The strength of arc welding compared to MIG welding depends on the application. While both can create strong welds, material type and project conditions often dictate the best method.
Arc welding, also known as shielded metal arc welding (SMAW), is a traditional and versatile welding process well-suited for various metals and thicknesses. It uses a consumable electrode coated in flux to lay the weld. MIG welding, or metal inert gas welding, is a more modern technique that employs a wire feeding system, making it faster and cleaner than arc welding.
Both methods are strong when properly applied, but their effectiveness can differ based on the materials involved, the skill of the welder, and the specific requirements of the job at hand. Professionals choose the welding technique that best matches the task, ensuring the integrity and strength of the final weldment. Whether working on home repairs, industrial fabrication, or automotive assembly, understanding the particular strengths of arc and MIG welding is essential for achieving durable and reliable results.
Credit: www.linkedin.com
Understanding Arc Welding
Exploring the world of welding, specifically arc welding, reveals a realm where metals fuse with might. This method stands as the backbone of several industries. Here’s a closer look at what makes arc welding unique and strong.
Definition And Process
Arc welding refers to joining metals by heating them with an electric arc. This fusion method involves an electrode and high-intensity heat.
- Preparation includes cleaning the metal surfaces.
- The electrode, either consumable or non-consumable, is indispensable.
- Electric current types include alternating (AC) or direct (DC).
- Heat from the arc melts the metal, allowing bonding.
Strength And Applications
Arc welding boasts considerable strength, essential for construction and repair. This strength arises from the deep penetration of heat, creating durable joints.
Industry | Application |
---|---|
Automotive | Chassis and frame repair |
Construction | Structural components bonding |
Manufacturing | Heavy machinery assembly |
The process caters to various metals like steel, iron, and aluminum. Custom projects and large-scale constructions frequently rely on this welding style.

Credit: www.amazon.com
Understanding Mig Welding
MIG welding stands for Metal Inert Gas welding. It’s popular for its simplicity and speed. Many industries use MIG welding due to its strong joins and efficiency. Let’s dive into what MIG welding is and how it compares in strength and applications.
Definition And Process
MIG welding, also known as Gas Metal Arc Welding (GMAW), uses a continuous solid wire electrode. This wire heats up and melts to form a weld. Electrical current is applied, which joins two pieces of metal together as the wire melts. Shielding gas flows through the welding gun. It protects the weld from air contamination.
Step | Action |
---|---|
1 | Prepare the equipment and metal |
2 | Setup the MIG welding machine |
3 | Turn on the power and shielding gas |
4 | Begin the welding process |
Strength And Applications
MIG welding creates very strong joints, often stronger than the materials being joined. Factors influencing strength include the heat input, the wire type, and mastering techniques. Due to its versatility, MIG is suitable for various applications.
- Automotive repair and customization
- Construction of metal structures
- Creating art and metal sculptures
- Fabricating metal furniture
Industries favor MIG welding for its adaptability to different metals, including stainless steel, aluminum, and carbon steel. The process is preferable for both thin and thick materials.
Comparing Strength
When choosing a welding process, strength is a key factor. Both Arc Welding and MIG (Metal Inert Gas) Welding create strong joints, but which one comes out on top? Understanding the strength of welds helps in selecting the right method for your project. Let’s compare the strength of Arc Welding to MIG Welding.
Factors Affecting Strength
The strength of a weld can be influenced by many aspects:
- Material Thickness: Thicker materials require more penetrating welds.
- Welding Current: Higher currents can increase weld penetration and strength.
- Filler Material: The strength of the filler metal can affect the weld’s overall strength.
- Welding Speed: Faster speeds can produce weaker welds due to less heat input.
- Technique: Proper technique is crucial for creating a strong weld.
Weld Strength Comparison
Comparing the strengths of Arc Welding to MIG Welding shows some differences:
Welding Process | Characteristics | Strength |
---|---|---|
Arc Welding | Deep penetration, can handle rust and dirt | Strong in thick and heavy-duty applications |
MIG Welding | Consistent, clean welds | Good for thin materials, strong if clean |
Arc Welding is generally stronger in situations where deep penetration is needed, such as with thicker materials. On the other hand, MIG Welding may provide sufficient strength for thin materials and can be optimal when a clean, consistent weld is necessary.
Considering Other Factors
When considering the strengths of arc welding versus MIG welding, it’s crucial to look beyond just the bond. Factors such as cost, ease of use, and weld quality and versatility are important. Let’s dive into these aspects to see how they influence your choice.
Cost And Ease Of Use
Cost-effectiveness and user-friendliness are key in welding. Here’s a breakdown:
- Arc Welding: Typically lower in cost due to simpler equipment.
- MIG Welding: Often has higher initial costs but could lead to savings over time with faster operation.
As for ease of use, MIG welding is generally more user-friendly, especially for beginners. Setup is simpler and it requires less skill to achieve clean welds. Arc welding, on the other hand, demands a solid technique but offers more control in skilled hands.
Weld Quality And Versatility
Weld integrity and the ability to adapt to various situations are paramount. Let’s explore:
Aspect | Arc Welding | MIG Welding |
---|---|---|
Weld Strength | Offers deep penetration for stronger bonds in thicker materials. | Provides consistent, high-quality welds with less penetration. |
Versatility | Excels outdoors and with rusty or painted metals. | Better for thinner materials and can be used with a variety of metals. |
While MIG welding affords greater flexibility in applications, arc welding wins in challenging environments where equipment ruggedness is essential. Both methods cater to specific needs and scenarios in the realm of welding.
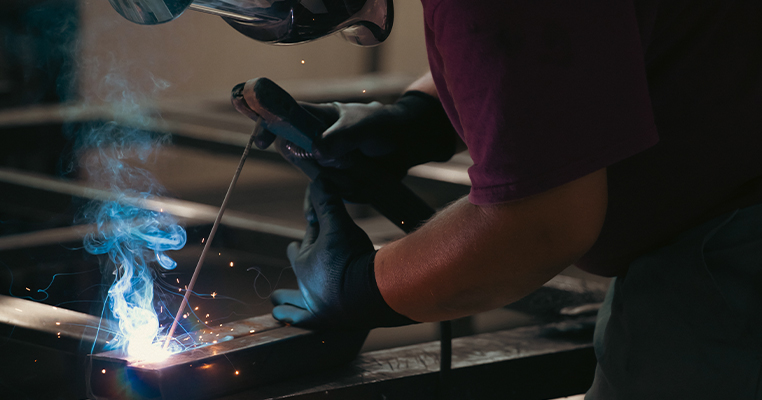
Credit: blog.red-d-arc.com
Frequently Asked Questions On Is Arc Welding Stronger Than Mig
Which Is Stronger Mig Welding Or Arc Welding?
MIG welding typically offers stronger welds than arc welding due to its use of shielding gas and continuous wire feed.
What Is The Strongest Type Of Welding?
The strongest type of welding is Tungsten Inert Gas (TIG) welding, known for producing high-quality, precise, and strong welds.
Is A Mig Or Arc Welder Better For Beginners?
A MIG welder is typically better for beginners due to its ease of use and versatility in various welding applications.
What Is An Arc Welder Best For?
An arc welder is best for joining metal components through high-heat welding processes, suitable for heavy-duty tasks and industrial applications.
Conclusion
Selecting between arc welding and MIG welding hinges on your project’s requirements. Arc welding excels in outdoor adaptability and thick materials. Conversely, MIG welding offers precision and speed for thinner metals and continuous welds. Ultimately, understanding each method’s strengths ensures the right choice for durable, effective joints.
Choose wisely for success in your welding endeavors.