Tungsten carbide is a compound containing equal parts tungsten and carbon. Pure tungsten is a single element with different properties from its carbide counterpart.
Tungsten carbide and tungsten are two materials widely utilized for their unique characteristics in various industries. Tungsten carbide stands out for its extreme hardness and wear resistance, making it ideal for cutting tools, abrasives, and various industrial applications requiring durability.
On the other hand, tungsten’s high melting point and tensile strength make it perfect for applications that demand high heat resistance, such as in electrical and military sectors. Choosing between these materials depends on the specific requirements of the task at hand, taking into account factors like toughness, durability, and resistance to heat and corrosion. Understanding the differences is essential for engineers, manufacturers, and consumers looking to make informed decisions for their specific needs.
Composition
Understanding the building blocks of materials is essential when comparing them. The composition of a substance dictates its properties, uses, and strength. Let’s dive into the world of Tungsten Carbide and Tungsten to uncover the secrets held in their structures.
Tungsten Carbide CompositionTungsten Carbide Composition
Tungsten Carbide stands out with a unique mix of elements. It’s a compound, not a pure element. The substance forms when tungsten and carbon come together. Think of it as a team-up, where each brings its best traits to create something stronger. Here’s a look at its composition:
- Carbon atoms join forces with tungsten particles.
- The ratio is one part carbon to one part tungsten.
- This blend forms a crystal lattice structure.
- The result? An incredibly hard material.
It’s the go-to for the toughest jobs. Dental tools and cutting equipment often use it.
Tungsten CompositionTungsten Composition
Pure Tungsten is an element. It claims spot number 74 on the periodic table. Its composition is simpler than Tungsten Carbide’s because it’s a solo act—it’s all tungsten. Here’s what you need to know about its makeup:
- It’s just tungsten—a single element with no mix.
- A high melting point makes it stand strong against heat.
- It’s very dense, denser than lead even.
Its purity makes it ideal for things like light bulb filaments and even rocket engine nozzles.
Properties
Exploring the core properties of two extraordinary materials, Tungsten Carbide and Tungsten, reveals how each stands out in various applications. Let’s dive into their individual characteristics and see how they stack up in terms of physical and mechanical properties.
Physical Properties
Tungsten, known for its remarkable robustness, has the highest melting point of all metals at 3,422°C. Tungsten Carbide also impresses with a melting point nearing 2,870°C, though not as high as pure Tungsten. Both materials exhibit high density, with Tungsten being incredibly heavy at 19.25 g/cm³, and Tungsten Carbide follows closely at about 15.63 g/cm³.
Color is another distinct aspect; pure Tungsten boasts a shiny, gray steel-like appearance, while Tungsten Carbide offers a richer, darker complexion. When considering electrical and thermal conductivity, Tungsten outperforms many metals, and although Tungsten Carbide is less conductive, it still maintains efficient thermal properties.
Property | Tungsten | Tungsten Carbide |
---|---|---|
Melting Point | 3,422°C | 2,870°C |
Density | 19.25 g/cm³ | 15.63 g/cm³ |
Appearance | Shiny Gray | Dark Gray |
Conductivity | High | Moderate |
Mechanical Properties
The spotlight shifts to hardness and durability features. Tungsten Carbide dominates with an impressive score of around 9 on the Mohs hardness scale, bested only by diamonds. This quality makes it exceptionally wear-resistant and capable of enduring high-pressure environments.
- Tungsten Carbide’s rigidity disciplines even the toughest applications.
- Tungsten maintains admirable scratch resistance, ideal for jewelry or industrial use.
Tensile strength is another arena where these materials shine. Tungsten’s is an astounding 1510 MPa, while Tungsten Carbide’s composite nature offers variations depending on the grain size and cobalt content, often exceeding 3447 MPa. Yet, Tungsten is more ductile in its pure form, making it slightly more pliable under stress than Tungsten Carbide.
- Tough environments demand Tungsten Carbide’s endurance.
- Tungsten’s flexibility under strain is beneficial for specific uses.
Applications
The world of tools and materials is rich with options like Tungsten Carbide and Tungsten. Known for their distinct properties, each serves unique applications. Exploring these applications reveals why these materials are indispensable in various industries.
Tungsten Carbide Applications
Tungsten Carbide stands out for its extreme hardness and durability.
- Cutting Tools: Drills, saws, and mills made of tungsten carbide cut through metal easily.
- Mining Machinery: It’s perfect for drill bits and cutting blades in tough mining conditions.
- Wear Parts: Industrial machinery benefits from its resistance to wear and tear.
- Jewelry: Rings and bracelets use tungsten carbide for a long-lasting shine.
- Sports Equipment: Some golf club heads are crafted for enhanced performance.
Tungsten Applications
Tungsten has a high melting point and density, fitting it for diverse uses.
Application | Description |
---|---|
Lighting | Filaments in bulbs produce bright light because of tungsten. |
Electronics | Used in phones and computers for its conductive properties. |
Aerospace | Rockets use tungsten for its weight and heat resistance. |
Medical Devices | X-ray machines rely on tungsten shields for safety. |
Alloys | Steel mixed with tungsten becomes much stronger. |
Credit: www.linkedin.com
Manufacturing Process
The manufacturing process of Tungsten Carbide and Tungsten showcases the stark differences between these two materials. Despite their shared element, Tungsten, their production journeys are unique. Dive into the intricate world of how these incredibly tough substances come to life within the industrial landscape.
Tungsten Carbide Production
Tungsten Carbide, known for its exceptional hardness, begins as tungsten ore. Through a series of crushing, milling, and purifying, the ore transforms into Tungsten Oxide (WO3). Carburization comes next; this is when carbon is added at high temperatures. The result? A fine powder that is the precursor to Tungsten Carbide.
The magic happens in a high-pressure furnace. Here, the powder is pressed into molds. These become the blanks for various tools and parts. Next comes sintering. This involves heating the blanks to a point where they bond without reaching a melt. Sintering is the key that unlocks the toughness and durability of Tungsten Carbide.
Shaping and finishing the sintered parts give them the final touch. Precision ensures each piece meets exacting specifications. The production of Tungsten Carbide culminates in robust components set for challenging environments.
Tungsten Production
The journey of pure Tungsten production is less complex but equally fascinating. It starts with the same Tungsten Oxide derived from ore. Unlike Tungsten Carbide, production here heads toward reduction.
Tungsten Oxide encounters hydrogen or carbon at high temperatures. This reduction process strip away the oxygen. What remains is pure Tungsten powder.
The powder then goes through pressing and sintering, similar to Tungsten Carbide. However, the desired result differs. With Tungsten, manufacturers aim for a dense, metal form. This forms the basis for filaments in lighting or electrical contacts.
Final steps for Tungsten involve re-heating and forming it into rods or wires. These are then drawn into the fine wires or shapes needed for their end use. The result is a metal ready to take on heat and electricity with impressive resilience.
Durability And Strength
Tungsten carbide and tungsten are renowned for their hardness and resilience. They bring exceptional durability and strength to various applications, particularly in jewelry and industrial uses. Let’s dive into what makes each material adapt so well to demanding environments.
Tungsten Carbide Durability
Tungsten carbide stands out as a robust material. It boasts a unique combination of tensile strength, rigidity, and resistance to wear and tear. This composite material is crafted by fusing tungsten with carbon atoms, resulting in a substance that’s hard as diamond.
- Resistance to Scratching: With a hardness rating close to that of a diamond, it resists scratches like no other.
- Impact Tolerance: High resilience means it maintains form, even under strong impacts.
- Longevity: It withstands years of use without losing its shine or becoming deformed.
Tungsten Durability
Pure tungsten also shares features of strength and durability. While not as hard as tungsten carbide, tungsten metal is still resistant to bending and deformation. Here’s why tungsten holds up well over time:
Feature | Benefit |
---|---|
High Melting Point | Keeps shape at extreme temperatures |
Ductile | Can be drawn into wires or thin sheets |
Corrosion Resistant | Doesn’t rust or degrade easily |
The resilience of tungsten makes it suitable for products that must endure a lot without wearing down. Yet, when extra toughness is essential, tungsten carbide is often the superior choice.
Usage In Industries
Tungsten Carbide and Tungsten play critical roles in various industries. Their unique properties make them ideal for many applications. This section dives into specific industry uses for both materials.
Industrial Applications Of Tungsten Carbide
- Machining and Cutting Tools: It’s a go-to material for tools that need to stay sharp longer and withstand high temperatures.
- Mining and Drilling: Oil and gas industries rely on it for drill bits that can cut through tough earth.
- Metal Forming: It molds other metals into different shapes because it’s so tough.
- Medical Devices: Surgeons use tools made of it for precise cuts.
- Defense: It’s in bullets and armor, protecting lives and equipment.
Industrial Applications Of Tungsten
Industry | Application |
---|---|
Electronics | It makes gadgets work better. |
Lighting | It’s in light bulbs that shine bright. |
Steel Making | It makes steel tough. |
Aerospace | It helps planes fly high and safe. |
Chemistry | It’s important for making other chemicals. |
Advantages
Exploring the unique strengths of Tungsten Carbide and Tungsten unlocks the potential for various applications. Each displays a set of benefits that can meet the needs of different environments. Let’s delve into their respective advantages.
Advantages Of Tungsten Carbide
Tungsten Carbide stands out with its remarkable properties:
- Exceptional hardness, measuring about 8.5 to 9 on the Mohs scale.
- Twice the stiffness and density of steel, making it super durable.
- High resistance to scratching and wear, ideal for long-lasting tools.
- Maintains sharpness over time, perfect for precise cutting tasks.
In industrial settings, Tungsten Carbide’s perks shine:
Industrial Uses | Advantage |
---|---|
Cutting tools | Stays sharp, less frequent replacement. |
Mining equipment | Resists high-pressure, extends service life. |
Drilling accessories | Bores through hard materials, improves efficiency. |
Advantages Of Tungsten
Pure Tungsten also has a set of notable benefits:
- Highest melting point of all metals, ideal for high-temperature applications.
- Minimal thermal expansion, keeping its shape under extreme heat.
- Dense and heavy, useful for counterweights and ballasts.
- Excellent conductivity for electrical applications.
From lighting to aerospace, Tungsten’s advantages are clear:
- Filament in light bulbs: withstands heat, provides prolonged life.
- Electronics: reliable performance in circuits and components.
- Spacecraft: resists thermal deformation in extreme environments.
Disadvantages
Despite the impressive qualities of both materials, Tungsten and Tungsten Carbide are not without drawbacks.
Limitations Of Tungsten Carbide
- Brittleness: Though incredibly hard, Tungsten Carbide can be brittle. Under certain impacts, it might crack or chip.
- Difficult to Work With: The material’s hardness makes it challenging to shape, requiring specialized equipment and techniques.
- Weight: Tungsten Carbide is heavier than some alternative materials, which can be a downside for wearable items.
Limitations Of Tungsten
- Scratch Resistance Overestimated: Pure Tungsten is not as scratch-resistant as Tungsten Carbide, leading to potential surface damage with wear.
- Less Durable: Tungsten is softer than Tungsten Carbide, making it less suited for certain applications requiring extreme durability.
- Conductivity Issues: Tungsten’s electrical conductivity is lower than that of other metals, limiting its usefulness in certain electrical applications.
Cost Comparison
Understanding the financial aspect of products is crucial. Tungsten carbide and tungsten often cause confusion. Let’s explore the cost differences.
Tungsten Carbide Cost
Tungsten carbide is prized for its hardness and durability. The price reflects its qualities. It’s a compound made by combining equal parts tungsten and carbon. The process to create tungsten carbide is complex. This affects its cost. Compared to pure tungsten, tungsten carbide is usually more expensive.
- Better scratch resistance
- Used in jewelry and industrial tools
- Cost varies depending on product and purity
Pricing depends on the final product. For example, a tungsten carbide ring might cost between $100 and $500.
Tungsten Cost
Tungsten, in its pure form, is also a strong material. Pure tungsten offers a unique look. Demand for tungsten fluctuates, which in turn affects cost. Industrial needs often dictate the market price for tungsten metal.
- Less expensive than tungsten carbide
- Used in electronics and as filament in bulbs
- Price is market dependent
Tungsten items, such as wedding bands, might range from $50 to $300.
Material | Usage | Price Range |
---|---|---|
Tungsten Carbide | Jewelry, Industrial Tools | $100 – $500 |
Tungsten | Electronics, Lighting | $50 – $300 |
Both materials offer value for their cost. Tungsten carbide’s durability justifies its higher price. Tungsten’s versatility keeps it in demand.
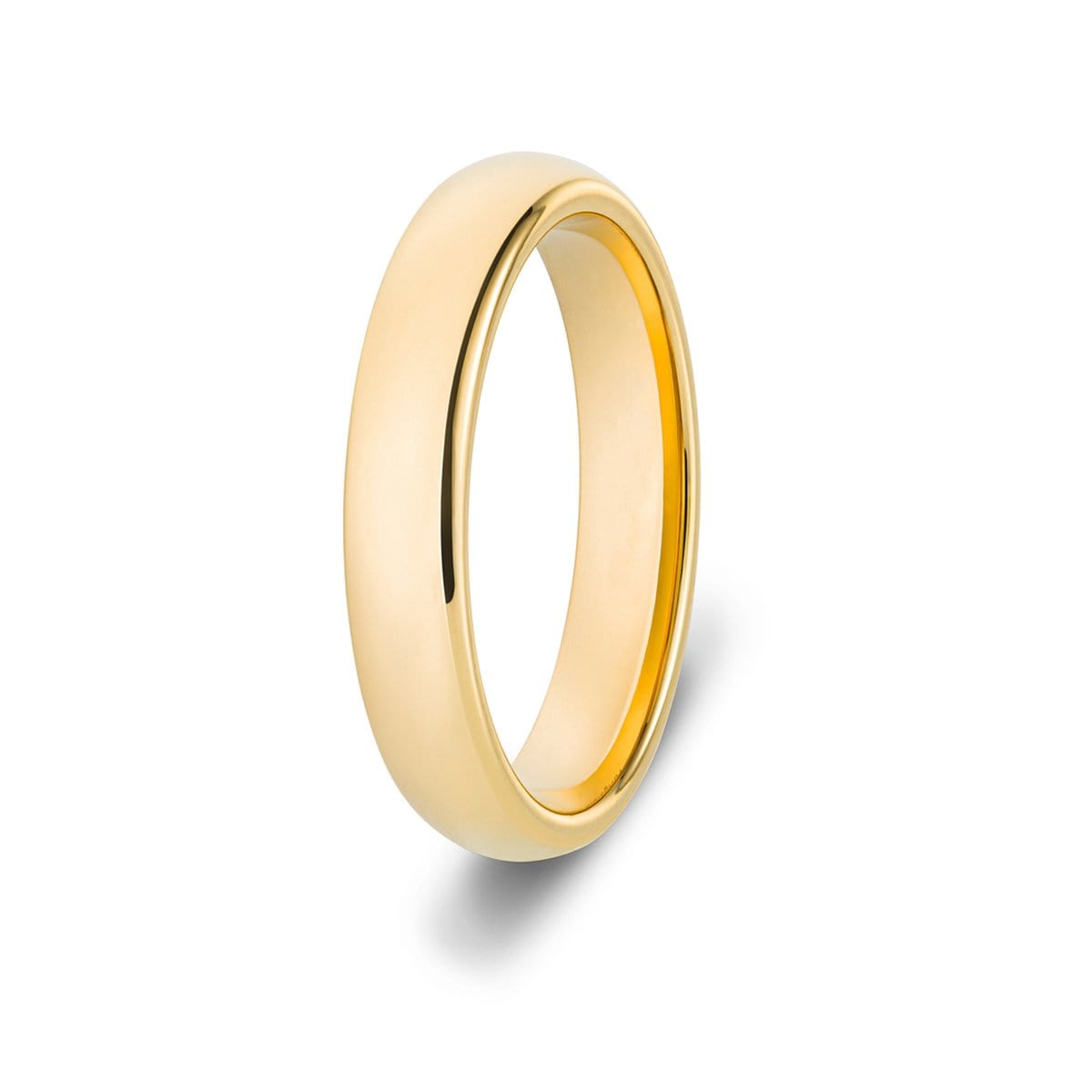
Credit: etrnlrings.com
Environmental Impact
The health of our planet matters to everyone. When choosing materials like Tungsten and Tungsten Carbide, it is key to understand their environmental impacts. This will guide responsible choices for industries and consumers alike.
Environmental Impact Of Tungsten Carbide
Tungsten Carbide (WC) is known for its strength and durability. Its impact on the environment is complex:
- Resource extraction: Mining tungsten ore can disturb ecosystems. Habitats may be lost, and waste products can affect water quality.
- Manufacturing process: Producing WC involves high energy. This leads to carbon emissions which contribute to climate change.
- Waste management: Scrap WC is hard but recyclable. Proper recycling practices reduce environmental strain.
Despite its toughness, WC’s recycling potential helps ease its overall environmental footprint.
Environmental Impact Of Tungsten
Pure tungsten bears its own unique environmental concerns:
- Mining impact: Similar to WC, mining affects landscapes. Tungsten mining involves drilling and blasting which disrupts local biomes.
- Energy usage: Tungsten refining is energy-intensive. It requires electricity that, if sourced from fossil fuels, impacts air quality.
- Longevity: Tungsten products last long. This reduces the frequency of manufacturing and, thus, lowers environmental stress over time.
Tungsten’s long life and low maintenance make it a more sustainable option if managed correctly.
Recycling And Sustainability
Focusing on a green future involves understanding the recycling process for materials like Tungsten Carbide and Tungsten. It’s key to sustainability.
Recycling Of Tungsten Carbide
Tungsten Carbide, known for its hardness and durability, is a prime candidate for recycling. Industries worldwide rely on Tungsten Carbide for making cutting tools, wear-resistant parts, and various heavy-duty components. Reclaiming this material offers tremendous environmental and economic benefits.
- Saves Resources: Limits the need for new raw material extraction.
- Conserves Energy: Less energy required than producing new Carbide.
- Reduces Landfill: Keeps non-biodegradable carbides out of waste disposal.
Specialized recycling facilities are set up to process used Tungsten Carbide. They use methods like chemical recycling, where materials are reclaimed, and then reused in manufacturing.
Recycling Of Tungsten
Pure Tungsten recycling is equally important. It extends the life cycle of the material and reduces environmental strain. The process for recycling Tungsten involves:
- Collection of Tungsten scraps.
- Sorting and preparing for recycling.
- Conversion through smelting.
Most Tungsten scraps come from machining processes, end-of-life products, or manufacturing waste. Through the right practices, organizations can recover much of this valuable resource. This loop supports a sustainable model for Tungsten use worldwide.
Material | Recycling Process | Environmental Impact |
---|---|---|
Tungsten Carbide | Chemical recycling, direct reuse | Highly beneficial |
Tungsten | Smelting and transformation | Eco-friendly and reduces raw material usage |
Future Trends
Exploring the battle of Tungsten Carbide vs. Tungsten reveals a fascinating look into the future.
Innovations and advancements continually reshape their applications. Both materials boast unique properties that set them apart.
Trends In Tungsten Carbide Usage
Tungsten Carbide (WC) is known for its exceptional hardness and durability. Its use spans from cutting tools to construction.
- Jewelry: WC rings maintain popularity for their resilience.
- Aerospace: Strong demand for resistant materials in extreme conditions.
- Automotive: The push for long-lasting components drives WC usage.
- 3D Printing: WC powder is crucial for industrial-grade printing.
The tech industry seeks WC for its efficient electrical conductivity.
Future Prospects For Tungsten
Pure tungsten remains vital for its high melting point and thermal conductivity.
Industry | Use of Tungsten |
---|---|
Lighting | Filaments use Tungsten’s heat resistance. |
Electronics | Tungsten’s conductivity enhances devices. |
Medical | X-ray and radiation shields rely on it. |
Research in nanotechnology anticipates new Tungsten uses.
The material’s versatility will witness increased demand in tech applications.
References
Understanding the differences between Tungsten Carbide and Tungsten demands reliable sources. Below are carefully selected references for those seeking deeper insights.
Sources Cited
- “Tungsten Carbide. A material for the ages” – Journal of Material Sciences
- “Comparative Analysis of Tungsten Carbide and Tungsten Properties” – International Review of Mechanical Engineering (IREME)
Further Reading
Expand your knowledge on this topic with the following readings:
- “Tungsten Carbide: Industrial Applications and Performance” – Industrial Material Handbook
- “The Tungsten Advantage: Utilization in High-Precision Tools” – Advanced Fabrication Technology Review

Credit: www.northwestdiamonds.com
Frequently Asked Questions Of Tungsten Carbide Vs Tungsten
What Is Tungsten Carbide?
Tungsten Carbide is a chemical compound containing equal parts of tungsten and carbon atoms. It’s known for its exceptional hardness and is often used in cutting tools and industrial machinery.
How Does Tungsten Differ From Tungsten Carbide?
Tungsten is a pure element, whereas Tungsten Carbide is a compound made from tungsten and carbon. Tungsten is softer and less durable compared to the very hard and wear-resistant Tungsten Carbide.
What Are The Uses Of Tungsten Carbide?
Tungsten Carbide is primarily used in the manufacturing of wear-resistant tools, cutting blades, industrial machinery parts, and in the jewelry industry for scratch-resistant rings.
Is Tungsten Or Tungsten Carbide Better For Jewelry?
Tungsten Carbide is preferred for jewelry due to its higher hardness and resistance to scratching. Tungsten alone is softer and may not endure everyday wear as effectively.
Conclusion
In summarizing the duel between tungsten carbide and tungsten, your choice hinges on usage. Tungsten carbide stands out for resilience and hardness, perfect for industrial applications. Pure tungsten, with its high melting point, shines in electrical contexts. Each holds distinct advantages tailored to specific needs, ensuring you make an informed selection for optimal performance.