Welding an exhaust pipe with a stick requires a clean surface and proper clamp setup. Use a small diameter rod and maintain a tight arc to avoid burn-through.
Welding an exhaust pipe can be a daunting task, but with the right tools and technique, it’s a skill that can be mastered by DIY enthusiasts and professional welders alike. This process involves using a stick welder, also known as shielded metal arc welding (SMAW), to join exhaust pipes efficiently.
Before beginning, it’s crucial to choose an electrode that’s compatible with the metal of the exhaust and to prepare the pipe by cleaning it thoroughly. Stick welding provides a strong, durable bond that’s ideal for the high-temperature environment of exhaust systems. Patience and practice are key, as the thin metal of exhaust pipes can pose a challenge, necessitating a steady hand and precise control of the welding equipment.
Credit: m.facebook.com
Preparing For Welding
Welding exhaust pipes is a task that demands precision and care. Before diving into the nitty-gritty of stick welding, ensuring you are fully prepared is crucial. Preparation involves two key aspects: collecting the right tools and addressing safety concerns.
Gathering The Necessary Tools
Effective preparation begins with having all the essential tools on hand. Here’s what you’ll need:
- Stick Welder: Suited for the job at hand.
- Welding Rods: Appropriate for the exhaust material.
- Angle Grinder: For cleaning and smoothing edges.
- Wire Brush: For removing debris and dirt.
- Clamps: To hold the pipes in place.
Ensuring Proper Safety Measures
Safety is paramount. Always make sure you’re properly equipped with:
- Welding Helmet: To protect your eyes and face.
- Welding Gloves: To guard your hands from sparks and heat.
- Protective Clothing: To shield your skin from burns.
- Fire-Resistant Blanket: To prevent fires.
- Ventilation: Ensure the area is well-ventilated.
Choosing The Right Electrode
When welding an exhaust pipe with stick, the electrode can make or break your weld. The electrode is your conduit for the electric current that heats and melts the metal, allowing you to fuse parts together. It’s crucial to select the right one for a strong, durable bond. Let’s dive into what you need to know to make the perfect choice for your exhaust pipe project.
Understanding Electrode Types
Electrodes come in various types, each suited for different jobs. For exhaust pipe welding, you want something that can withstand high temperatures and resist corrosion. Here’s what to look for:
- E6011: This electrode works well on rusty metals, making it a good choice for older exhaust systems.
- E6013: It offers a smooth weld and works on all positions, great for hard-to-reach spots.
- E7018: Known for creating strong welds, it’s ideal for thicker exhaust pipes that need extra strength.
Determining Electrode Thickness
Choosing the right electrode thickness is important for a successful stick weld. Too thick and you might burn through the pipe, too thin and the weld won’t hold. It usually matches the metal you’re welding.
Metal Thickness | Electrode Thickness |
---|---|
<1/8″ (3.2mm) | 1/16″ (1.6mm) |
1/8″ (3.2mm) | 1/8″ (3.2mm) |
>1/8″ (3.2mm) | 5/32″ (4.0mm) |
Match the electrode thickness to your exhaust pipe’s gauge. Use the guide above to find your ideal electrode size.
Preparing The Exhaust Pipe
Preparing the exhaust pipe properly is key.
Let’s dive into the crucial steps to get it ready.
Cleaning The Surface
To ensure a strong weld, start with a clean surface.
- Wipe the pipe with a degreaser.
- Use a cloth to remove any grease or oil.
- Dry the area completely before proceeding.
Removing Rust And Corrosion
Next, tackle rust and corrosion.
- Inspect the exhaust pipe closely.
- Identify any spots with rust.
Use a wire brush or sandpaper to:
- Scrub off the rust.
- Smooth the metal surface.
- Clean the area again after removing rust.
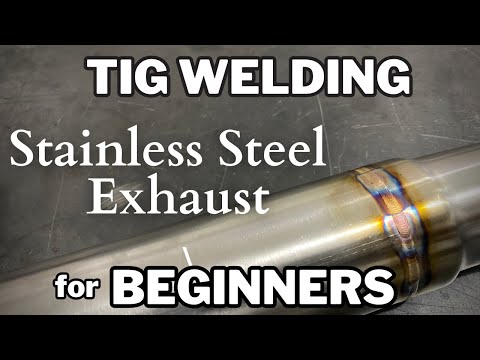
Credit: m.youtube.com
Setting Up The Welding Equipment
Before diving into the world of welding exhaust pipes, a proper setup of equipment is crucial. Setting up the welding equipment with precision ensures a strong, durable weld. Let’s explore the steps to prepare the stick welding equipment for your exhaust pipe project.
Setting the AmperageSetting The Amperage
Selecting the right amperage is key for a successful weld. The amperage controls the heat of the welding arc. It varies based on:
- The thickness of the exhaust pipe
- The type of metal in the pipe
- The electrode size
For thinner metals, like exhaust pipes, start with a lower amperage and adjust as needed.
Use this table as a guide:
Electrode Diameter (in) | Amperage Range |
---|---|
1/16 | 20 – 40 A |
5/64 | 40 – 80 A |
3/32 | 60 – 100 A |
Adjusting The Arc Length
The arc length, or the distance between the electrode and the metal, influences weld quality. A short arc length increases the heat, penetration, and potential for better control. On the other hand, a long arc length can lead to spatter and a weaker weld.
- Position the electrode close to the workpiece.
- Aim for an arc length equal to the diameter of the electrode’s core.
- Adjust your hand to maintain the arc length as the electrode melts.
Executing The Welding Process
When it comes to welding an exhaust pipe with a stick welder, precision and the right technique are crucial. This section of our blog post guides you through executing the welding process. Our focus will be on two key steps: starting the arc and applying the welding beads.
Starting The Arc
Initiating the arc is the first step in stick welding an exhaust pipe. Ensure your welding machine is set to the correct amperage for the thickness of the pipe. Follow these steps:
- Secure the exhaust pipe in place with clamps to prevent movement.
- Put on your safety gear, including helmet, gloves, and protective clothing.
- Strike the electrode like a match against the pipe to start the arc.
- Maintain a short arc length, slightly lifting the electrode if sticking occurs.
Applying The Welding Beads
After starting the arc, the next step is to apply the welding beads. Proper bead application ensures a strong, leak-free joint. Here’s how to do it right:
- Maintain a consistent speed and motion to produce even welds.
- Use a back and forth or circular motion as you move along the joint.
- Focus on keeping the electrode angle consistent throughout the process.
Remember to let the welded area cool down before inspecting your work. Aim for smooth, even beads without gaps or bulges for optimal exhaust function.

Credit: conwhole.en.made-in-china.com
Frequently Asked Questions For How To Weld Exhaust Pipe With Stick
Can You Use A Stick Welder To Weld Exhaust Pipe?
Yes, you can use a stick welder to weld an exhaust pipe, but it requires skill for thin metal. Opt for small diameter rods and lower amperage to prevent burn-through.
What Kind Of Rod To Use To Weld Exhaust Pipe?
For welding exhaust pipes, use a mild steel rod, such as the E308L rod for stainless steel exhausts, to ensure a durable and lasting join.
Can You Weld Pipe With Stick?
Yes, you can weld pipes with stick welding (Shielded Metal Arc Welding or SMAW), which is suitable for various pipe materials and thicknesses. Stick welding offers versatility and portability, ideal for both indoor and outdoor pipe joining tasks.
What Is The Best Welding Method For Exhaust Pipe?
The best welding method for exhaust pipes is TIG (Tungsten Inert Gas) welding, due to its precision and strong, clean welds.
Conclusion
Mastering the art of stick welding exhaust pipes takes practice but is achievable. Utilize the right tools and follow safety guidelines. Your efforts will ensure strong, durable welds for your exhaust system. Keep honing your skills for excellent results in all your welding projects.
Happy welding!