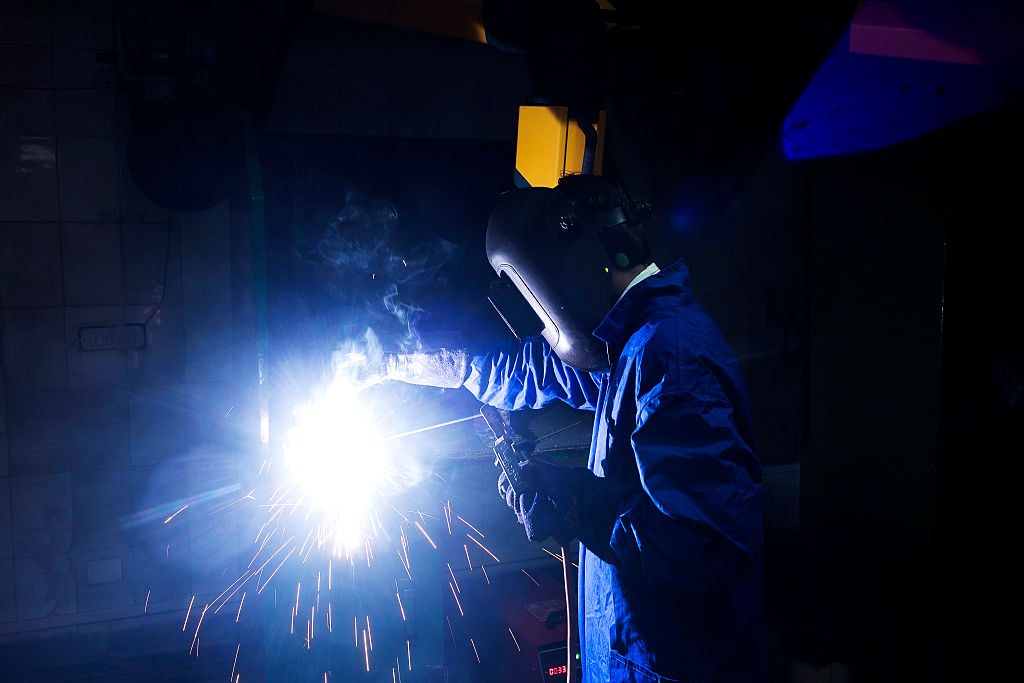
Credit: www.bloomberg.com
Types Of Welding Rods
When it comes to welding, it’s essential to choose the right type of welding rod for the job. Welding rods play a crucial role in the welding process as they determine the strength, durability, and quality of the weld. Understanding the different types of welding rods available can help you make an informed decision that ensures effective and reliable welds.
Overview Of Different Types
Welding rods come in various types to suit different welding applications. The most common types of welding rods include:
- Shielded metal arc welding (SMAW) rods
- Gas metal arc welding (GMAW) rods
- Flux-cored arc welding (FCAW) rods
- Gas tungsten arc welding (GTAW) rods
- Submerged arc welding (SAW) rods
Each type of welding rod is designed for specific welding techniques and materials, ensuring optimal performance and weld integrity. Understanding the composition and characteristics of these welding rods is crucial in determining their suitability for particular welding tasks.
Composition And Characteristics
Understanding the composition and characteristics of welding rods is essential when choosing the right rod for your welding needs:
Type | Composition | Characteristics |
---|---|---|
SMAW rods | Coated in flux, comprised of iron, graphite, and alloys | Easy to use, versatile, suitable for various materials |
GMAW rods | Solid wire or flux-cored wire, containing gas for shielding | High productivity, excellent for thin materials |
FCAW rods | Flux-cored wire, containing flux for shielding | High deposition rates, excellent for outdoor applications |
GTAW rods | Tungsten electrode, non-consumable, with a filler wire | Precise control, high-quality welds, suitable for exotic metals |
SAW rods | Flux and consumable wire, submerged beneath a granular flux | High-deposition rates, ideal for thick materials and long welds |
By understanding the composition and characteristics of different welding rods, you can choose the appropriate rod that meets the requirements of your specific welding application. The right choice will result in strong, durable welds that withstand the test of time.
Welding Rod Numbering System
When it comes to understanding welding rods, it’s essential to decipher the numbering system. The welding rod numbering system provides critical information about the characteristics and properties of the rod. Understanding these numbers is crucial for choosing the right welding rod for a specific welding task. In this article, we’ll delve into the welding rod numbering system, breaking down the basic structure and meaning of the digits.
Basic Structure Of Welding Rod Numbers
The welding rod numbering system consists of four or five digits that convey important details about the welding rod. Each digit represents a specific characteristic of the welding rod, including the type of coating, welding position, and tensile strength. These numbers are standardized across the industry, allowing welders to easily interpret the information provided by the manufacturer.
Meaning Of The Digits
The first two digits of the welding rod number indicate the minimum tensile strength of the electrode, measured in thousands of pounds per square inch (psi). The third digit represents the welding position(s) in which the rod can be used, such as flat, horizontal, vertical, or overhead. The fourth digit, if present, signifies special characteristics such as the type of coating and the welding current the rod requires.
Understanding The Impact Of Rod Numbers
Understanding the impact of rod numbers in welding is crucial for achieving desired results. The unique characteristics of each rod number determine its suitability for specific welding tasks, such as strength, penetration, and deposition. By comprehending rod numbers, welders can make informed choices for successful welding projects.
Understanding the Impact of Rod Numbers Welding rod numbers play a crucial role in determining the success of a welding project. The number assigned to a welding rod provides vital information about its composition and properties, allowing welders to make informed decisions about which rod to use for specific applications. With a clear understanding of these numbers, welders can optimize their welding techniques and achieve superior results.
Effect On Welding Techniques
The rod number directly influences the welding technique required to produce a strong and reliable weld. Lower-numbered rods, such as E6010, are designed for deep penetration and can be used with an all-position technique. In contrast, higher-numbered rods, like E7018, require a slower and steady technique to ensure proper deposition and strength. Understanding these nuances allows welders to adapt their technique accordingly, resulting in high-quality welds.
Choosing The Right Rod For The Job
When selecting a welding rod, it’s essential to consider the specific requirements of the job. Factors such as material thickness, welding position, and desired weld characteristics all play a role in determining the most suitable rod number. By matching the rod number to the job requirements, welders can ensure optimal performance and minimize the risk of defects or failures in the weld. Overall, a clear understanding of welding rod numbers empowers welders to make informed decisions and optimize their welding techniques for superior results. By carefully considering the impact of rod numbers and choosing the right rod for the job, welders can achieve reliable and durable welds in a wide range of applications.
Industry Standards And Codes
When it comes to welding, industry standards and codes play a crucial role in ensuring safety, quality, and efficiency. Understanding these standards is essential for welders, as it helps them select the right welding rods for different applications. In this blog post, we will explore the industry standards and codes related to welding rod numbers.
American Welding Society (aws) Standards
The American Welding Society (AWS) is a renowned organization that sets the standards for welding processes and materials in the United States. When it comes to welding rods, AWS assigns a unique numbering system to categorize them based on their characteristics and usage. These numbers are commonly known as AWS electrode classifications.
Each AWS electrode classification consists of a letter prefix followed by a series of numbers. The letter prefix provides information about the type of welding rod, such as the welding process and the specific characteristics it possesses. The series of numbers indicate the rod’s performance characteristics, such as its tensile strength, position of use, and type of coating.
For example, an AWS electrode classification might look like E7018. Here, the “E” indicates that it is an electrode, and the “70” signifies its minimum tensile strength in thousands of pounds per square inch (ksi). The “18” denotes a low-hydrogen coating, suitable for welding in all positions.
European Standards (en)
Similarly, European countries follow their own set of standards known as the European Standards (EN). These standards ensure compatibility, safety, and quality across the European welding industry. The EN classification system for welding rods is similar to the AWS system, but it uses a different coding scheme.
The EN classification for welding rods consists of a letter prefix followed by a numeric code. The letter prefix provides information about the welding process, while the numeric code represents the mechanical and chemical properties of the rod, including its tensile strength, impact toughness, and composition.
For instance, an EN classification might be C-Mn3Si1. Here, the “C” denotes the welding process (in this case, it stands for manual metal arc welding), the “Mn3Si1” indicates the chemical composition of the rod, consisting of 3% manganese and 1% silicon.
In addition to the AWS and EN standards, other countries and regions have their own set of welding rod classification systems. It is important for welders to familiarize themselves with these standards and codes to ensure they comply with the requirements of their specific locale.
Selecting The Correct Welding Rod
Select the correct welding rod by understanding the numbers associated with different rods. Each number indicates specific properties, such as the rod’s tensile strength, welding position, and coating type. Knowing these numbers helps you choose the right rod for your welding project.
Factors To Consider
When it comes to selecting the correct welding rod for your specific application, there are several important factors to consider. By understanding and evaluating these factors, you can ensure that you choose the right welding rod for the job. Firstly, you need to consider the type of material you will be welding. Different welding rods are designed for specific materials such as steel, aluminum, stainless steel, or cast iron. It is crucial to use a rod that is compatible with the material you are working with to achieve the best weld quality. Secondly, you should take into account the thickness of the material you are welding. Thicker materials require welding rods with higher amperage capacities to create strong and durable welds. On the other hand, thinner materials may require rods with lower amperage capacities to prevent burn-through. Another factor to consider is the welding position. Whether you are welding in the flat, horizontal, vertical, or overhead position, the welding rod you select should be suitable for that specific position. Some rods are designed to perform better in certain positions, providing better control, penetration, and overall weld quality. Next, it is important to assess the intended application of the weld. Different welding rods have varying levels of tensile strength, flexibility, and resistance to corrosion. If the weld will be subjected to heavy loads, vibrations, or exposure to harsh environments, you may need a rod with higher tensile strength and better corrosion resistance. Additionally, you should consider the welding process you will be using. Different welding processes such as stick welding, MIG welding, and TIG welding require specific types of welding rods. Each process has its own advantages and limitations, so choosing the right welding rod for your chosen process is key to achieving optimal results.
Rod Selection For Specific Applications
In addition to the factors mentioned above, specific applications may require the use of specialized welding rods. Let’s explore some common scenarios where rod selection is crucial: 1. Automotive welding: When working on automotive projects, it is important to choose welding rods that offer good penetration and create strong, durable welds. Selecting rods specifically designed for automotive applications ensures the welds can withstand the stresses of the road. 2. Structural welding: For structural welding projects, such as the construction of buildings or bridges, high-strength welding rods are required. These rods provide excellent weld integrity and meet the structural standards required for such applications. 3. Pipe welding: Welding pipes involves unique challenges due to their circular shape. Selecting welding rods suitable for pipe welding ensures proper fusion, strong welds, and leak-free connections. 4. High-temperature applications: When welding materials that will be subjected to high temperatures, such as furnace components or exhaust systems, it is crucial to use welding rods that can withstand these extreme conditions. These rods are formulated with materials that have high melting points and offer excellent heat resistance. In conclusion, selecting the correct welding rod is vital to achieve strong, durable welds that meet the specific requirements of your application. By considering factors such as the material, thickness, position, intended application, welding process, and specific application requirements, you can confidently choose the right welding rod for your needs and ensure successful welding projects.
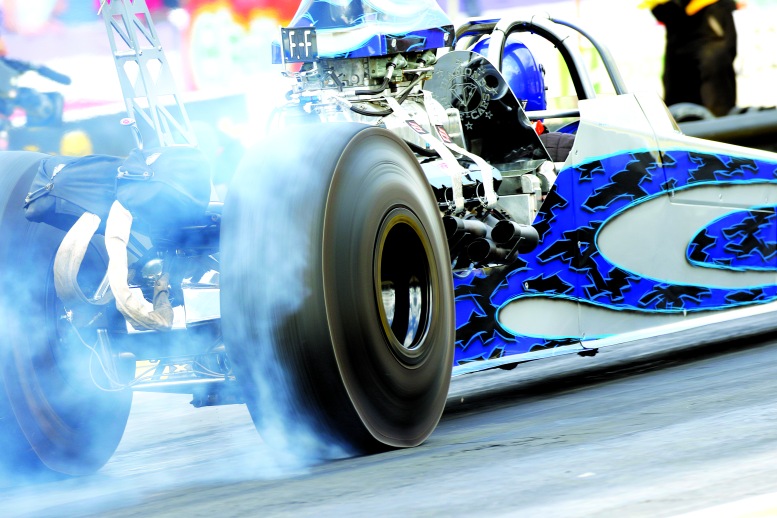
Credit: www.nhra.com
Welding Rod Storage And Handling
Proper storage and handling of welding rods are essential to ensure the quality of your welding projects. Improper storage can lead to moisture absorption and contamination, while mishandling can result in damage or reduced usability of the rods. In this section, we will explore the best practices for welding rod storage and handling.
Proper Storage Conditions
For optimal performance and longevity, it is crucial to store welding rods in suitable conditions. Below are the key factors to consider:
- Temperature: Store welding rods in a cool and dry environment, preferably with a temperature range of 70°F to 120°F (21°C to 49°C). Extreme heat or cold can affect the rods’ performance.
- Humidity: Moisture absorption can cause welding rod defects. Keep them in a low humidity area below 70% to prevent rusting and other potential damage. Consider using a dehumidifier if needed.
- Protection from contaminants: Shield welding rods from substances like oil, dirt, dust, and chemical vapors that can contaminate and compromise their integrity. Store them in airtight containers or use rod ovens specifically designed for storage.
Handling Best Practices
Proper handling techniques contribute significantly to the overall quality and usability of your welding rods. Here are some guidelines to follow:
- Avoid dropping: Dropping welding rods can lead to structural damage, causing weak spots, cracks, or fractures. Be careful while transporting them and handle with care.
- Minimize exposure: Limit the time exposure of welding rods to the open air to prevent moisture absorption. Take out only the necessary amount of rods at a time and promptly seal the container afterwards.
- Control moisture contact: Keep your hands and work areas dry while handling the rods. Moisture from sweat or wet gloves can transfer to the rods and potentially impact their performance.
- Clean electrodes: Before starting your welding process, ensure that the welding electrodes are clean and free from rust, oil, or other contaminants. Remove any debris by gently grinding or brushing the electrode surface.
By following these proper storage conditions and handling best practices, you can extend the shelf life of your welding rods, maintain their quality, and achieve optimal welding results.
Welding Rod Number Misconceptions
Understanding welding rod numbers can help dispel common misconceptions. Properly decoding the numbers allows welders to determine the rod’s composition, diameter, and intended use for a more effective welding process.
When it comes to understanding welding rods, there are many misconceptions that can lead to confusion and mistakes. A common source of confusion is the numbering system used to categorize welding rods. In this section, we will debunk some of the most common welding rod number misconceptions and help you gain a clearer understanding of how these numbers work.
Common Misunderstandings
There are a few common misunderstandings when it comes to welding rod numbers. These misconceptions can hinder your ability to choose the right rod for your welding project:
- Lower numbers mean smaller rods: One of the most prevalent misconceptions is that lower numbers indicate smaller welding rods. However, this is not entirely accurate. The numbering system for welding rods is not based on size, but on the rod’s tensile strength, welding position, and other characteristics.
- Rods with higher numbers are always better: Another misconception is that higher-numbered welding rods are always better than lower-numbered ones. While higher numbers may indicate stronger or more versatile rods, it all depends on your specific welding needs and the project at hand. It’s important to consider the specific properties of the rod rather than solely relying on the number.
Clarifying Rod Number Myths
To clarify some of these misconceptions, let’s take a closer look at how welding rod numbers are determined:
First and foremost, the numbering system for welding rods originated from the American Welding Society (AWS), and it is an industry-standard.
The AWS classification system uses a combination of letters and numbers to indicate various characteristics of the rod. The first two digits of the code represent the minimum tensile strength, measured in thousands of pounds per square inch.
For example, a welding rod with the number “6010” means that it has a minimum tensile strength of 60,000 PSI.
The third and fourth digits indicate the welding position and type of coating on the rod. This information helps determine the rod’s suitability for specific welding applications.
It’s important to note that the AWS numbering system is not the only one used worldwide. Each country or region may have its own classification system, so be cautious when comparing rods with different code systems.
In conclusion, understanding welding rod numbers can help you make more informed decisions when selecting the right rod for your welding projects. By debunking these common misconceptions, you can confidently choose the best welding rod based on its specific properties and suitability for your needs.
Impact Of Rod Numbers On Weld Quality
Rod numbers play a crucial role in determining the quality of a weld. Understanding the significance of different rod numbers is essential for achieving optimal results in welding projects.
Impact of Rod Numbers on Weld Quality The selection of welding rod numbers has a significant impact on the overall quality of a weld. Understanding the correlation between the numbers and weld quality is crucial for achieving desired results. Different rod numbers have varying characteristics, influencing factors such as weld strength, appearance, and the presence of defects. Quality Control Considerations When choosing welding rods, quality control is a crucial consideration. Opt for rods with the appropriate number, matching the specific requirements of the welding task at hand. Pay close attention to the manufacturer’s specifications and recommendations for each rod number. Perform thorough inspections to ensure that the welding rods meet the necessary quality standards before use. Welding Defects and Rod Numbers The choice of welding rod number directly impacts the occurrence of welding defects. Mismatched rod numbers can lead to defects such as porosity, cracks, and lack of fusion. Use the correct rod number for the base material to minimize the risk of defects. Conduct regular assessments to identify any welding defects and to determine whether the rod number is contributing to these issues. In summary, the selection of welding rod numbers significantly influences weld quality. Quality control considerations are essential to ensure the suitability of the chosen rods, while choosing the appropriate rod number can minimize the occurrence of welding defects.
Environmental And Safety Regulations
Environmental and Safety Regulations are crucial aspects of the welding industry, ensuring that welding processes adhere to strict standards for the protection of workers, the environment, and the general public. Regulatory compliance and safety precautions play an essential role in the welding rod numbers used in various welding applications.
Regulatory Compliance
Regulatory compliance in welding operations involves adhering to the standards and guidelines set by organizations such as the Occupational Safety and Health Administration (OSHA), the American Welding Society (AWS), and the Environmental Protection Agency (EPA).
Safety Precautions
When working with welding rods, safety precautions are imperative to prevent accidents and protect against health hazards. This includes ensuring proper ventilation in the work area, wearing appropriate personal protective equipment (PPE), and following safe handling and storage protocols for welding rods.

Credit: www.millerwelds.com
Emerging Trends In Welding Rod Technology
As technology continues to advance in various industries, welding is no exception. In recent years, there have been groundbreaking developments in welding rod technology. These emerging trends have revolutionized the welding process, offering improved performance, durability, and efficiency. Let’s take a closer look at the advancements in rod materials and technological innovations that are shaping the future of welding.
Advancements In Rod Materials
Traditionally, welding rods were primarily made from carbon steel or stainless steel. However, with advancements in metallurgy, new materials have emerged that offer enhanced properties and capabilities for welders. One such material is aluminum, which is now commonly used for welding rods due to its lightweight nature and excellent conductivity. Additionally, titanium rods have gained popularity for their high strength-to-weight ratio and corrosion resistance, making them suitable for critical applications.
In recent years, the development of composite welding rods has gained momentum. These rods are composed of a combination of materials, such as ceramic matrix composites or carbon fiber reinforced polymers, which provide superior strength and heat resistance. The use of composite rods allows for increased precision and reduced distortion during the welding process.
Technological Innovations
The welding industry has embraced technological advancements, resulting in innovative solutions that enhance the overall efficiency and quality of welds. One significant technological innovation is the introduction of flux-cored welding rods. These rods are filled with flux materials that shield the weld pool from contaminants, resulting in stronger and cleaner welds. Flux-cored rods have become popular due to their ease of use and versatility in various welding applications.
Another notable technological innovation is the development of self-shielding welding rods. These rods eliminate the need for an external shielding gas, making them more convenient and cost-effective for certain welding projects. Self-shielding rods are commonly used in outdoor or windy environments where gas shielding can be challenging.
The use of nanotechnology has also made waves in the welding industry. Nanotechnology-enabled welding rods offer improved weld strength, reduced defects, and enhanced corrosion resistance. The incorporation of nanomaterials into welding rods has opened up new possibilities for welding processes, including micro-welding and precision joining of advanced materials.
As the demand for sustainable practices grows, there has been a surge in the development of eco-friendly welding rods. These rods are typically made from recycled or low-emission materials, reducing the environmental impact of welding operations. Eco-friendly welding rods not only contribute to a greener planet but also provide comparable performance to conventional rods.
To keep up with the ever-evolving welding industry, it is crucial for welders and manufacturers to stay informed about these emerging trends in welding rod technology. Embracing these advancements can lead to improved productivity, cost savings, and high-quality welds. As the landscape of welding continues to evolve, it is exciting to see what the future holds for welding rod technology.
Training And Education
When it comes to welding, it is crucial for welders to have a solid understanding of rod numbers. Choosing the right welding rod number can greatly impact the quality and success of a weld. That is why training and education play a vital role in ensuring welders are equipped with the knowledge they need to make informed decisions.
Educating Welders On Rod Numbers
Welding, like any skilled trade, requires continuous learning and development. Before getting their hands on a welding torch, welders need to understand the significance of rod numbers and how they affect their welding projects. Educating welders on rod numbers is the first step towards ensuring they use the appropriate welding rod for each job.
Training Programs
Training programs are designed to equip welders with comprehensive knowledge and practical skills in their trade. Welding programs not only cover the basics of welding techniques but also delve into the importance of rod numbers and how to choose the right rod for specific welding applications.
These training programs use a combination of theory and hands-on practice to give welders a well-rounded understanding of welding rod numbers. They teach them how to interpret the numerical codes associated with various rods and what each code represents. By providing welders with this valuable knowledge, training programs empower them to make informed decisions when it comes to selecting welding rods.
Moreover, these programs also highlight the significance of factors such as metal type, joint design, and welding process in determining the appropriate rod number. Welders learn to consider all these variables and factors when choosing a rod, ensuring they achieve strong and structurally sound welds.
Training programs for welders make use of visual aids, practical demonstrations, and interactive sessions to create an engaging learning environment. This hands-on approach allows welders to gain valuable experience in rod selection and understand the impact it has on weld quality.
In addition, these programs also provide welders with the opportunity to practice their skills using different rod numbers on a variety of materials. By doing so, they gain confidence in their ability to choose the right welding rod for any given welding task.
By prioritizing training and education on rod numbers, welders are equipped with the knowledge and skills necessary to excel in their craft. They are empowered to make informed decisions when it comes to selecting welding rods, resulting in superior weld quality and ultimately, the success of their welding projects.
Case Studies And Examples
Understanding welding rod numbers is crucial for choosing the right rod for your welding projects. In this section, we will delve into some real-world case studies and success stories that demonstrate the importance of selecting the appropriate welding rod number.
Real-world Applications
Welding rod numbers may seem like a complex system, but once you grasp the basics, you’ll be able to apply them to various welding scenarios. Let’s take a look at a few real-world applications to see how welding rod numbers come into play:
- Structural Welding: When constructing buildings or bridges, it is essential to use an appropriate welding rod. For instance, in a project that requires welding high-strength steel, a rod with a higher tensile strength and welding current should be used. Using the wrong rod can compromise the structural integrity of the entire project.
- Automotive Welding: In the automotive industry, precise and strong welds are essential. Different welding rod numbers are used depending on the type of metal being joined. For example, when welding aluminum, a rod with a high silicon content is typically used to achieve a smooth and strong weld.
- Pipe Welding: Welding pipes is a specialized task that requires specific welding rod numbers to ensure proper joint integrity. For instance, when welding stainless steel pipes, a rod with the appropriate stainless steel electrode classification and diameter must be chosen.
Success Stories
The right choice of welding rod number can make all the difference between a successful welding project and one that falls short. Here are a couple of success stories that highlight the impact of using the right welding rod:
- Case Study 1: XYZ Manufacturing
XYZ Manufacturing faced a challenging project that required welding dissimilar metals. They initially used a welding rod that was not suitable for the task, resulting in weak and brittle welds. After consulting with welding experts, they switched to a rod with a suitable number, which drastically improved the quality and strength of their welds.
- Case Study 2: ABC Construction
ABC Construction had a project that involved welding high-strength steel beams. Initially, they used a rod with a lower tensile strength, leading to frequent weld failures. By switching to a welding rod with a higher tensile strength, they successfully completed the project with flawless and robust welds.
These success stories demonstrate the significance of understanding welding rod numbers and choosing the right rod for each specific application. By carefully considering the welding rod number, you can achieve superior weld quality, structural integrity, and overall project success.
Future Outlook For Welding Rod Numbers
As technology continues to advance, the future outlook for welding rod numbers appears promising. With ongoing developments and innovations, the welding industry is expected to witness significant changes in the coming years. Here, we explore some of the anticipated developments and potential challenges that lie ahead.
Anticipated Developments
The welding industry is projected to experience several exciting advancements in the near future:
- The introduction of new welding rod numbers:
- In response to evolving welding techniques and requirements, new welding rod numbers are likely to be introduced. These numbers will be specifically designed to cater to emerging welding technologies, optimizing the welding process and enhancing productivity.
- The industry can anticipate the creation of welding rod numbers that offer improved weld penetration, reduced spatter, and enhanced arc stability.
- Advancements in rod materials:
- The development of new materials with superior strength, durability, and corrosion resistance will revolutionize the welding rod market.
- Manufacturers are expected to create welding rods that are capable of joining dissimilar metals without compromising the integrity of the joint.
- Automation and robotics:
- With the rise of automation and robotics, welding processes are becoming more precise, efficient, and streamlined.
- In the future, welding rod numbers will cater to automated and robotic welding applications, ensuring optimal performance and compatibility.
- Robotic welding systems will be able to interpret welding rod numbers, select the appropriate rod for the job, and execute high-quality welds with minimal human intervention.
Potential Challenges
While the future of welding rod numbers looks promising, there are some challenges to consider:
- Standardization:
- As new welding rod numbers are introduced, ensuring global standardization and widespread adoption may pose a challenge.
- The industry will need to establish protocols and guidelines to maintain consistency and facilitate seamless integration of new welding rod numbers across various welding operations.
- Training and education:
- With the introduction of advanced welding rod numbers, there will be a need for comprehensive training and education to equip welders with the necessary skills and knowledge.
- Training programs and certifications will play a crucial role in preparing welders to effectively utilize the new welding rod numbers and maximize their benefits.
- Cost implications:
- The adoption of new welding rod numbers may come with initial costs associated with equipment upgrades and training.
- Welding professionals and businesses will need to consider the financial implications of transitioning to the latest welding rod numbers and weigh them against the potential long-term advantages.
The future of welding rod numbers is undoubtedly exciting, with anticipated developments and potential challenges. By staying abreast of these trends and addressing the associated hurdles, the welding industry can embrace the advancements and leverage new welding rod numbers to achieve remarkable results.
Frequently Asked Questions On Welding Rod Numbers Explained
What Do The Numbers Mean On A Welding Rod?
The numbers on a welding rod indicate its classification, which includes information about its strength, welding position, and electrode coating. These numbers help welders choose the right rod for their specific welding needs.
What Do The Numbers 7018 Mean On A Welding Rod?
The numbers 7018 on a welding rod refer to its classification. These numbers indicate that the rod is an all-position, low-hydrogen electrode commonly used for welding mild and low alloy steels.
What Does The 3 Mean In 6013?
The ‘3’ in 6013 refers to the chemical composition of the electrode.
What Does The E 7018 Stand For?
E 7018 is a welding electrode code that signifies the electrode’s characteristics, such as its tensile strength and welding positions.
What Do Welding Rod Numbers Mean?
Welding rod numbers indicate the type, composition, and strength of the electrode used for welding.
Conclusion
Understanding welding rod numbers is key to selecting the right rod for your welding project. By deciphering the meaning behind these numbers, you can ensure optimal performance and results. Remember that the first two digits denote tensile strength, while the third digit indicates the welding position and polarity.
Additionally, the final digit signifies the coating type. Taking these factors into account will allow you to make informed choices and achieve successful welds. So, next time you’re faced with welding rod numbers, you’ll be equipped to make the best decision for your specific needs.
Happy welding!