Cad welding, also known as exothermic welding, is a bonding process that utilizes a chemical reaction to produce heat and fuse metals. This process creates a strong, conductive, and corrosion-resistant connection ideal for permanently joining electrical conductors or grounding applications.
Exothermic welding involves using a mold to contain and shape the molten metal. The process begins by igniting a mixture of powdered copper oxide and aluminum, which produces the high temperatures necessary to melt the conductive materials. Cad welding ensures a superior connection compared to mechanical or compression methods because it forms a molecular bond between the conductors.
Professionals often use this type of welding in electrical, rail, and construction industries for its durability and reliability. The process requires minimal training and equipment, making it highly efficient. The one-time-use molds designed for specific connections underscore the precise nature of this welding technique. Cad welding’s consistent results support infrastructure safety and longevity, reinforcing its essential role in various industrial sectors.
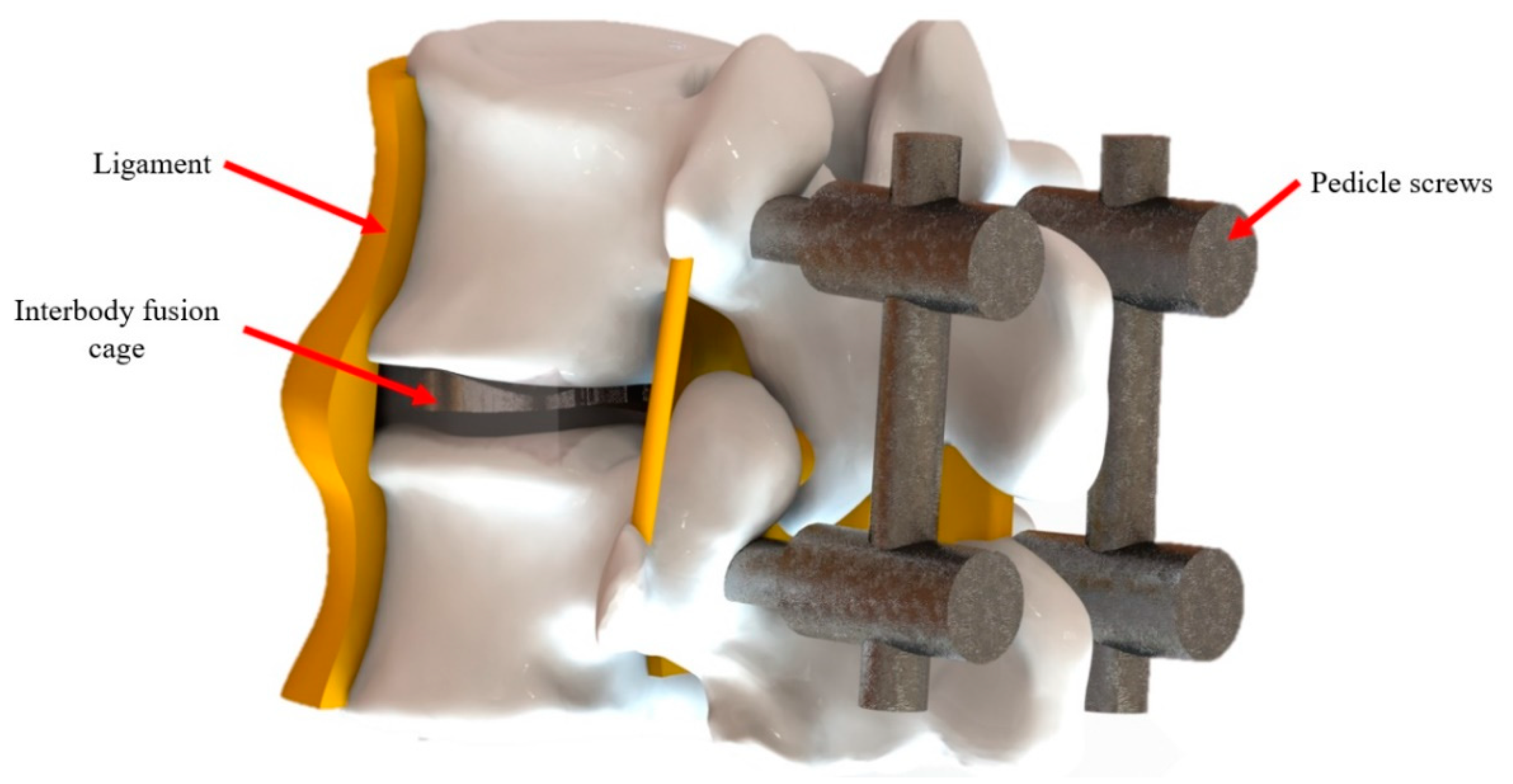
Credit: www.mdpi.com
The Basics Of Cad Welding
Imagine two metals becoming one without a clunky bolt or a riveting joint. This is the magic of CAD welding, a process that revolutionizes how we join metals. Let’s dive into the basics of this innovative technique.
What Is Cad Welding?
CAD welding, also known as Exothermic Welding, is a method where metallic parts are fused together. It uses a high-temperature chemical reaction to produce a molten metal that joins the other two metals. Unlike traditional welding, CAD doesn’t require external heat sources.
How Does Cad Welding Work?
The process begins with a mold, where the metals to be joined are held in place. Next, a starting powder is ignited to initiate the reaction. Within seconds, the temperature soars, and molten metal fills the mold, creating a solid, sturdy bond once cooled.
- Mold Preparation: Clean and place conductors in the mold.
- Welding Material: Add welding powder and starting material.
- Ignition: Ignite the starting material which melts the welding powder.
- Cooling: Allow the joint to cool and solidify for a strong bond.
Steps | Description |
---|---|
1. Setup | Prepare mold and place conductors. |
2. Add Materials | Place welding and starting powders. |
3. Ignition | Use flint igniter to start the reaction. |
4. Bond Formation | Wait for the exothermic reaction to create a join. |
5. Cooling | Let the new joint cool and solidify. |
With these steps, metals achieve a permanent bond that’s highly conductive and corrosion-resistant. CAD welding’s simplicity ensures a reliable, maintenance-free joint for various applications.
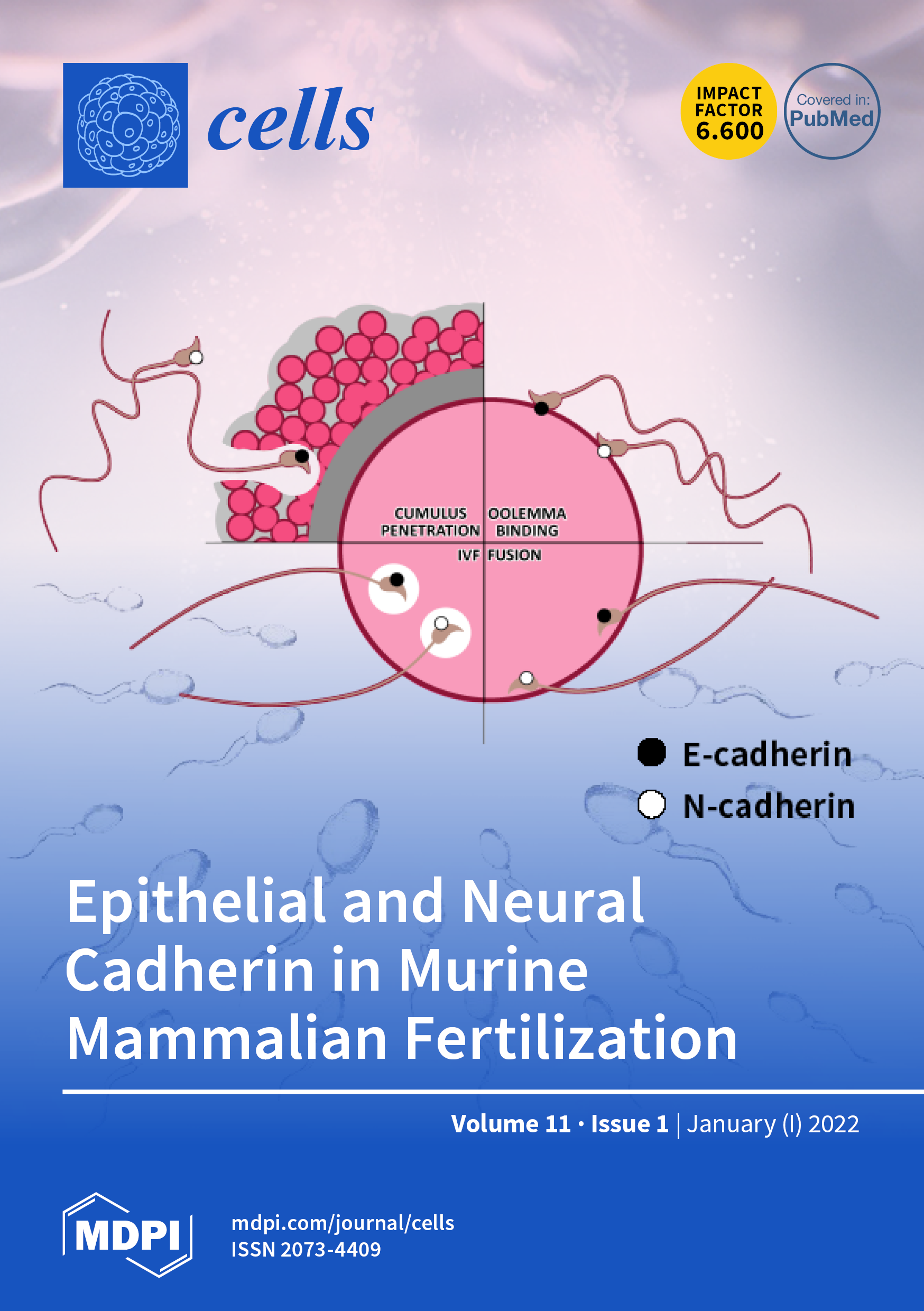
Credit: www.mdpi.com
Advantages Of Cad Welding
CAD Welding, or Computer-Aided Design welding, leverages technology for joining metals. This process has transformed the fabrication industry. Below, we explore its key benefits.
Increased Precision And Accuracy
One of the standout benefits of CAD Welding is its high level of precision and accuracy. Computer software allows welders to plan their projects with intricate detail.
- Exact measurements and specifications guide the welding process.
- This precision leads to consistent quality across welding projects.
- CAD Welding can produce complex structures without human error.
Reduced Time And Cost
CAD Welding significantly cuts down on project time and associated costs. Here’s how:
Aspect | Benefit |
---|---|
Efficiency | Projects are completed faster, using less manpower. |
Material Usage | Optimized use of materials means fewer wastes. |
Revisions | Fewer mistakes lead to less time spent on revisions. |
Enhanced Safety
With CAD Welding, safety takes a front seat. This technology-forward approach minimizes risks:
- Welding plans are assessed for potential safety issues before implementation.
- Automated processes reduce human interaction with dangerous equipment.
- Consistent quality means fewer structural failures and accidents.
Applications Of Cad Welding
CAD welding, also known as exothermic welding, finds application across multiple industries. Its ability to create highly durable and conductive joints makes it indispensable in sectors where reliability is crucial. Let’s delve into the details of how CAD welding is deployed within different industries.
Automotive Industry
The automotive sector relies on CAD welding to ensure robust electrical connections. It plays a vital role in:
- Battery terminal fabrication
- Engine grounding
- Attaching electronic components
The method delivers joints that withstand high vibrations and temperatures, prominent in vehicular environments.
Construction Industry
In construction, CAD welding secures infrastructure:
Application | Significance |
---|---|
Rebar splicing | Enhances structural integrity |
Earthing systems | Improves safety and reliability |
The joints made through CAD welding in construction are known for longevity and resist corrosion effectively.
Aerospace Industry
CAD welding secures critical connections in aerospace, vital for:
- Safety of flight instruments
- Grounding applications
- Fuel line continuity
This ensures both uncompromised performance and safety in extreme conditions.
Credit: www.facebook.com
Future Trends In Cad Welding
The world of CAD welding is always evolving. With new technologies shaping how we join metals, the future of this field looks brighter than ever. We explore the latest trends that will revolutionize CAD welding.
Integration Of Ai And Robotics
Robots are not science fiction in welding anymore. AI and robotics blend for better precision. This means higher quality welds every time.
- Robots learn from mistakes, making fewer as they go.
- AI predicts outcomes, adjusting techniques in real-time.
- Safety improves, with robots handling dangerous tasks.
Automated systems are getting smarter. They are set to take CAD welding to new heights.
Advancements In Welding Materials
New materials mean better welds. Research is yielding fascinating results:
- Lighter, yet stronger materials are in development.
- Conductive adhesives open new welding possibilities.
- Environment-friendly options are becoming more common.
Materials science is pushing the boundaries of what’s possible in CAD welding.
Frequently Asked Questions Of What Is Cad Welding
What Is Cad In Welding?
CAD in welding refers to the use of Computer-Aided Design software to create detailed 3D models and plans for welding projects. It enhances precision and efficiency in welding fabrication.
What Are The Hazards Of Cad Welding?
CAD welding hazards include intense heat, harmful fumes, loud noises, bright flashes that can damage eyes, and the risk of burns or fires. Good ventilation and protective gear are essential for safety.
Is Cad Welding Considered Hot Work?
Yes, CAD welding is considered hot work as it involves heating and joining metals, creating a potential fire hazard.
What Is Cadweld Shot Made Of?
Cadweld shots consist of a mixture of copper oxide and aluminum powder, utilized for creating permanent exothermic welds in grounding and bonding applications.
Conclusion
Cad welding, a robust method aligning precision and durability, stands out in metalwork. This process fuses materials at a molecular level, offering exemplary strength. It’s a go-to for electrical and structural connections that last. As we’ve explored, cad welding’s reliability and efficiency make it indispensable for industries seeking long-term solutions.
Embrace this technique for secure, high-quality joins.