7014 and 7018 welding rods are both popular choices for welding mild steel. 7014 is known for its easy flow and good penetration, making it suitable for thin metal and small weld areas.
On the other hand, 7018 is known for its low hydrogen content, making it ideal for welding high-strength steel and heavy sections. One key difference is that 7018 requires more skill to use effectively compared to 7014. Understanding the characteristics of these welding rods is crucial for achieving the desired weld strength and quality.
We will explore the differences between 7014 and 7018 welding rods to help you make an informed decision for your welding projects.
Chemical Composition
The chemical composition of welding rods plays a crucial role in determining their performance and suitability for specific applications. Understanding the composition of welding rods can help welders make informed decisions and achieve optimal results in their welding projects. In this section, we will explore the chemical composition of two popular welding rods – 7014 and 7018.
7014 Welding Rod Composition
The 7014 welding rod is a versatile electrode that is commonly used for general-purpose welding. It is known for its excellent arc stability and smooth weld bead appearance.
The chemical composition of the 7014 welding rod mainly consists of the following components:
Component | Percentage |
---|---|
Iron (Fe) | Balance |
Carbon (C) | 0.08% max |
Manganese (Mn) | 0.60-1.00% |
Silicon (Si) | 0.30-0.60% |
Sulfur (S) | 0.035% max |
Phosphorus (P) | 0.040% max |
This composition ensures that the 7014 welding rod offers good mechanical properties, such as high tensile strength and impact resistance. It also provides excellent weldability with minimal spatter.
7018 Welding Rod Composition
The 7018 welding rod is widely regarded as one of the most versatile and commonly used electrodes, especially for structural welds. It is known for its high tensile strength and superior crack resistance.
The chemical composition of the 7018 welding rod mainly includes the following elements:
Component | Percentage |
---|---|
Iron (Fe) | Balance |
Carbon (C) | 0.08% max |
Manganese (Mn) | 1.60-2.10% |
Silicon (Si) | 0.75-1.25% |
Sulfur (S) | 0.035% max |
Phosphorus (P) | 0.040% max |
The composition of the 7018 welding rod ensures excellent weld quality with minimal porosity and enhances the electrode’s ability to withstand higher welding currents. This makes it suitable for a wide range of applications, including construction, shipbuilding, and pipeline welding.
Welding Characteristics
Welding Positions For 7014 Rod
The 7014 welding rod is designed for flat, horizontal, vertical, and overhead welding positions. It offers versatility and ease of use, making it suitable for various welding applications. The 7014 rod is known for producing smooth and clean welds, making it ideal for beginners and general-purpose welding tasks.
Welding Positions For 7018 Rod
7018 welding rods are primarily used for flat and horizontal welding positions. While it is not as versatile as the 7014 rod, it is preferred for structural welding projects due to its high strength and quality of welds. The 7018 rod is commonly used in industries such as construction and infrastructure development for its reliable performance and weld quality.
“` In the comparison of 7014 welding rod vs. 7018, understanding the welding characteristics is essential. The 7014 welding rod offers versatility across various positions, whereas the 7018 welding rod excels in specific positions, catering to high-strength applications. Each rod’s welding positions play a crucial role in determining its suitability for different welding projects.
Features And Applications
When it comes to welding rods, choosing the right one for your project is essential. Two popular options for welding rods are the 7014 and 7018, each with its own set of features and applications.
Features Of 7014 Rod
- Iron powder coating for a smooth and stable arc
- Easy to use with all types of welding machines
- High metal deposition rate for quick welding
- Compatible with both AC and DC polarity
Applications Of 7014 Rod
The 7014 welding rod is ideal for general-purpose welding, including structural work, machine bases, fabrication, and repairs.
Features Of 7018 Rod
- Low hydrogen content for improved weld quality
- Excellent bead appearance with minimal spatter
- High tensile strength for durable welds
- Suitable for vertical and overhead welding positions
Applications Of 7018 Rod
The 7018 welding rod is commonly used for heavy-duty welding tasks, such as construction, pressure vessels, pipelines, and structural steel.
Shielding Gas Requirements
When it comes to welding, understanding the shielding gas requirements is essential for achieving quality welds. Shielding gas plays a crucial role in protecting the molten weld pool from atmospheric contamination, such as oxygen and nitrogen, which can lead to weakened welds and defects. Different types of welding rods have specific requirements when it comes to shielding gas, and in this section, we will explore the shielding gas requirements for 7014 and 7018 welding rods.
7014 Rod Shielding Gas
The 7014 welding rod is often referred to as an iron powder electrode. It is commonly used for general-purpose welding applications and is known for its ease of use and versatility. One of the benefits of using the 7014 rod is that it can be used with both AC (alternating current) and DC (direct current) power sources.
When it comes to shielding gas requirements, the 7014 welding rod does not typically require the use of additional shielding gas. It is designed to produce a self-shielding slag that acts as a protective barrier during the welding process. This self-shielding slag helps to maintain the integrity of the weld and prevents the contamination of the weld pool by atmospheric gases.
7018 Rod Shielding Gas
The 7018 welding rod is a low-hydrogen electrode that is commonly used for structural welding applications. It is known for its high strength and high-quality welds. Unlike the 7014 rod, the 7018 rod requires the use of external shielding gas for optimal results.
When using the 7018 rods, the most commonly used shielding gas is 100% carbon dioxide (CO2), or a mixture of carbon dioxide and argon. This shielding gas helps to prevent the exposure of the molten weld pool to oxygen and moisture, which can result in hydrogen-induced cracking.
The specific ratio of carbon dioxide to argon in the shielding gas mixture will depend on the specific welding application and the desired weld characteristics. It is important to consult the manufacturer’s recommendations or consult with a welding expert to determine the appropriate shielding gas mixture for your specific application when using the 7018 rods.
Welding Techniques
Welding is a highly skilled trade that requires a deep understanding of various welding techniques and the corresponding welding rods that are used for each specific task. When it comes to 7014 welding rods vs 7018 welding rods, knowing the proper techniques can make all the difference in achieving a clean, strong, and durable weld. In this article, we will discuss the techniques for using both the 7014 and 7018 welding rods, ensuring that you know necessary for successful welding projects.
Techniques For Using 7014 Rod
7014 welding rods are known for their versatility and ease of use. They are an excellent choice for welding in all positions, especially vertical and overhead welding. With their high deposition rates, 7014 rods provide strong and reliable welds in a wide variety of applications. To make the most out of this welding rod, consider the following techniques:
- Preparation: Begin by cleaning the base material thoroughly, removing any rust, paint, or debris. This will ensure proper fusion and a clean weld.
- Amperage settings: Adjust the amperage settings on your welding machine accordingly to match the rod diameter and base material thickness. This will help achieve optimal penetration and prevent under or over-penetration that can weaken the weld.
- Travel speed: Maintain a consistent and steady travel speed to prevent overheating and allow the weld puddle to solidify properly. A slow travel speed may result in excessive heat build-up, while a fast speed may lead to insufficient penetration.
- Angle and technique: Hold the electrode at a 15 to 20-degree angle and drag it along the joint with a slight weave motion. This will ensure good sidewall fusion and allow for even distribution of the molten metal.
Techniques For Using 7018 Rod
The 7018 welding rod is known for its exceptional strength and low hydrogen content, making it an ideal choice for welding projects that require high-quality and crack-resistant welds. To master the use of the 7018 rods, follow these techniques:
- Preparation: Clean the base metal thoroughly to remove any impurities or contaminants that can compromise the weld quality. Use a wire brush or grinder to achieve a clean surface.
- Amperage settings: Adjust the amperage settings on your welding machine based on the rod diameter and the thickness of the base material. The correct amperage ensures proper penetration and fusion of the materials.
- Travel speed: Maintain a steady travel speed, neither too fast nor too slow. This helps in achieving consistent heat distribution and proper solidification of the molten metal.
- Angle and technique: Hold the electrode at a 10 to 15-degree angle and use a short arc length technique. This ensures a focused and concentrated heat on the joint area, resulting in a strong and reliable weld.
By mastering these techniques, you can confidently work with both the 7014 and 7018 welding rods, producing high-quality welds that meet the requirements of your welding projects. Remember, practice makes perfect, so don’t hesitate to experiment and refine your skills to become a proficient welder.
Strength And Quality
When it comes to welding, one of the most important factors to consider is the strength and quality of the welds. In this article, we will explore the differences between the 7014 welding rod and the 7018 welding rod and discuss their respective strengths.
Strength Of 7014 Welds
The 7014 welding rod is known for its excellent deposition rate and ease of operation. It produces welds with good tensile strength, making it suitable for welding projects that require moderate strength. The welds made with 7014 rods are typically smooth and uniform, resulting in a visually appealing finish.
This type of welding rod is commonly used in applications such as structural steel welding, shipbuilding, and general fabrication. Its strength allows it to withstand moderate loads and provides a reliable and durable weld.
Strength Of 7018 Welds
The 7018 welding rod, on the other hand, is known for its high tensile strength and excellent penetration. This makes it ideal for welding projects that require more robust welds, such as heavy machinery, pressure vessels, and bridges.
7018 welds are characterized by their exceptional strength and durability, even in high-stress environments. The rod provides deep penetration into the base metal, resulting in a strong bond that can withstand heavy loads and extreme conditions.
Due to its high strength properties, the 7018 welding rod is often used in critical applications that require welds with superior strength, such as the construction of infrastructure and equipment that must meet stringent safety standards.
Additionally, the 7018 rod produces welds that are less prone to cracking and porosity, further enhancing the overall strength and quality of the weld.
In conclusion, both the 7014 and 7018 welding rods have their strengths and are suitable for different applications. The 7014 rod provides good tensile strength and is commonly used for moderate-strength projects, while the 7018 rod offers exceptional strength and is ideal for applications that require robust welds. Understanding the strengths and qualities of these welding rods will help you choose the right rod for your welding projects, ensuring strong and reliable welds every time.
Electrode Coating
When it comes to welding, the choice of electrode can greatly impact the quality and strength of the weld. Two widely used electrodes in the welding industry are the 7014 welding rod and the 7018 welding rod. Both are known for their exceptional performance, but one key factor that sets them apart is their electrode coating.
Coating On 7014 Rod
The 7014 welding rod is renowned for its versatility and ease of use. This electrode features a thick and creamy flux coating, which serves several purposes during the welding process. The coating not only provides excellent arc stability but also shields the weld puddle from air contamination. This prevents oxidation and ensures a clean, strong weld that is free from harmful impurities.
One of the distinctive traits of the 7014 electrode coating is its ability to produce a smooth and aesthetic weld bead. This makes it highly suitable for applications that require a visually appealing finish, such as ornamental ironwork or decorative metal structures. The coating also facilitates a stable and controlled arc, making it an ideal choice for beginners or less experienced welders.
Coating On 7018 Rod
On the other hand, the 7018 welding rod boasts a different type of electrode coating with unique characteristics. This electrode features a low-hydrogen coating, often referred to as a “low hydrogen electrode.” The primary purpose of this coating is to minimize the risk of hydrogen-induced cracking in the weld metal.
The low-hydrogen coating on the 7018 rods is designed to absorb moisture, preventing it from entering the weld pool and creating hydrogen-related defects. This makes the 7018 electrode a popular choice for welding high-strength steel, pressure vessels, and other critical applications where weld integrity is paramount.
The 7018 electrode coating also contributes to improved arc stability and reduced spatter, resulting in a smoother and more controlled welding process. Furthermore, it offers better resistance to weld contamination and ensures stronger welds with enhanced mechanical properties.
Summary:
7014 Welding Rod | 7018 Welding Rod |
---|---|
Thick and creamy flux coating | Low-hydrogen coating |
Provides excellent arc stability | Minimizes the risk of hydrogen-induced cracking |
Prevents air contamination in the weld puddle | Absorbs moisture to prevent hydrogen-related defects |
Suitable for aesthetically pleasing finishes | Ideal for critical applications and high-strength steel |
Overall, understanding the unique properties of electrode coatings is essential in selecting the right rod for your welding needs. Whether you opt for the 7014 welding rod with its creamy flux coating or the 7018 welding rod with its low-hydrogen coating, you can rest assured that both electrodes offer exceptional performance and are capable of delivering high-quality welds.
Fillet Weld Applications
Fillet welds are commonly used in various welding applications, and the choice of welding rod can significantly impact the outcome of the weld. Understanding the differences between 7014 and 7018 welding rods in fillet weld applications is crucial for achieving high-quality welds.
Use Of 7014 Rod In Fillet Welds
The 7014 welding rod is well-suited for fillet weld applications, especially in projects where speed is of the essence. The rod’s high deposition rate enables quick welds, making it suitable for applications where efficiency is prioritized. Its ability to produce smooth and uniform welds also makes it a popular choice for fillet welds, particularly in non-critical structures.
Use Of 7018 Rod In Fillet Welds
When precision and strength are paramount in fillet welds, the 7018 welding rod shines. Its low hydrogen content and superior mechanical properties make it an ideal choice for welding critical fillet joints, ensuring strong and durable welds. The 7018 rod is well-suited for applications where the integrity of the welds is vital, such as in structural and heavy equipment fabrication.
Welding Machine Compatibility
When it comes to choosing the right welding rod for your project, it’s essential to consider the compatibility with different welding machines. The welding rod you select must be suitable for the specific welding machine you are using to ensure a strong and durable weld.
Compatibility With Different Welding Machines
7014 Welding Rod: This welding rod is known for its versatility and compatibility with various welding machines, including AC and DC welding machines. It is suitable for use with low-amp machines, making it a popular choice for general welding tasks.
7018 Welding Rod: On the other hand, the 7018 welding rod is also compatible with both AC and DC welding machines. However, it is designed for use with higher-amperage machines, typically used for heavy-duty and structural welding applications.
Ensuring Compatibility
- Check the welding machine’s specifications to ensure it is compatible with the welding rod you intend to use.
- Consult with the welding rod manufacturer or supplier to verify compatibility with your specific welding machine.
- Consider the type of welding machine (AC or DC) and its amperage requirements to match with the appropriate welding rod.
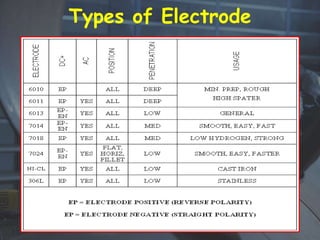
Credit: www.slideshare.net
Cost And Availability
When it comes to choosing the right welding rod for your project, two popular options that often come up are the 7014 and 7018 rods. These rods are known for their reliability, strength, and versatility. However, one important factor to consider before making a decision is the cost and availability of these welding rods.
Cost Comparison Of 7014 And 7018 Rods
Understanding the cost difference between 7014 and 7018 welding rods can help you make an informed decision based on your budget and requirements.
7014 rods are generally more affordable compared to 7018 rods, making them a popular choice for projects where cost is a significant consideration. Welders on a tight budget often prefer the 7014 rods as they deliver decent performance without breaking the bank. However, it’s important to note that the lower cost of 7014 rods can also impact their overall quality, resulting in a shorter lifespan.
On the other hand, 7018 rods are slightly more expensive but offer better quality and durability. These rods are known for their superior weldability and produce stronger welds, making them a preferred choice for demanding projects that require utmost strength and reliability. Although the initial cost may be higher, the long-term benefits of using 7018 rods can outweigh the additional expense.
Availability Of 7014 And 7018 Rods
The availability of welding rods can impact your project timeline and convenience. Here’s what you need to know about the availability of 7014 and 7018 rods:
- 7014 rods are widely available in various stores, making them easily accessible for welders. You can find them in most hardware stores, welding supply shops, and even online platforms. The high availability of 7014 rods ensures that you won’t have to go through any hassle when sourcing them for your welding needs.
- 7018 rods, although slightly less common, are still readily available in many welding supply shops and online marketplaces. While they may not be as easy to find as 7014 rods, you can still obtain them without much difficulty. It’s recommended to plan and check the availability of 7018 rods in your area to ensure you can get them when needed.
In conclusion, considering the cost and availability of welding rods is essential to make an optimal choice for your project. While the 7014 rods offer affordability and decent performance, the slightly pricier 7018 rods deliver superior quality and strength. Additionally, both types of rods are generally available in stores, although 7014 rods tend to have broader accessibility. So, weigh your budget, project requirements, and availability factors to determine which welding rod suits your needs best.
Welding Performance
When it comes to welding, the choice of welding rod plays a crucial role in determining the quality and strength of the weld. Two popular welding rods that are frequently used are the 7014 and 7018 rods. Both of these rods offer different performance characteristics, making them suitable for different welding applications. Let’s take a closer look at the performance characteristics of each rod.
7014 Rod Performance Characteristics
The 7014 welding rod is known for its versatility and ease of use. It is often referred to as a “all-position” rod, which means it can be used in various welding positions, including vertical, horizontal, and overhead. This makes it a popular choice for welding thick materials and structural welding.
The 7014 rod also provides good penetration, allowing for deep and strong welds. It has a light slag that is easily removable, reducing the clean-up time. Additionally, it offers moderate deposition rates, ensuring efficient welding.
7014 Rod Performance Characteristics |
---|
Versatile and suitable for all positions |
Good penetration for strong welds |
Light slag that is easy to remove |
Moderate deposition rates for efficient welding |
7018 Rod Performance Characteristics
The 7018 welding rod is favored for its high tensile strength and excellent weld quality. It is often used for heavy-duty welding applications, such as structural steel fabrication and pipe welding. This rod is specifically designed for low hydrogen welding, which reduces the chances of weld defects and improves the overall strength of the weld.
The 7018 rod also offers deep penetration, ensuring strong and durable welds. It has a relatively heavy slag that provides additional protection to the weld zone and improves the appearance of the weld. This rod has high deposition rates, allowing for faster and more efficient welding.
7018 Rod Performance Characteristics |
---|
High tensile strength for heavy-duty applications |
Designed for low hydrogen welding for improved strength |
Deep penetration for strong and durable welds |
Relatively heavy slag for added protection and better appearance |
High deposition rates for faster and more efficient welding |
In conclusion, both the 7014 and 7018 welding rods offer unique performance characteristics that make them suitable for different welding applications. The 7014 rod is versatile and easy to use, while the 7018 rod provides high tensile strength and excellent weld quality. Understanding these performance characteristics can help you choose the right welding rod for your specific welding needs.
Preheating Requirements
HTML Response:
When it comes to welding, understanding the preheating requirements is crucial for achieving strong and quality welds. Preheating is necessary to prevent the formation of cracks and ensure proper fusion between the base metal and the welding rod. In this blog post, we will compare the preheating requirements for using two popular welding rods: 7014 and 7018.
Preheating Before Using 7014 Rod
Preheating the base metal is not mandatory when using a 7014 welding rod. However, it is recommended to preheat the material if it is thick or has high carbon content to minimize the risk of cracking. Preheating the base metal helps in reducing the cooling rate and overall stress on the welded structure.
Preheating Before Using 7018 Rod
Unlike the 7014 rods, preheating the base metal is often required when using a 7018 welding rod. The need for preheating depends on the thickness and composition of the material. For carbon steels with a thickness of 3/4 inches or more, preheating is typically required to ensure proper weld penetration and minimize the risk of cracking.
When using a 7018 rod, it is important to follow the specific preheating temperature mentioned by the rod manufacturer or as specified by the welding procedure. The preheating temperature should be maintained throughout the welding process to achieve the desired results.
To summarize, while preheating is generally not mandatory when welding with a 7014 rod, it is highly recommended when dealing with thick or high-carbon-content materials. On the other hand, preheating is often required when using a 7018 rod, especially for thicker carbon steels. Following the preheating requirements for each rod will result in stronger, crack-free welds.
Storage And Handling
Proper storage and handling of welding rods are crucial for maintaining their quality and performance. Whether you are working with 7014 welding rods or 7018 welding rods, following the right storage practices will ensure optimal results. In this section, we will discuss storage recommendations for both types of rods to help you prolong their shelf life and maintain their effectiveness.
Storage Recommendations For 7014 Rod
- Store your 7014 welding rods in a dry location, away from any moisture or humidity.
- Ensure that the rods are kept in a well-ventilated area to prevent condensation and minimize the risk of corrosion.
- Use a moisture-resistant container to store the rods, such as a sealed plastic bag or a rod oven.
- Label the container with the type and diameter of the rods to easily identify them.
- Keep the storage area clean and free from debris that can contaminate the rods.
Storage Recommendations For 7018 Rod
- Store your 7018 welding rods in a controlled environment with low humidity levels to prevent moisture absorption.
- Keep the rods in their original packaging or a rod oven to protect them from excessive moisture and humidity.
- If using a rod oven, set the temperature to the manufacturer’s recommended range to avoid overheating or damage.
- Store the rods vertically in a rack or holder, ensuring they are not in contact with any wet surfaces.
- Avoid storing the rods near any chemicals or corrosive substances that can compromise their quality.
By following these storage recommendations, you can ensure that both your 7014 and 7018 welding rods remain in optimal condition for use. Proper storage and handling practices will not only extend their shelf life but also enhance their performance, resulting in high-quality welds.
Environmental Impact
When evaluating different welding rods, it’s essential to consider their environmental impact. The choice between 7014 and 7018 welding rods can significantly affect the environment. Each type of rod comes with its own set of environmental considerations that should be taken into account before making a decision.
Environmental Considerations For 7014 Rod
The 7014 welding rod is known for its ease of use and versatility. However, from an environmental standpoint, it’s important to note that this rod generally requires higher amperage, leading to increased power consumption. This can contribute to higher levels of energy consumption and potentially have a greater impact on the environment. Additionally, the flux coating on 7014 rods contains higher levels of iron powder, potentially impacting the environment during the welding process.
Environmental Considerations For 7018 Rod
On the other hand, the 7018 welding rod is recognized for its high deposition rates and strong welds. In terms of environmental impact, this rod generally operates at a lower amperage, resulting in reduced power consumption. This can lead to lower levels of energy consumption and, consequently, a more eco-friendly welding process. 7018 rods also tend to produce lower levels of smoke and fumes compared to 7014 rods, which can contribute to a more environmentally friendly work environment.
Safety Precautions
Welding with 7014 and 7018 rods requires a set of safety measures to ensure the protection of both the welder and the surroundings. By strictly adhering to these precautions, one can minimize the risks associated with welding work and create a secure environment for all involved.
Safety Measures For Using 7014 Rod
- Wear appropriate protective gear, including a welding helmet, gloves, and flame-resistant clothing, to shield yourself from sparks and intense heat.
- Work in a well-ventilated area to prevent inhalation of harmful fumes and vapors produced during the welding process.
- Inspect the welding equipment regularly to ensure that it is in good working condition and free from defects that may compromise safety.
- Keep a fire extinguisher nearby to tackle any potential fire hazards that may arise during welding.
- Implement proper storage and handling procedures for the 7014 rods to prevent accidental damage and ensure its efficacy.
Safety Measures For Using 7018 Rod
- Utilize a suitable welding area with non-flammable flooring to prevent fire hazards and ensure a stable working environment.
- Adhere to proper grounding practices to minimize the risk of electric shock and ensure the safety of equipment and personnel.
- Adopt safe handling techniques for the 7018 rods to prevent injuries and maintain the integrity of the welding material.
- Regularly inspect and maintain electrode holders and welding equipment to prevent malfunctions that could compromise safety.
- Use protective screens to shield nearby individuals from the intense light produced during welding with the 7018 rod.
Credit: m.facebook.com
Industry Standards
When it comes to welding rods, it’s important to prioritize conformance to industry standards. Choosing the right welding rod can make a significant difference in the quality and strength of a weld. In this blog post, we will compare the popular welding rods 7014 and 7018, focusing on their adherence to industry standards.
Conformance To Industry Standards
In the welding industry, standards are established to ensure uniformity, reliability, and safety. Both 7014 and 7018 welding rods are widely used in various applications and are known for their performance. Let’s dive deeper into how each of these rods complies with the industry standards.
7014 Welding Rod
The 7014 welding rod is a versatile rod that is often used for general-purpose welding. It is known for its smooth arc characteristics and good deposition rates. This rod conforms to the American Welding Society (AWS) A5.1 specifications, which ensures its quality and meets the necessary safety requirements.
It is important to highlight that the 7014 welding rod can withstand higher levels of impurities in the base metal compared to other rods. This makes it suitable for welding on slightly rusty or dirty surfaces, providing convenience and time-saving benefits.
7018 Welding Rod
The 7018 welding rod is another popular choice that is widely used in the industry. It is known for its high-quality welds and excellent mechanical properties. This rod also conforms to the AWS A5.1 specifications, ensuring its reliability and adherence to industry standards.
Unlike the 7014 rod, the 7018 welding rod requires a bit more care when it comes to base metal cleanliness. It is designed for welding on clean and properly prepared surfaces, which guarantees more robust welds.
Comparison
Welding Rod | Conformance to AWS A5.1 | Base Metal Cleanliness |
---|---|---|
7014 | Yes | Tolerates higher levels of impurities |
7018 | Yes | Requires clean and properly prepared surfaces |
In conclusion, both the 7014 and 7018 welding rods adhere to industry standards as specified by AWS A5.1. However, their base metal cleanliness requirements differ, making each rod more suitable for specific applications. Choosing the right welding rod depends on the project’s requirements and the condition of the base metal. Consider consulting with a welding professional or referring to the manufacturer’s recommendations for the best results.
Welding Code Compliance
When it comes to welding, following welding codes and regulations is of utmost importance. Compliance with these codes ensures the safety, quality, and durability of the welded structures. In this article, we will explore the welding code compliance of two popular welding rods: 7014 and 7018.
Compliance With Welding Codes And Regulations
Welding codes and regulations are standards established by various organizations to ensure the proper and safe execution of welding operations. They provide guidelines and requirements for welding procedures, materials, inspections, and more. Compliance with these codes is crucial to meet industry standards and legal requirements.
7014 Welding Rod Compliance
The 7014 welding rod is a versatile electrode commonly used for mild or low-alloy steel welding. It is known for its excellent arc stability, all-position welding capabilities, and smooth bead appearance. When it comes to compliance with welding codes, the 7014 rod usually meets the requirements set by industry standards and regulatory bodies, such as the American Welding Society (AWS) or the International Organization for Standardization (ISO).
7018 Welding Rod Compliance
The 7018 welding rod is another popular electrode widely used for structural welding applications. It offers high tensile strength, low hydrogen content, and superior weld quality. Similar to the 7014 rods, the 7018 welding rod is usually compliant with industry welding codes and regulations. It meets the standards outlined by organizations like AWS and ISO, ensuring the welds made with this rod adhere to recognized quality and safety guidelines.
Overall, both the 7014 and 7018 welding rods are commonly used in welding projects that require code compliance. These rods have undergone rigorous testing and meet the necessary standards, giving welders confidence in their weld quality and structural integrity.
Credit: github.com
References
The comparison between 7014 welding rods and 7018 welding rods is a crucial aspect when it comes to selecting the appropriate welding method for specific projects. Understanding their differences in terms of electrode composition, welding positions, and applications is essential for welders.
Citations For Further Reading
For those looking to delve deeper into the world of welding rods, here are some additional resources that provide valuable information on the comparison between 7014 and 7018 welding rods:
- Lincoln Electric: A renowned name in the welding industry, Lincoln Electric offers insightful articles and blogs on various welding rod types, including the 7014 and 7018 varieties. Find their comprehensive guide on their website.
- Miller Electric: Miller Electric, another leading welding equipment manufacturer, also provides detailed information on different welding rod options. Their website features a comprehensive comparison between the 7014 and 7018 welding rods, discussing their unique characteristics and applications.
- Welding Tips and Tricks: This popular welding blog, run by experienced welder Jody Collier, offers practical advice, tips, and comparisons on various welding techniques and products. Check out their articles specific to 7014 and 7018 welding rods to gain valuable insights from a welding expert’s perspective.
- The Fabricator: As a renowned industry magazine, The Fabricator covers a wide range of welding-related topics. Their website includes articles, research papers, and industry expert opinions that can further enhance your knowledge of welding rods, including the comparison between 7014 and 7018 rods.
Whether you are a hobbyist welder or a professional looking to improve your welding skills, these resources can provide valuable information to help you make an informed decision about which welding rod is best suited for your specific needs.
Frequently Asked Questions Of 7014 Welding Rod Vs 7018
Is 7014 As Good As 7018?
Yes, 7014 and 7018 are both good welding electrodes, but they have different applications and characteristics.
What Is 7014 Welding Rod Good For?
7014 welding rods are suitable for welding high-strength steel, such as construction or structural materials. They offer good penetration and produce clean welds.
Is 7014 Uphill Or Downhill?
7014 is neither uphill nor downhill. It is just a numerical value and does not have a directional connotation.
What Is The Difference Between E7010 And E7018 Electrode?
E7010 and E7018 electrodes differ in their characteristics for welding. E7010 is used for deep penetration in thicker materials, while E7018 is used for low-hydrogen welding of various thicknesses. Both electrodes provide different welding properties to suit specific applications.
What Is The Difference Between 7014 Welding Rod And 7018?
7014 welding rod and 7018 have different coating compositions which influence their performance and suitability for various applications.
Conclusion
To summarize, the choice between 7014 welding rods and 7018 welding rods ultimately depends on the specific welding project at hand. While 7014 rods offer easier use and a smoother finish, 7018 rods provide stronger and more durable welds. It’s crucial to consider factors such as material type, joint strength, and intended application to make an informed decision.
Remember to consult with a welding professional for personalized guidance and ensure the best results for your welding needs.