To weld brass, use appropriate filler material and employ TIG or MIG welding techniques. Preheat the brass to prevent cracking and ensure thorough cleaning before starting.
Welding brass, an alloy predominantly of copper and zinc, requires precise skill due to the metal’s sensitivity to heat and its low melting point of zinc. The process demands a clean surface and proper ventilation due to the fumes emitted during welding.
Mastery of TIG (Tungsten Inert Gas) or MIG (Metal Inert Gas) welding is essential for achieving strong, high-quality joins in brass. These methods provide the control needed to manage the heat input and to work around the zinc’s tendency to vaporize at high temperatures. Preheating the brass can help mitigate some of the challenges presented by the differing melting points of copper and zinc within the alloy. Ensuring proper safety measures, like wearing a respirator, is paramount due to the metallic fumes produced during the welding process. For those in Austin, Texas seeking to perform brass welding tasks, understanding these specific techniques and precautions is key to a successful outcome.
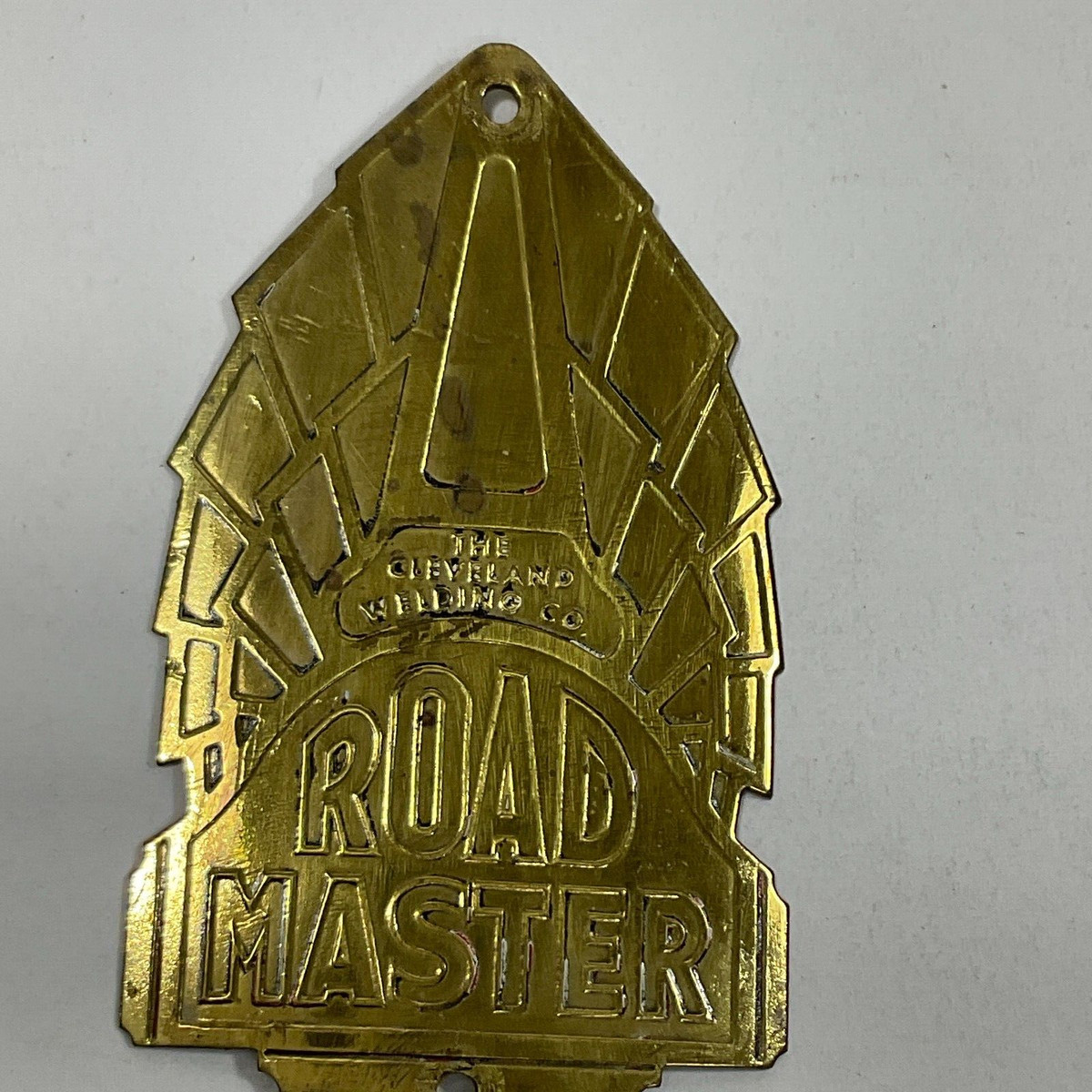
Credit: www.ebay.com
Safety Precautions
Before diving into the intricacies of welding brass, it’s crucial to prioritize safety. Welding, by its nature, can be hazardous. Brass welding, in particular, requires additional precautions. It involves intense heat, harmful fumes, and bright arc light. Safeguarding against risks ensures a successful and unharmed experience.
Protective Gear
Wearing proper protective gear is non-negotiable. To shield yourself from sparks, spatter, and intense light, the right equipment is necessary. Here are essential items:
- Auto-darkening welding helmet – Protects eyes from arc flash.
- Fire-resistant welding jacket – Prevents burns from hot brass.
- Thick gloves – Keeps hands safe from heat.
- Respirator mask – Filters out fumes, especially zinc oxide.
- Leather apron – Adds an extra layer of protection.
- Safety glasses – Must be worn under the helmet for additional eye safety.
- Ear protection – Dampens noise from welding machines.
Workspace Safety
Setting up a safe workspace is as important as wearing the right gear. Follow these guidelines:
- Ensure good ventilation to avoid inhaling harmful fumes.
- Keep a fire extinguisher nearby in case of an accidental fire.
- Remove flammable materials from the welding area.
- Display safety signage for others to be aware of the welding activities.
- Have first-aid equipment accessible for immediate response to potential injuries.
- Use a welding screen to protect bystanders from arc flash.
- Maintain neat workspace to prevent accidents caused by clutter.
Maintaining safety standards while welding brass keeps you and your surroundings secure. Tailor your workspace and personal gear to handle the demands of the task. From the intense heat to the bright light and toxic fumes – prevention is key. Always operate with acquired training, and if unsure, seek guidance from experienced welders. Let safety empower your work, not hinder it.
Preparing For Brass Welding
Begin SEO tagsEnd SEO tags
Welding brass can seem daunting due to the different melting points of its copper and zinc components. Proper preparation ensures a strong, clean weld. Master these preparations, and you’ll be equipped to start welding brass with confidence.
Cleaning the brass surfacesCleaning The Brass Surfaces
Clean brass surfaces prevent weld defects. The cleaning process involves several steps:
- Remove grease with a solvent like acetone.
- Brush off surface oxidation with a wire brush.
- Wipe down with a clean cloth to eliminate residues.
Always wear gloves to stop oils from your hands transferring to the brass.
Choosing the right filler materialChoosing The Right Filler Material
Selecting the ideal filler material is critical:
Filler Type | Features | Applications |
---|---|---|
Silicon Bronze | High strength, corrosion resistance | Suitable for thin brass sheets |
Manganese Bronze | Good mechanical properties | Recommended for castings |
Match the filler to the brass alloy for optimal results.
Welding Techniques
Welding brass involves techniques ensuring a strong bond and clean finish. Whether for art, repairs, or construction, understanding the proper approach is key. Explore the common methods of welding and when to use them here.
Tig Welding
Tungsten Inert Gas (TIG) welding, also known as GTAW, is renowned for its precision and clean results. It is often the preferred method for welding brass due to the metal’s melting characteristics. Follow these steps:
- Clean the brass thoroughly before starting.
- Choose a filler material compatible with brass.
- Ensure the welding environment is well-ventilated.
Mig Welding
Metal Inert Gas (MIG) welding is less common for brass but possible with the right settings. While it’s faster than TIG, it might not provide the same finish. Consider these points:
- Select the right brass-compatible wire.
- Set the welder to the correct power settings for brass.
- Use a short-circuit transfer type to handle the brass’s lower melting point.
Oxyacetylene Welding
Oxyacetylene welding is a traditional process suitable for brass. It requires a steady hand and close attention to temperature. Here’s how to do it:
- Adjust the flame to a neutral setting to avoid oxidizing the brass.
- Use a flux to prevent oxidation and improve flow.
- Heat both pieces evenly for a consistent weld pool.
Credit: www.linkedin.com
Troubleshooting Brass Welding Issues
Mastering brass welding is challenging. This section guides you through common pitfalls. Learn the savvy tips and tricks to conquer brass welding defects.
Common problems and their solutionsCommon Problems And Their Solutions
Brass welding often presents unique hurdles. Identifying and resolving these can make all the difference. Here’s a rundown of frequent issues and how to fix them:
Table of common issuesProblem | Solution |
---|---|
Porosity | Ensure clean surfaces. Use the right flux to prevent gas pockets. |
Warping | Avoid excessive heat. Weld in short intervals. |
Cracks | Preheat the brass. Use a lower welding temperature. |
Melting of Zinc | Control the heat input. Zinc burns off at lower temps. |
Tips For Avoiding Welding Defects
- Always clean the brass thoroughly before welding to avoid impurities.
- Select the appropriate filler material for a stronger bond.
- Control your welding speed and temperature to prevent overheating.
- Utilize proper ventilation to handle fumes from zinc evaporation.
- Practice your technique on scrap pieces first to gain confidence.
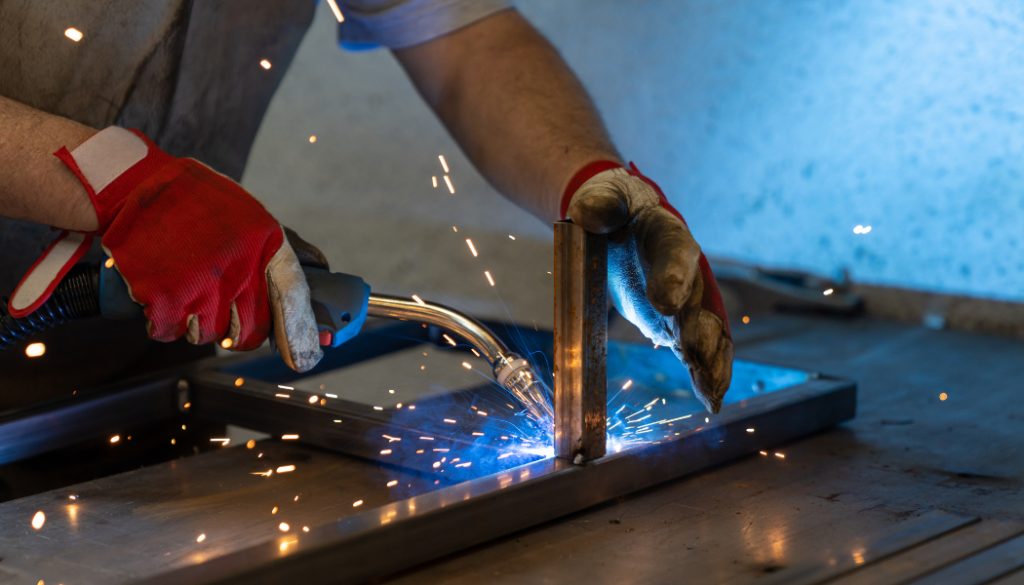
Credit: xpressmobilewelding.com
Frequently Asked Questions On How To Weld Brass
Is It Difficult To Weld Brass?
Welding brass can be challenging due to differing melting points of copper and zinc. Use appropriate techniques like TIG or MIG welding with careful heat control.
How Do You Join Two Pieces Of Brass Together?
To join two pieces of brass together, you can either solder, weld using TIG or MIG methods, or braze them.
Can I Weld Brass With A Mig Welder?
Yes, you can weld brass using a MIG welder by employing proper techniques and filler material designed for brass.
Do You Weld Or Solder Brass?
Yes, you can weld or solder brass using techniques like TIG, MIG welding, or soldering, depending on the project’s requirements.
Conclusion
Mastering brass welding can unlock numerous metalworking opportunities. To nail this skill, patience and practice are key. Remember the nuances: brass’s varying zinc content, the importance of proper heat management, and safety measures like ventilation. By keeping these factors in mind, your welded brass projects should turn out strong, durable, and aesthetically pleasing.
Time to spark up the torch and create with confidence!