Flux core welding is a viable method for joining exhaust pipes. It allows for strong bonds without the need for a shielding gas.
Flux core welding, a subset of wire feed welding, is commonly utilized for its efficiency and portability, which make it ideal for exhaust pipe repairs and fabrication. The flux core in the wire creates a shielding gas when it’s heated, which is essential for preventing contamination during welding.
This technique is beneficial in outdoor conditions or in environments where a gas tank cannot be accommodated. Using flux core welding for exhaust pipes allows for quick, robust repairs even for beginners, provided they adhere to safety standards and proper welding procedures. It is an excellent solution for automotive enthusiasts or professionals looking to execute quality welds with minimal equipment.
What Is Flux Core Welding?
Flux core welding—or FCAW (Flux Cored Arc Welding)—is a semi-automatic or automatic arc welding process revered for its versatility and speed. This welding technique is especially beneficial for welding exhaust pipes, where metal joining is complex due to the cylindrical shapes and hard-to-reach spots. Flux Core Welding stands out in its simplicity and efficiency, making it a popular choice for both professionals and DIY enthusiasts in the automotive industry. Let’s dive into the nuts and bolts of flux core welding, understanding its definition, process, materials, and techniques.
Definition and Process
Definition And Process
Flux core welding leverages a continuous tubular wire filled with flux to shield the arc from contamination. This method simplifies the welding process, as it doesn’t necessitate a separate shielding gas. Upon heating, the change melts and forms a gas that protects the weld pool from atmospheric gases such as oxygen and nitrogen, which can weaken the weld. Moreover, it includes a slag layer over the completed weld, which can be easily chipped away upon cooling.
The process of flux core welding involves several steps:
- Preparing the metal: Cleaning the surfaces to be welded to ensure proper adhesion.
- Choosing the correct wire: Select the appropriate flux core wire diameter and composition.
- Setting up the equipment: Adjusting the voltage, amperage, and wire feed speed.
- Welding: Initiating the arc and creating a bead by moving the torch at the right speed and angle.
- Cooling: Allowing the welded area and slag to cool.
- Cleaning: Chipping away the slag to reveal the strong, protected weld underneath.
Materials and Techniques
Materials And Techniques
A variety of materials can be joined using flux core welding. This method is particularly well-suited for welding steel, including stainless steel and carbon steel, making it ideal for exhaust pipes that require high strength and durability. Alloys like nickel can also be welded with the flux core process. Here are some fundamental techniques and considerations:
- Wire selection: Using a wire that complements the metal being welded is crucial.
- Machine settings: Tweaking the settings based on the material thickness and the position of the weld.
- Welding technique: A push or pull technique is employed, depending on the desired penetration and bead shape.
- Safety: Flux core welding generates fumes and slag, so adequate ventilation and safety gear like gloves and masks are imperative.
Expert welders often develop their techniques further, refining their control and adapting to different welding positions. Their expertise allows for solid and durable welds on exhaust pipes, which must withstand significant mechanical stress and high temperatures.
Importance Of Welding In Exhaust Systems
The integrity of an exhaust system plays a pivotal role in the operational excellence of any vehicle. Fusing parts flawlessly is of the utmost importance to ensure that the system functions correctly and withstands the test of time. Flux core welding has become a go-to method for fabricating and repairing exhaust pipes due to its efficiency and durability in handling high temperatures and corrosive gases. Let’s delve into why welding, especially with a flux core process, is critical in constructing and maintaining exhaust systems.
Function And Durability
The exhaust system is essential for channeling hazardous gases away from the vehicle’s occupants and reducing noise. Welding is the cornerstone that ensures all parts of the exhaust work in harmony. Quality welds support the functionality of the exhaust, allowing it to do its job effectively without the risk of leaks or breakages that could lead to hazardous conditions. With flux core welding, exhaust pipes acquire a strong bond resistant to rust and can endure the vibration and thermal expansion associated with daily vehicle operation. This capability to withstand extreme environments makes flux core welds ideal for ensuring the longevity and reliability of exhaust systems.
Impact On Performance And Emissions
It’s not just the longevity of the exhaust system that benefits from impeccable welding—vehicle performance and emission control also hinge on the quality of these joints. A well-sealed exhaust system enables optimal gas flow and backpressure, which can enhance engine efficiency. On the other hand, a poorly welded exhaust can result in leaks, leading to increased emissions and the potential for failing emission tests. Flux core welding provides a solution with deep penetration capabilities, establishing seals that meet the rigorous demands for maintaining low emission levels and promoting peak vehicle performance.
Advantages Of Flux Core Welding For Exhaust Pipes
Flux core welding offers many benefits, making it an ideal choice for working on exhaust pipes. With its unique approach to handling metals, this welding technique stands out in the automotive repair and fabrication industries. Here, we’ll explore the key advantages of using flux core welding when tackling the challenges of welding exhaust pipes.
Strength And Durability
Flux core welding is renowned for producing some of the strongest bonds crucial for the integrity of exhaust systems. It penetrates deep into the metal, creating joints that withstand high pressure and intense vibrations. The outcome is a durable weld that lasts for an extended period, ensuring that exhaust pipes can handle the demands of daily vehicular operation.
- Penetration depth yields robust joints.
- Long-lasting performance even under harsh conditions
- Resilience against breakage, ensuring safety and reliability
Corrosion Resistance
Exhaust pipes are susceptible to corrosion, but flux core welding offers enhanced protection. Due to its slag-inclusive process, it creates a protective barrier that helps to ward off rust and oxidation. This makes flux core welding not just a method for joining metals but also a way to prolong the life of the exhaust pipe by preventing corrosive damage.
Factors Contributing to Corrosion Resistance | Benefits |
---|---|
Slag production | Creates a protective layer over the weld |
Deep penetration | Reduces porosity and exposure to elements |
Cost-effectiveness
With its flexibility and efficiency, flux core welding is a cost-effective exhaust pipe repair and fabrication solution. This welding method doesn’t require an external shielding gas, which can lead to lower operational costs. In addition, flux core welding can be performed quickly, reducing labor time and expense. The speed and efficiency of flux core welding ensure that projects are completed on time and within budget.
- No need for shielding gas reduces expenses
- Quick application cuts down on labor costs
- High productivity levels boost overall cost efficiency
Considerations For Flux Core Welding Exhaust Pipes
When welding exhaust pipes with a flux core welder, a handful of factors come into play to ensure a robust and lasting weld. Whether you’re a professional welder or a DIY enthusiast, considering the following aspects can make a significant difference in the success of your project. Flux core welding, known for its convenience outside a traditional welding shop, requires specific attention to details that might not be as critical in more controlled environments. Let’s delve into the essential considerations for flux core welding exhaust pipes.
Welding Environment
The environment where you perform flux-core welding directly affects the quality and safety of your work. Unlike MIG welding, flux core welding does not require a shielding gas, making it suitable for outdoor conditions where wind can disperse a protective gas. However, certain environmental conditions can still compromise weld integrity. Prioritize the following:
- Shield the welding area to prevent wind from affecting the weld pool’s cooling.
- Maintain a clean work area free of contaminants that can be introduced into the weld.
- Ensure good ventilation to eliminate fumes and welding gases.
- Work under a canopy or shade to protect yourself and the equipment from direct sunlight.
Materials And Thickness
Flux core welding can join a wide range of metals, but it’s essential to select the correct wire for the material of your exhaust pipe. Additionally, the thickness of the material will dictate your welding process. Consider these points:
- Match the wire type to the exhaust metal, predominantly steel or stainless steel.
- Choose the appropriate wire diameter. Thinner wires are more suitable for lower-thickness metals and vice versa.
- Adjust your welder settings to the material thickness, including amperage and wire feed speed.
- Prepare the joint design accordingly to ensure proper penetration and weld strength.
Quality Control And Inspections
Rigorous quality control and inspections are indispensable to ensure that exhaust pipe repairs or fabrications meet safety and performance standards. Incorporate the following into your process:
- Perform a visual inspection of each weld, looking for inconsistencies or defects like porosity or cracks.
- Use non-destructive testing methods, when necessary, for critical applications.
- Keep track of the welder’s travel speed and technique to avoid common issues such as undercuts or lack of fusion.
- Adherence to specifications is crucial – ensure all welds follow the guidelines for applying the exhaust system.
Best Practices For Flux Core Welding Exhaust Pipes
Best Practices for Flux Core Welding Exhaust Pipes are essential for anyone working with vehicles’ emission systems. Flux core welding does not require a shielding gas, making it ideal for outdoor welding and those hard-to-reach spots on exhaust pipes. Mastery of this technique ensures strong, durable welds that can withstand the harsh conditions to which exhaust pipes are typically exposed. Let’s explore the practices that will elevate the welding quality and longevity.
Preparing The Pipe
Preparation is critical to a successful flux core weld. It begins with cleaning the exhaust pipe thoroughly. Remove any oil, dirt, or rust from the welding area to prevent contamination. Use a wire brush or grinder for cleaning, and pay extra attention to where the wires will lay. After cleaning, align and clamp the pipes to hold them steady. This will ensure precision and avoid unnecessary movement resulting in a poor weld.
Choosing The Right Flux Core Wire
Selecting an appropriate wire is crucial for practical exhaust pipe welding. Options vary depending on the material and thickness. Use E71T-GS wires for single-pass applications and E71T-11 wires when multiple passes are required. For stainless steel exhaust systems, opt for a wire explicitly designed for stainless steel, such as AWS A5.22 welding wire. Ensure the wire diameter is appropriate for the thickness of the metal being welded.
Welding Techniques And Settings
The proper technique and welding settings make a big difference. Use a drag technique, pulling the gun away from the completed weld, which offers better visibility and deeper penetration. Maintaining a consistent speed and angle ensures a steady flow and even weld. Regarding settings, fine-tune the welder to the correct voltage and amperage to match the thickness of the pipes and the wire. Typically, thin exhaust pipes require lower voltage settings to prevent burn-through.
Pipe Thickness | Wire Diameter | Amperage | Voltage |
---|---|---|---|
Up to 0.8 mm | 0.30″ | 90-130 A | Lower setting |
0.8 – 1.6 mm | 0.35″ | 120-150 A | Medium setting |
1.6 mm and above | 0.45″ | 150-180 A | Higher setting |
Always perform test welds on scrap materials before starting on the exhaust pipes. This ensures the settings are optimized for the material you are working with. Adjust as necessary for the best result.
Troubleshooting Common Issues In Flux Core Welding
Flux core welding is a prevalent technique for joining exhaust pipes due to its versatility and effectiveness in producing robust welds. Even with its merits, practitioners can encounter various challenges that may affect the quality of the weld. Addressing these common issues requires a blend of expertise and practical troubleshooting solutions. Let’s delve into these issues and learn how to mitigate them to ensure seamless and durable welds for your exhaust pipes.
Porosity, Spatter, And Undercut
Identifying and rectifying defects is crucial in flux core welding. You may encounter three common defects: porosity, spatter, and undercut.
- Porosity: As small cavities or holes within the weld, porosity weakens the weld integrity. Ensuring a clean work surface and using the correct voltage settings can minimize this issue. Adjust the welding parameters and avoid excessive moisture in the air to tackle porosity.
- Spatter: Unwanted droplets of molten material are not only a nuisance but also compromise the finish of the weld. To reduce spatter, fine-tune the welding machine’s wire feed speed and voltage and select the appropriate contact tip size.
- Undercut: This groove that occurs along the edges of the weld can lead to weak points. To prevent undercutting, maintain a steady travel speed and angle your welding gun correctly.
Ensuring Proper Fusion
Proper fusion is a cornerstone of solid and durable welds. Flux core welding must create a homogenous bond between the exhaust pipe materials. How do you ensure this?
- Verify the cleanliness of the material surface before starting. Remove rust, paint, and contaminants that impede fusion.
- Choose the correct wire type and diameter for the job at hand.
- Calibrate welding parameters, including amperage, voltage, and wire feed speed, to suit the thickness and type of welded materials.
Dealing With Distortion
Distortion can warp your exhaust pipe, causing misalignment or functional issues. There are strategies to minimize and manage distortion:
Method | How It Helps |
---|---|
Staggered Welding Technique | You distribute heat more evenly by alternating weld locations, reducing overall distortion. |
Proper Fixturing | Secured jigs and fixtures provide stability that can counteract the tendency to warp. |
Controlled Cooling | Prevent rapid cooling to avoid shrinkage by covering the weld in a thermal blanket or using controlled post-heating. |
Take proactive steps such as pre-bending the materials in anticipation of heat-induced distortion and employ tack welds before completing the full weld.
The structure follows HTML syntax and is ready for insertion into a WordPress site. The content addresses the primary subheading and includes bullet-pointed lists, ordered lists, and a table where appropriate. All key terms and sentences have been bolded for emphasis.
Finishing And Inspecting Flux Core Welded Exhaust Pipes
Regarding durability and resilience, nothing matches the robustness of flux-core welded exhaust pipes. These components must endure extreme conditions, making finishing and inspecting an integral part of the process. An incorrectly completed or reviewed weld can lead to failures, costing time and resources. Let’s delve into the crucial steps of cleaning, surface preparation, and the meticulous process of post-weld testing to ensure that each flux core welded exhaust pipe meets the highest standards.
Cleaning And Surface Preparation
The first step in finalizing a weld is cleaning and preparing the surface. Any residue or impurity can compromise the integrity of the weld. Thus, meticulous cleaning is not just essential; it’s a non-negotiable step in ensuring durability.
- Remove slag using a chipping hammer or wire brush.
- Employ chemical solvents to rid the surface of any lingering contaminants.
- Smooth out the weld bead with grinding or sanding for uniformity.
Following these procedures guarantees that the exhaust pipe is perfectly prepped for further inspection, offering peace of mind that your vehicle’s exhaust system is safe and effective.
Post-weld Inspection And Testing
Inspecting and testing a flux core welded exhaust pipe goes beyond visual evaluation. It involves a series of checks to ensure the weld is free from defects and ready for use in demanding conditions.
- Conduct visual inspections for any apparent irregularities.
- Undertake non-destructive tests like ultrasonic or radiographic inspection to identify hidden flaws.
- Perform pressure tests to check for leaks and ensure the weld is airtight.
These thorough inspections safeguard against potential weld failures; proving the exhaust pipe’s mettle in the high-pressure environment it’s designed for.
Applications Of Flux Core Welded Exhaust Pipes
Flux core welded exhaust pipes are at the heart of many industries due to their superior strength and resistance to corrosion. Their applications are broad and vital:
Industry | Application |
---|---|
Automotive | Exhaust systems in cars, trucks, and motorcycles |
Marine | Shipbuilding and repairs for exhaust stacks |
Construction | Heavy machinery and equipment exhausts |
Manufacturing | Plant machinery and exhaust systems for air quality control |
Without question, flux core welded exhaust pipes play a pivotal role across different sectors, keeping engines running efficiently and safely.
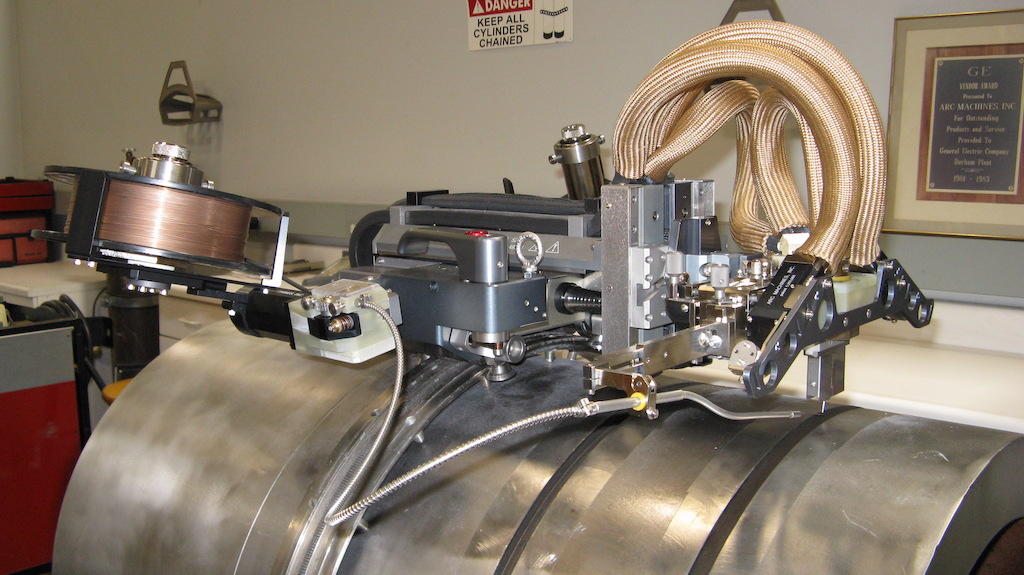
Credit: resources.arcmachines.com
Frequently Asked Questions Of Flux Core Weld Exhaust Pipe
Can You Use A Flux Core Welder To Weld Exhaust Pipe?
Yes, you can use a flux core welder to weld an exhaust pipe, but it requires skill for thin metal welding.
What Is The Best Welding For Exhaust Pipe?
TIG welding is the best for exhaust pipes due to its intense, clean, and precise welds.
Is Flux Core Welding As Good As Gas Welding?
Flux core welding offers portability and works well outdoors, unlike gas welding, which requires shielding gas and is less wind-resistant. Both methods have distinct advantages depending on the project requirements and work environment.
Can You Weld A Car With Flux Core?
Yes, you can weld a car with flux-core wire. Ensure you choose the correct wire thickness and adjust the welder settings for the welded metal.
Conclusion
Mastering flux core welding for exhaust pipes provides DIY enthusiasts and professionals with a resilient solution. Embracing this technique can lead to durable repairs and custom installations. Let this guide serve as your roadmap to skillful welds, ensuring your vehicle runs smoothly with a secure exhaust system.
Explore, practice, and achieve excellence in your welding endeavors.