An electrode chart for arc welding is a reference guide for selecting the appropriate electrode based on the welding job and materials involved. It outlines the electrode classification, current settings, and positions applicable for various tasks.
Arc welding requires precision, and the success of a welding project hinges on the appropriate selection of electrodes. Each electrode in the chart has unique properties tailored to different metal types, thicknesses, and welding positions. Welders rely on the information in the electrode chart to ensure strong welds with optimal penetration and minimal defects.
It’s vital to consult this chart to match the electrode with the specific requirements of the welding job, considering factors such as the base metal’s composition, required strength, and the desired characteristics of the final weld. By adhering to the specifications of the electrode chart, welders can achieve efficient and high-quality welds in both industrial applications and personal projects. Understanding this chart is fundamental for novice and experienced welders to ensure a solid foundation for any arc welding task.
Electrode Chart Explanation
Welcome to the comprehensive guide on the Electrode Chart Explanation for Arc Welding. This chart is pivotal for welders to select the appropriate electrode for their projects, ensuring a strong and durable weld. Let’s delve into the significance of choosing the right electrode and how to read the classification numbers that will guide you toward making an informed choice for your welding tasks.
Significance Of The Correct Electrode
Selecting the correct electrode is crucial for the success of any welding job. Using the right electrode affects everything from the ease of welding to the strength, corrosion resistance, and even the appearance of the final weld. Electrodes are designed for different types of metals and welding positions, and choosing the wrong one can lead to weak welds that may fail under stress. Therefore, understanding the electrode classification and its chart is of utmost priority for professional outcomes.
Understanding Electrode Classification Numbers
Every electrode comes with numbers that are not random but provide essential information about the electrode’s characteristics. For instance, a common electrode used in the industry is the E6013. Here, ‘E’ signifies an arc welding electrode. The following two digits, ’60’, represent the minimum tensile strength of the weld the electrode will produce, measured in thousands of pounds per square inch (psi). The ‘1’ in the third position indicates the electrode’s suitable welding positions, while the final digit ‘3’ reveals the type of coating and current options it can work with.
Interpreting Chart Details For Optimal Use
An electrode chart is not just a mere figure; it is a detailed guide that helps optimize electrode use for various welding applications. Such a chart might present a set of recommended amperages for different electrode diameters, which is crucial for achieving the best penetration and avoiding weld defects. Additionally, the graph may include information on the metal types each electrode can be used with, ideal welding angles, and whether the electrode is suitable for AC, DC+, or DC- currents. Grasping the information presented on an electrode chart ensures welders can select the best electrode for their work, resulting in higher-quality welds.
Material Compatibility And Electrodes
Material Compatibility and Electrodes are essential for achieving quality welds in arc welding. Understanding the appropriate electrode for the welded material ensures strong, reliable joins and optimal welding performance. Different materials respond differently when subjected to the intense heat of the welding arc, making the choice of electrode critically important. Selecting the wrong electrode can result in poor weld quality, increased defects, and potential failure of the welded assembly. Let’s explore how matching electrodes to your workpiece materials and considering the influence of the base material can enhance your welding outcomes.
Matching Electrodes To Workpiece Materials
Matching the right electrode to the material of the workpiece is a pivotal step in arc welding. It’s not just about getting the job done but ensuring the weld is strong, durable, and suitable for its intended application. Use the following guidance to select the correct electrode:
- Identify the Material: First, determine the type of material you will be welding, whether it’s carbon steel, stainless steel, aluminum, or another metal.
- Electrode Composition: Choose an electrode with a composition similar to the workpiece material. This compatibility reduces the chances of cracking or weak welds.
- Electrode Classification: Refer to the American Welding Society (AWS) electrode classification to find the suitable electrode type. For example, a popular choice for welding mild steel is the AWS E6013.
- Material Thickness: Consider the thickness of the material when selecting electrode size. Thicker materials typically require larger diameter electrodes to achieve adequate penetration.
Influence Of Base Material On Welding Quality
The base material is a determining factor in the overall quality of the weld. It influences not only the choice of electrode but also the welding technique and settings. Keep these considerations in mind:
Base Material | Welding Consideration | Recommended Electrode |
---|---|---|
Carbon Steel | Widely welded material, forgiving to various electrodes. | AWS E6011, E6013, E7018 |
Stainless Steel | Requires careful control to avoid warping and maintain corrosion resistance. | AWS E308L, E316L |
Aluminum | It is conductive, requires higher amperage, and is susceptible to impurities. | AWS E4043, E5356 |
Critical factors like thermal conductivity and expansion rate of the base material also influence electrode choice. For instance:
- Conductivity: Materials with high thermal conductivity may require electrodes that can operate at higher currents to ensure proper heat input.
- Expansion Rate: Materials with expansion rates different from the electrode material can cause stresses during cooling, leading to cracks. Selecting an electrode that closely matches the expansion rate is vital.
In summary, aligning electrode choice with workpiece materials is non-negotiable for high-quality arc welding. By understanding the properties of both the electrode and the base material, welders can execute their tasks with the confidence that their welds will be solid and durable.
Differentiating Between Common Electrodes
Embarking on the journey of arc welding requires a solid understanding of the tools at one’s disposal, beginning with the electrodes. Each welding electrode plays a pivotal role in the success of the welding process, influencing everything from the ease of use to the strength and finish of the weld. With many electrodes available, differentiating between common electrodes helps welders select the optimal tool for their specific project needs.
Overview Of Various Electrode Types
Electrodes for arc welding are classified by the American Welding Society (AWS) and distinguished by letters and numbers denoting their characteristics and capabilities. These guidelines allow welders to match electrode types with the job at hand, considering factors such as the metal being welded, the position of the weld, and the desired welding properties.
Key Characteristics And Applications
Each electrode type is tailored for different scenarios and has its own features. Understanding these key characteristics and applications is essential for achieving desired results.
Electrode Type | Description | Applications |
---|---|---|
E6010 | A fast-freeze cellulose-sodium electrode ideal for vertical and overhead welding | Used for pipeline welding and in shipyards |
E6011 | This electrode operates on AC and DC currents and is favorable for poorly fitted joints. | Suitable for general repair work and non-critical paths |
E6013 | A rutile-iron powder electrode that offers a smooth and stable arc | Great for thin metals, small home workshops, and general maintenance |
E7018 | Low-hydrogen iron powder electrodes are known for producing rugged and crack-resistant welds. | Widely used in structural welding, including bridges and buildings |
E7024 | High-speed iron powder electrode that yields a high deposition rate | Best for flat and horizontal welds on thick plates |
Focusing on each electrode type’s specific uses and strengths allows welders to use the right tools for their requirements, producing high-quality welds tailored for the application. For instance, some electrodes are designed for smooth surface applications and others for deep penetration into the workpiece.
Navigating The Electrode Chart Properly
Welding professionals and enthusiasts recognize the importance of selecting the right electrode for their arc welding projects. Navigating the electrode chart properly is essential to achieving strong, durable, and quality welds. Understanding this chart helps you quickly match the correct electrode to the needs of your specific project based on factors such as base material, welding position, and desired mechanical properties. Let’s use the electrode chart efficiently with a step-by-step guide and some handy tips for quick reference.
Step-by-step Guide To Using The Chart
- Identify the Base Material: Your first step is determining the base material you will be welding. This influences the electrode’s required composition to ensure compatibility and optimal performance.
- Refer to the Electrode Specification: Electrodes are classified by a series of alphanumeric codes. These codes describe the electrode’s characteristics, such as tensile strength, welding position, and type of coating or current.
- Please select the Appropriate Electrode. Cross-reference the base material and its thickness with the electrode specifications to find the right fit. The chart may provide a range of suitable electrodes.
- Consider the Welding Position: Welding position (flat, horizontal, overhead, or vertical) is a crucial factor in electrode selection, affecting the flux’s ability to solidify and support the weld pool.
- Check the Power Source: Ensure the electrode is compatible with the available AC, DC, or both. This information is typically denoted in the electrode chart.
- Analyze Mechanical Properties: Review the desired mechanical properties, such as flexibility, tensile strength, and toughness, which are specified in the chart.
- Final Verification: Once an electrode type is chosen, verify all parameters align with your project requirements before commencing the welding process.
Tips For Quick Reference During Projects
- Keep a printed or digital copy of the electrode chart readily accessible in your workspace for a quick lookup.
- Create a condensed version or cheat sheet of the chart that highlights the most commonly used electrodes in your projects.
- Use bookmarks or tabs to mark specific chart sections for different materials or processes.
- Leverage color coding to differentiate electrode types visually and reduce search time.
- Memorize the meaning of electrode specification codes to expedite the selection process rather than consulting the chart each time.
- Employ an app or a digital tool that allows you to input your project requirements and present the appropriate electrode options based on the chart.
Understanding and utilizing the electrode chart for arc welding effectively streamlines the electrode selection process, ensuring each project’s success due to the accurate and well-suited material choice.
Impact Of Thickness On Weld Quality
Understanding the impact of thickness on weld quality is crucial for achieving optimal strength and durability in metal structures. The proper fusion between metals depends on carefully considering electrode characteristics and operating conditions. Notably, the thickness of the materials being joined plays a significant role in determining the appropriate electrode type and size.
Role Of Electrode Diameter In Joint Penetration
The diameter of an electrode directly affects the depth of penetration in arc welding. Choosing the correct electrode diameter ensures the weld reaches the required depth within the workpiece. The following are key points to consider:
- Thin materials may require smaller electrodes to prevent burn-through and guarantee an adequate weld without excessive heat input.
- Conversely, thicker materials demand larger electrodes to achieve sufficient penetration. This ensures the weld’s root is firm and the join is secure.
- Using an electrode that is too large can lead to overheating and compromised weld quality, while too small may result in inadequate penetration and potential weld failure.
The table below showcases the relationship between material thickness and recommended electrode diameter.
Material Thickness | Recommended Electrode Diameter |
---|---|
Up to 3mm | 2.0 mm or smaller |
3mm to 12mm | 2.5 to 3.2 mm |
12mm and above | 4.0 to 5.0 mm or larger |
Selecting The Right Electrode For Welding Positions
The electrode chosen for a welding project must also suit the position in which welding takes place:
- Flat or horizontal welding positions allow for most electrode types due to gravity assisting in the placement of the molten metal.
- Electrodes with a fast-freeze or fill-freeze characteristic are generally selected for vertical or overhead positions. These electrodes form a solid weld quickly, preventing molten metal from dropping.
- Electrodes categorized as E6010 or E6011 are known for their deep penetration and are typically used in root passes due to their fast-freeze characteristics.
- Similarly, E7018 electrodes provide medium penetration with a fill-freeze characteristic, suitable for both fill and cap passes in various positions.
The selection should always align with the welding position to achieve a high-quality, defect-free weld.
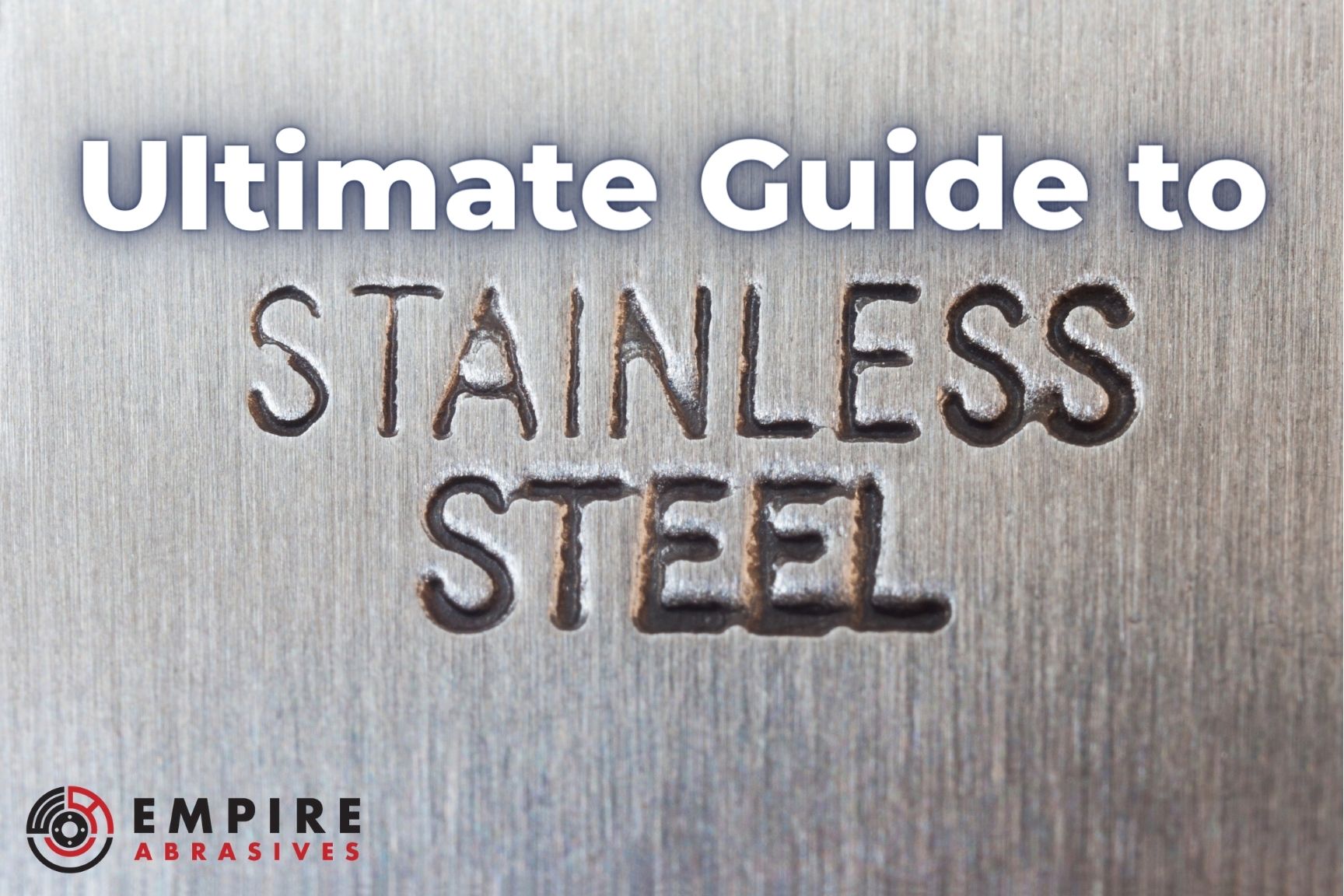
Credit: www.empireabrasives.com
Adjusting Amperage Based On Chart
When it comes to arc welding, precision is crucial — and that precision extends beyond your technique to the equipment settings. For any experienced welder, understanding the correct amperage for the specific electrode being used is not just helpful; it’s non-negotiable. Adjusting the amperage per the electrode chart is fundamental to achieving the best weld quality and maintaining the integrity of the welded joints. Let’s delve into the reasons for setting the correct current and how an electrode chart can be an essential guide.
Importance Of Correct Current Settings
Setting the current correctly for arc welding is paramount for numerous reasons. Incorrect amperage can lead to weak welds, excessive spatter, or even damage to the workpiece. Amperage that’s too high can melt through the metal, while an amperage that’s too low fails to penetrate adequately. Optimal current settings ensure the electrode performs as it should, resulting in a strong, clean, and visually pleasing weld.
How The Electrode Chart Helps In Fine-tuning Amperage
The electrode chart comprehensively guides the amperage settings across various electrode types and sizes. It assists welders in choosing the proper amperage based on the metal’s thickness and the weld’s position. By consulting the chart, you can:
- Determine the starting amperage based on the electrode diameter.
- Adjust for the metal thickness, which affects the required heat input.
- Consider the welding position (flat, vertical, overhead), as gravity affects weld pool behavior.
This fine-tuning enables welders to apply the right amount of heat, leading to optimal fusion and weld strength.
Remember, while the electrode chart offers excellent baseline settings, the best welders will also rely on experience and intuition to make slight adjustments for the perfect weld. So, use the electrode chart as a starting point and fine-tune it as necessary to master the art of arc welding.
Influence Of Gasses On Arc Welding
Arc welding’s success hinges on the correct balance and selection of gases—a critical factor in the process. The gases you choose directly influence the arc’s stability, the weld’s quality, and the level of protection against environmental contaminants like oxygen and nitrogen. This discussion focuses on understanding the role of shielding gases and making informed choices based on an electrode chart for arc welding.
Types Of Shielding Gases Used In Arc Welding
Shielding gases are pivotal in arc welding, an invisible force field that protects the weld pool from atmospheric contamination. These gases can be pure or mixed, and each type brings its properties to the welding performance.
- Argon (Ar): Often used for its inert quality, it is excellent for creating a stable arc and minimizing spatter.
- Carbon Dioxide (CO2): Enables deep penetration of the weld but can increase spatter.
- Helium (He): Promotes high heat input and faster welding speeds but can be costly.
- Oxygen (O2): Often added in small quantities to other gases to stabilize the arc and improve weld pool fluidity.
- Mixed Gases: Combinations like Argon-CO2, Argon-O2, and Argon-He are common to balance the benefits and control bead appearance.
How To Choose Gases Based On The Electrode Chart
Selecting the suitable gas for your welding project involves consulting an electrode chart. The chart provides a comprehensive guide on the compatibility of electrodes with the right type of welding gas, aiming to achieve optimal results.
Electrode Type | Recommended Shielding Gas |
---|---|
E6010 | Pure CO2 |
E6013 | Argon-CO2 mix |
E7018 | Argon-25% CO2 |
E7024 | Argon-O2 mix |
Stainless Steel | Tri-mix (He-Ar-CO2) |
The chart above provides a snapshot of potential gas choices, but application specifics, material, and desired weld characteristics must always be considered. Match the electrode type with the gas that optimizes protection and performance for your project’s requirements.
Maintaining Electrode Quality
Every skilled welder knows that the integrity of arc welding operations strongly depends on the quality of the electrodes in hand. Electrode quality can significantly influence weld strength, durability, and overall project success. It’s not just about selecting the right electrode type for the job; maintaining that electrode in its prime condition is paramount. Improper handling or storage can lead to moisture absorption, contamination, or damage, compromising the weld’s performance and reliability. In this segment, we will explore practical methods to preserve electrode quality, guided by a precise electrode chart for arc welding.
Importance Of Proper Electrode Storage
Maintaining the electrodes’ integrity begins with optimal storage conditions. The primary enemy of electrode efficacy is moisture – it can devastate the electrodes’ performance. Moist electrodes can cause problems like porosity, weak weld seams, and increased spatter. This is why proper storage solutions are not just a recommendation but a critical aspect of the welding process.
Storing Electrodes According To Chart Recommendations
To ensure that electrodes retain their properties and deliver the expected results, refer to the manufacturer’s electrode chart for specifics on storage. These charts provide invaluable information on humidity control, temperature requirements, and reconditioning processes if the electrodes have been exposed to moisture.
- Temperature Controlled: Store electrodes in a dry, temperature-controlled environment to prevent moisture uptake.
- Humidity Restrictions: Keep humidity levels in check per the chart’s recommendations — often below a certain threshold.
- Original Packaging: Until use, keep electrodes in their original packaging to protect against environmental contaminants.
- Reconditioning: If exposure to moisture is suspected, adhere to the reconditioning instructions on the electrode chart to restore quality.
By setting the correct storage conditions based on the electrode chart, welders can increase electrode life and ensure consistent welding performance.
Frequently Asked Questions On Electrode Chart For Arc Welding
What Is An Electrode Chart In Arc Welding?
An electrode chart for arc welding is a reference guide. It lists different types of welding electrodes. It also shows their applications, material compatibility, and amperage settings. Welders use it to select the proper electrode for a job.
How To Read An Electrode Classification Number?
An electrode classification number reveals electrode type and properties. It includes tensile strength, welding position, and flux coating. Decoding the number helps welders choose the right electrode for specific welding requirements.
Which Electrodes Are Best For Thin Metal Arc Welding?
For thin metal, small-diameter electrodes are best. Options like E6010 or E6011 are ideal because they offer deep penetration. They have a fast freeze characteristic suited for more delicate materials, ensuring a solid weld.
Can The Same Electrodes Be Used For AC and DC welding?
Not all electrodes are compatible with both AC and DC welding. Some, like the E6010, are primarily used with DC. However, the E6011 and E6013 types work well with AC and DC currents.
Conclusion
Selecting the right electrode for arc welding can make or break your project. It’s essential to match the electrode to the metal type and thickness. This chart serves as your quick reference guide to achieving solid and durable welds. Keep it handy, and ensure your welding process is efficient and effective.
Let this be the foundation for all your successful welding endeavors!