A full penetration weld fuses the entire section thicknesses of the joined materials, whereas a fillet weld joins two surfaces at a right angle without full penetration. Full penetration welds are typically used for their superior strength, providing continuity across the entire joint, while fillet welds are more common due to their simplicity and cost-effectiveness.
Both full penetration and fillet welds are fundamental techniques in the welding process with distinct applications and strengths. Full penetration welds require precise preparation, including beveling the edges and controlling heat input to achieve the desired weld depth. They are crucial in high-stress applications where structural integrity is paramount.
On the other hand, fillet welds are employed in various constructions due to their versatility and ease of application. They can be performed quickly, making them advantageous for projects with time constraints or for joining components that can’t tolerate the high heat of full penetration welding. Understanding the differences between these two weld types is essential for any project requiring metal joining, as the choice directly impacts the final product’s strength, quality, and safety.

Credit: fsmdirect.com
Definition Of Full Penetration Weld
Full penetration welds involve the melting and fusion of the base materials throughout the entire thickness. This type of weld creates a strong bond. It intersects the entire thickness of the components joined. It is critical in applications where strength is paramount.
How It Is Achieved
Achieving a full penetration weld requires precision and technique. Skilled welders use methods such as:
- Groove welds – where a channel is formed between two materials.
- Beveling edges – which prepares the materials for deeper welds.
- Application of heat control for material flow.
Proper joint preparation, welding sequence, and heat input control are essential.
Benefits
Full penetration welds offer numerous benefits:
Benefit | Description |
---|---|
High Strength | A seamless bond along the entire material thickness ensures optimal strength. |
Durability | These welds withstand higher stresses and last longer. |
Reliable | Consistent quality and reliability in high-pressure applications. |
They are ideal for structures requiring maximum weld penetration and integrity.
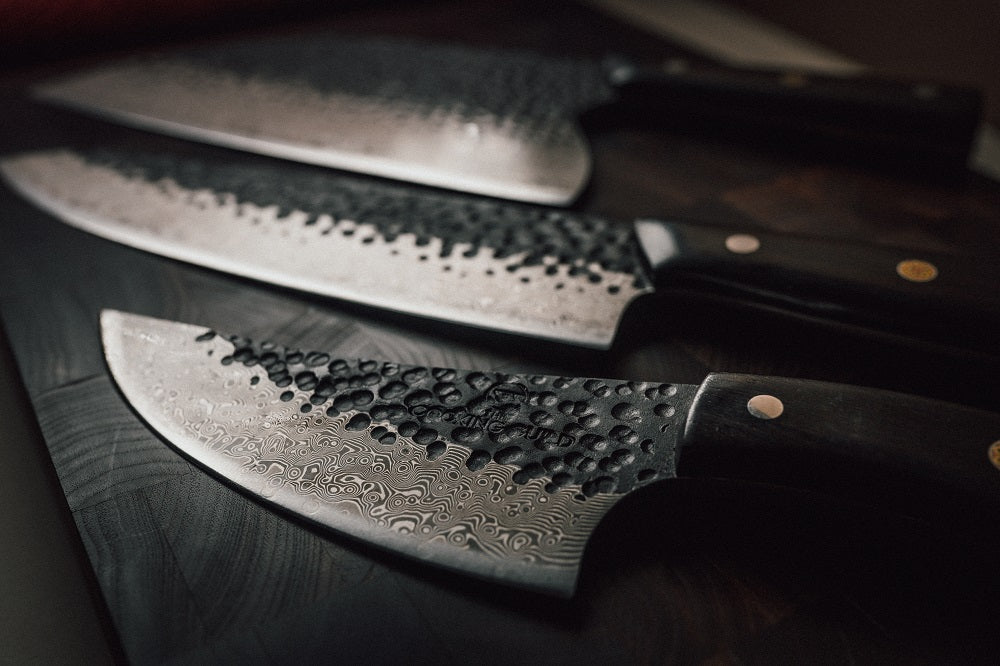
Credit: www.thecookingguild.com
Definition Of Fillet Weld
A fillet weld joins two pieces of metal at a right angle. It is the most common type of weld used in fabrication. Picture the corner of a picture frame, where the two sides meet. That’s where you would see a fillet weld. Experts mold the weld metal into a triangular shape to keep the pieces together.
How It Is Achieved
Creating a fillet weld involves skill and precision. First, a welder cleans the metal surfaces. Then, they choose the right electrode and set their welding machine to the correct settings.
- Set at the right angle: The tool must be held at a 45-degree angle to the pieces.
- Steady hand motion: As the welder moves along, the filler metal fuses the pieces.
- Cooling: After the weld passes, the metal must cool slowly, forming solid connections.
Benefits
Fillet welds have important advantages. They are not only easy to perform but also save time and materials.
- No need for edge preparation: The pieces can be welded without shaping the edges first, unlike other weld types.
- Efficient: Fillet welds use less filler material, making them cost-effective.
- Versatile: They are suitable for different projects, big or small.
Key Differences Between Full Penetration Weld And Fillet Weld
The choice between full penetration welds and fillet welds can greatly impact the strength, efficiency, and cost of your project. Understanding the distinct differences between these two common welding techniques is crucial for any construction or manufacturing endeavor. Let’s explore the key factors distinguishing full penetration and fillet welds.
Joint Design
Full penetration welds involve melting and fusing materials along the entire cross-section of the joint, resulting in a single piece of metal. These welds are often designed for critical structures where joint integrity is of utmost importance. Fillet welds, on the other hand, connect two pieces at right angles without requiring the complete fusing of the base materials. This results in a triangular-shaped weld along the outside of the joint.
Material Thickness
Thicker materials tend to require full penetration welds to ensure a bond throughout the entire material. Fillet welds are more suited for thinner or non-critical materials where full penetration is not necessary for the integrity or function of the joint.
Strength And Load Capacity
Considering strength and load capacity, full penetration welds offer higher strength than fillet welds. They are preferred in high-stress applications because they bear loads from all directions uniformly. Fillet welds are adequate for less demanding scenarios where full strength is not required.
Cost And Time
In terms of cost and time, fillet welds typically require less preparation and are faster to execute, thus being more cost-effective for non-critical applications. Full penetration welds demand precise preparation, often including beveling the edges of the material and increased welding time, which can drive up costs.
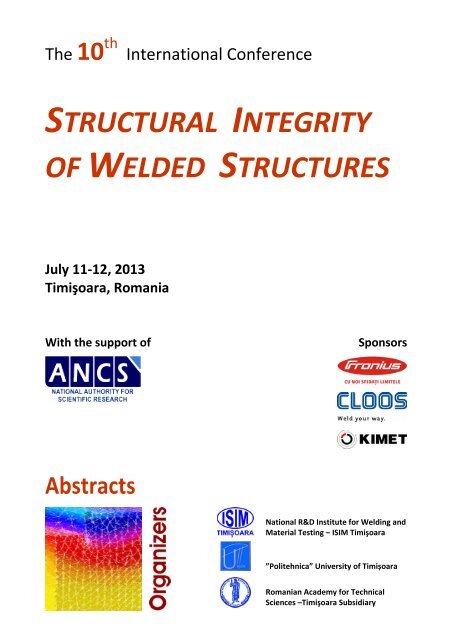
Credit: www.yumpu.com
Applications And Usage Scenarios
Applications and Usage Scenarios affect the choice between Full Penetration and Fillet Welds. These welding techniques have distinct characteristics. These differences suit different needs in construction and manufacturing. Let’s dive into where each weld type shines.
Full Penetration Weld
A Full Penetration Weld melts and fuses material all the way through the workpiece. This creates a single piece of metal. Here’s when to use them:
- Structural Steelwork: Buildings and bridges rely on these welds for a strong bond.
- High-Pressure Pipelines: Gas and oil pipelines need full strength to prevent leaks.
- Heavy Equipment Manufacturing: Full penetration ensures machinery can handle stress.
These scenarios demand welds that can bear heavy loads. They also require endurance against fatigue and fractures.
Fillet Weld
Fillet Welds bond two surfaces at a right angle. They are quicker to make. Here’s where they are used:
- Light to Medium Construction: Smaller structures like workbenches use fillet welds.
- Home Projects: DIY metal crafts and furniture often need fillet welds.
- Automotive Fabrication: Cars and trucks parts are joined using fillet welds.
These scenarios are perfect for fillet welds. They offer balance between strength and speed of application.
Choosing The Right Type Of Weld
Full Penetration Welds and Fillet Welds are critical techniques in the world of welding. Each has its own set of characteristics and uses. Knowing which weld to choose can make a huge difference in the strength and quality of your project. Let’s delve deeper into the factors to consider for each type of weld.
Considerations For Full Penetration Weld
- Strength Needs: Full penetration welds provide superior strength.
- Project Requirements: Often specified for critical joints.
- Material Thickness: Ideal for thicker materials needing sturdy joints.
- Inspection and Testing: Required for full penetration to ensure quality.
These welds are costlier due to higher material and labor requirements.
Considerations For Fillet Weld
- Simplicity: Fillet welds are easier to perform.
- Speed: These welds are quicker to execute.
- Cost-Effectiveness: Less labor and material usage save costs.
- Applicability: Best for non-critical joints and lighter materials.
Choose fillet welds for projects where strength is less of a concern.
Frequently Asked Questions On Full Penetration Weld Vs Fillet Weld
What Is Full Penetration Weld?
A full penetration weld completely fuses two materials by filling the entire joint thickness, ensuring maximum strength.
Which Type Of Welding Has The Best Penetration?
Stick welding, also known as Shielded Metal Arc Welding (SMAW), typically offers the deepest penetration for welding thick sections.
What Is The Strongest Weld Pattern?
The strongest weld pattern is often considered to be the multipass weave bead, which provides excellent penetration and strength.
Why Fillet Welds Are Preferred?
Fillet welds are preferred for their ease of execution, versatility in joining different shapes, and efficient material usage. They require less preparation and are generally more cost-effective than other types of welds.
Conclusion
Deciding between full penetration welds and fillet welds is crucial for project success. Both have distinct advantages tailored to specific needs. Factor in strength, application, and cost before choosing. Embrace the right weld type and ensure structural integrity and durability.
Always prioritize your project’s unique requirements for optimal outcomes.