For optimal performance with 1/16 flux core wire, set the amperage between 50 to 120A and the voltage from 16 to 22V. Adjust wire feed speed from 90 to 340 inches per minute depending on the application.
Understanding the right settings for 1/16 flux core wire is essential for achieving strong, high-quality welds. These settings will vary based on the material thickness and the welding position. Working with flux core welding requires a balancing act between heat input, penetration, and welding speed.
An accurate setup ensures a stable arc and proper bead appearance, essential for both professional and hobbyist welders. Start by setting your welder to the manufacturer’s recommended baseline and fine-tune as needed based on your results. Remember, practice and experience play a significant role in identifying the sweet spot for any given welding project. A well-adjusted welder leads to improved efficiency and cleaner welds, reducing the need for post-weld clean-up.
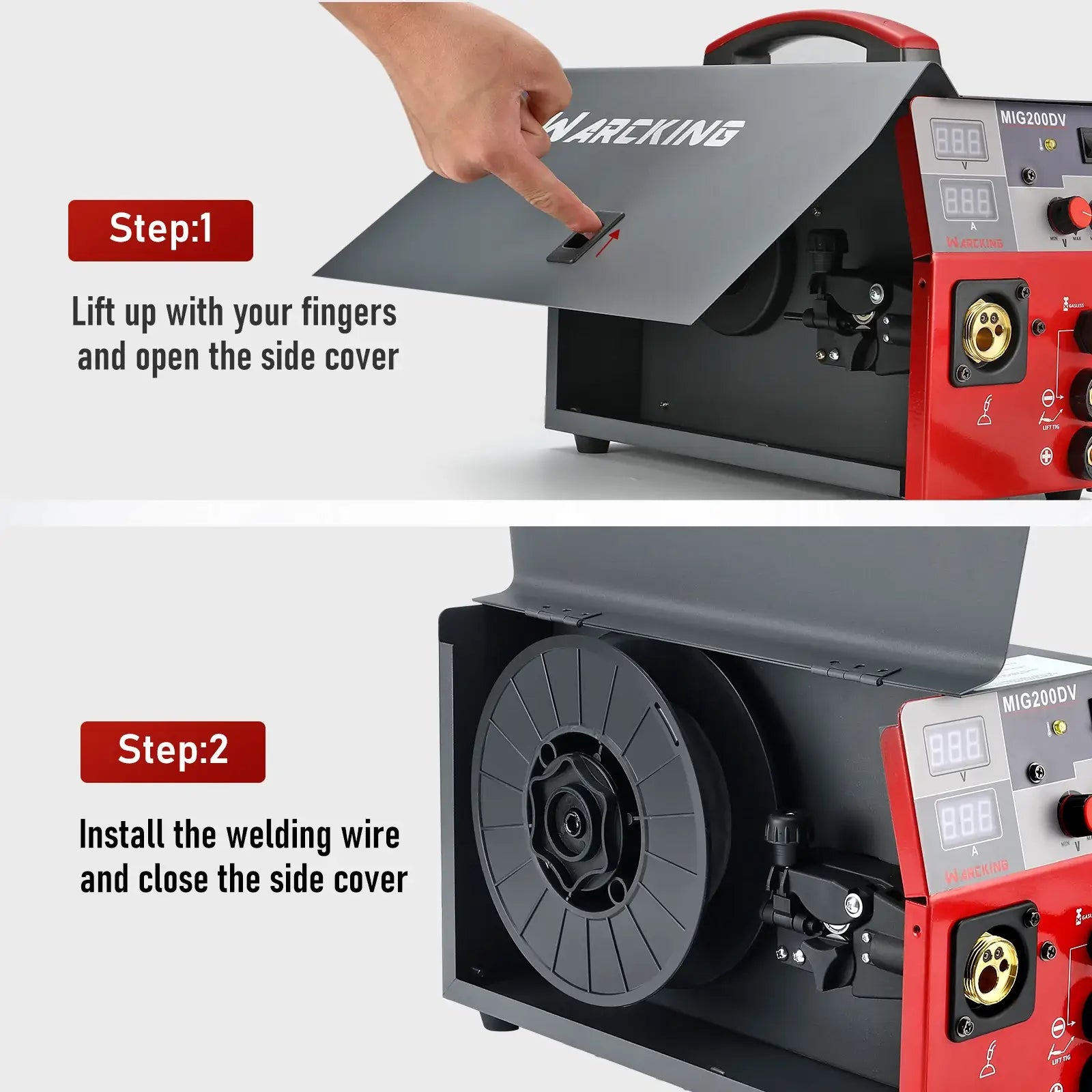
Credit: warcking.net
Basics Of 1/16 Flux Core Wire
Embarking on the journey of welding involves getting to grips with the tools and equipment that welders rely on. In the world of welding, 1/16 flux core wire emerges as a popular choice for its versatility and ease of use. Whether you’re a seasoned professional or a novice, understanding the fundamentals of this wire can enhance your welding projects significantly.
Definition And Characteristics
Flux core wire is a tubular welding filler metal that comes with a flux at its core, designed to shield the weld pool from contaminants without the need for external gas. The 1/16 dimension refers to the diameter of the wire, ideally suited for medium to heavy-duty welding tasks. Here are some key characteristics:
- Self-shielding capability, eliminating the need for a separate shielding gas
- Suitable for all-position welding, offering excellent versatility
- High deposition rate, which speeds up the welding process
- Produces a slag which peels off easily, ensuring a cleaner weld
Advantages And Applications
The 1/16 flux core wire is not just defined by its characteristics; its advantages make it an indispensable tool. This wire:
Advantages | Applications |
---|---|
|
|
The far-reaching utility of 1/16 flux core wire across various industries underscores its importance. From heavy-duty construction to robust equipment repairs, its applications mirror its strengths, providing a practical solution for challenging welding scenarios.
Parameters For 1/16 Flux Core Wire
Perfecting the art of welding with 1/16 Flux Core Wire begins with a comprehensive understanding of its key parameters: wire speed and voltage settings. Delivering quality welds depends heavily on tuning these factors to align with the thickness of the material being welded and the position of the weld. This section breaks down these critical elements, providing a reference guide to optimize your welding performance.
Wire Speed
Wire speed, a pivotal parameter for maintaining a consistent welding arc, dictates the flow rate of the wire feeding through your welding gun. An appropriate wire speed harmonizes with the voltage setting to prevent issues like spatter, incomplete fusion, or excessive burn-through. Below are recommended wire speed settings for using 1/16 Flux Core Wire:
- Fine detail work: Lower speeds to ensure precision.
- Thicker material: Increased wire speeds to penetrate effectively.
- Overhead welding: Moderate speeds to reduce the risk of dripping.
Voltage Settings
The voltage settings affect the arc length and the heat input into the material. For 1/16 Flux Core Wire, correct voltage settings are instrumental in managing penetration and avoiding defects such as undercutting or lack of fusion. The following outlines ideal voltage settings for various scenarios:
Material Thickness | Typical Voltage Setting |
---|---|
Thin metals | Lower voltage to avert burn-through |
Medium thickness | Mid-range voltage for balanced penetration |
Thick materials | Higher voltage for deep penetration |
Techniques For Optimal 1/16 Flux Core Welding
1/16 flux core welding is a nuanced technique that demands precision and skill. Achieving the best results with this welding method involves understanding the right settings and movement. The key is to master the heat input and travel speed and angle. By doing so, welders can enhance penetration, control the weld pool, and minimize weld defects. Whether you’re a seasoned professional or just starting out, these strategies will help you refine your 1/16 flux core welding process.
Travel Speed And Angle
The correct travel speed and angle are critical for producing strong and clean welds. As with any welding process, too slow of a travel speed can lead to a buildup of excess material, causing slag inclusions and other defects. Conversely, a fast travel speed might not allow for proper penetration or could result in incomplete fusion.
- Travel Speed: Maintain a consistent speed that allows the weld puddle to fully form but also keeps it from getting too large or out of control.
- Travel Angle: Use a slight drag angle (typically between 15 to 30 degrees) when welding in the flat, horizontal, or overhead positions. This helps improve penetration and allows you to see the weld puddle more clearly.
For an ideal weld, balance is essential. Adjust your technique according to the position and type of joint being welded. Practicing on scrap metal helps to find the right pace and angle before attempting the final weld.
Heat Input Management
Managing heat input is a balancing act. With 1/16 flux core wire, it’s especially important to avoid too much heat as it can compromise weld integrity by creating burn-through or excessive warping in the metal. Conversely, insufficient heat may lead to weak welds that do not penetrate sufficiently.
Parameter | Guideline |
---|---|
Voltage | Set the voltage within the recommended range for 1/16 flux core wire. This ensures a stable arc and proper bead formation. |
Amperage | Adjust amperage to control heat input, modifying it according to the thickness of the metal and the welding position. |
Stick-Out | Keep the stick-out at about 3/4 inch, as too much can cause spatter and too little can reduce stability and control. |
Remember that thermal conductivity of the base metal, joint thickness, and even ambient temperature can affect optimal heat settings. Running a few test passes on similar scrap metal allows for fine-tuning before the actual weld.
Common Mistakes With 1/16 Flux Core Wire Settings
Many welders, both novices and experienced, often face challenges when working with 1/16 flux core wire. Proper settings are crucial for strong, durable welds, yet a few common missteps can lead to suboptimal results. Understanding these errors is key to avoiding them and ensuring a smooth welding experience.
Overheating
Overheating occurs when the welder uses excessive heat during the welding process. This not only compromises the integrity of the weld but can also lead to warping of the material. Here are some indicators and consequences of overheating:
- Discoloration of the weld or base metal
- Excess spatter, causing additional cleanup
- A burnt or excessively fluid weld pool
- Carefully check and adjust the amperage settings
- Ensure a consistent travel speed
- Maintain the correct stick-out length
Consistency in technique is crucial for preventing the adverse effects of too much heat input.
Inconsistent Penetration
Inconsistent penetration can be just as problematic, leading to weak welds that are prone to failure. This usually stems from incorrect speed or power settings. Issues with penetration often manifest as:
- Welds that sit on top of the base metal without proper fusion
- Excessive penetration leading to burn-through
- Visible lack of uniformity in the weld bead
- Match the voltage and wire feed speed to the thickness of your base metal
- Angle the welding gun properly to ensure even heat distribution
- Monitor travel speed to avoid staying too long in one spot
Attention to detail and regular adjustments based on material feedback are vital for attaining the desired penetration.
Adjusting Settings For Different Materials
Welcome to the nuanced world of welding, where precision is pivotal, and the right settings can make or break your project. When it comes to using 1/16 Flux Core Wire, understanding how to adjust your welding setup for different materials is crucial. Each material conducts heat and reacts to welding techniques differently, necessitating a tailored approach. Whether you’re working with steel, stainless steel, or aluminum, this guide will help ensure your welding projects are successful and of high quality. Let’s dive into the specifics of adjusting your welder’s settings to match the requirements of the material at hand.
Steel
When welding steel with 1/16 flux core wire, the right combination of voltage and wire feed speed is essential. Typically, a higher voltage and moderate wire feed speed are recommended. Be mindful of your material’s thickness: the thicker it is, the higher the heat settings should be.
- Mild Steel (up to 1/8″): 15-18 volts with wire feed speed of 110-130 inches per minute (IPM)
- Thicker Steel (1/8″ to ½”): 18-20 volts with wire feed speed of 120-150 IPM
Stainless Steel
Welding stainless steel demands a cautious approach to prevent warping and maintain the material’s corrosion-resistant qualities. A slightly lower voltage compared to mild steel, coupled with a higher wire feed speed, contributes to a stable arc and reduced overheating.
Thickness | Voltage | Wire Feed Speed (IPM) |
---|---|---|
Up to 1/8″ | 14-16 | 160-180 |
1/8″ to 3/8″ | 17-19 | 170-190 |
Aluminum
Aluminum poses unique challenges due to its high thermal conductivity and low melting point. A softer touch is often necessary, with lower voltage settings and a carefully adjusted feed speed to prevent burn-through and ensure proper penetration.
- Begin with a clean surface, free from oxides and impurities.
- Use a lower voltage setting, around 15-17 volts for aluminum.
- Adjust the wire feed speed, normally in the range of 110-140 IPM.
It’s key to practice on scrap aluminum before tackling the main project to fine-tune these settings for your specific equipment and application.
Troubleshooting 1/16 Flux Core Welds
Welcome to the pivotal segment of our comprehensive guide, where we delve into the intricacies of troubleshooting 1/16 flux core welds. Welding with a 1/16 flux core wire can be highly rewarding, presenting an ideal balance between versatility and penetration power. Yet, as with any welding process, it’s not free from potential hiccups. Grasping the nuances of fine-tuning your welder settings can mean the difference between a strong, clean weld and one that’s fraught with issues. Below, we’ll explore some common complications and offer practical solutions to help you achieve impeccable flux core welding results.
Porosity
Porosity in welding refers to the presence of tiny holes or voids within the weld bead that can seriously compromise its strength and integrity. When you’re working with 1/16 flux core wire, porosity can stem from several factors:
- Improper gas shielding: Even though flux core welding typically doesn’t require an external gas, environmental conditions or a faulty wire may introduce contaminants.
- Incorrect settings: Setting the voltage and wire feed speed too low can lead to incomplete fusion and trapped gas.
- Material contamination: Ensure that the base materials are clean and free of rust, paint, or grease before welding.
To counteract porosity, check your welder’s settings and adjust accordingly. Cleaning your base material thoroughly and ensuring a proper work environment can also drastically reduce the occurrence of porosity.
Spatter
Spatter represents those pesky droplets of molten metal that scatter during the welding process, adhering to the workpiece or surrounding areas. It’s a common but annoying issue when welding with 1/16 flux core wire. The culprits are usually:
- Incorrect wire feed speed: Too high or too low can cause an unstable arc and result in spatter.
- Suboptimal voltage settings: Like wire feed speed, misjudged voltage can disrupt the arc stability, causing spatter.
- Poor contact tip condition: Worn out or improperly sized contact tips can affect the wire feed and lead to spatter.
Adjusting your wire feed speed and voltage to the sweet spot is critical. Ensure the contact tip is in good condition and the correct size for your wire. Practicing these measures will significantly reduce spatter and create a smoother welding experience.
Advancements In 1/16 Flux Core Wire Technology
Staying abreast of the latest technological advancements is key in any industry, and the world of welding is no exception. The introduction and refinement of 1/16 Flux Core Wire Technology has been a game-changer, offering numerous benefits over traditional welding methods. This innovative leap has not only enabled welders to work more efficiently but has also greatly improved the quality of welds. Let’s delve into the innovations that have revolutionized the way professionals approach welding tasks.
Innovations In Wire Composition
The core of changes in flux core wire technology lies in the innovations in wire composition. Manufacturers have developed new formulas that enhance the wire’s performance in several dimensions. The most impactful alterations include:
- Alloy Additions: By integrating various alloys into the wire, the tensile strength, and durability of the resulting welds have seen a significant boost. This means that welds can withstand higher stresses without failure.
- Reduced Slag: Advanced compounds in the wire have led to reduced slag creation, which in turn means cleaner welds and less post-weld clean-up, saving valuable time and effort.
- Improved Arc Stability: Latest 1/16 flux core wires are engineered to provide a more stable arc, giving welders better control and producing higher quality welds even in challenging positions.
These compositional innovations have enhanced the wire’s utility and adaptability, allowing welders to achieve better results with greater ease.
Impact On Welding Processes
With enhanced wire technology, the impact on welding processes has been profound. Here’s what has changed:
Traditional Processes | Advancements with 1/16 Flux Core Wire |
---|---|
Requires extensive pre-weld set-up | Streamlined preliminary preparations |
Higher post-weld clean-up due to slag | Minimal post-weld cleaning |
Variable weld quality in different environments | Consistent performance across diverse conditions |
These innovative wires have expanded the potential for welding operations in numerous settings, providing benefits such as:
- Enhanced Efficiency: Faster welding processes without compromising on strength or quality.
- Environmental Adaptability: Performant in inclement weather and less than ideal conditions.
- Improved Accessibility: More forgiving for beginner welders while granting experienced professionals additional flexibility.
Overall, these advancements have not just reshaped workflows, but they’ve also set new industry standards for what can be accomplished with flux core welding technology.
Frequently Asked Questions Of 1/16 Flux Core Wire Settings
What Is 1/16 Flux Core Wire?
1/16 Flux Core Wire is a type of welding wire used without external gas. It’s suitable for outdoor welding and has a flux core that helps shield the weld. This size is commonly used for medium-thickness materials.
Best Settings For 1/16 Flux Core Wire?
The best settings for 1/16 Flux Core Wire usually start around 120-150 amps for voltage and 250-300 ipm for wire feed speed. Fine-tuning will depend on material thickness and welding position.
How To Choose 1/16 Flux Core Wire?
Choose 1/16 Flux Core Wire based on material compatibility, welding position, and desired bead profile. Look for wires that match your base material and are suited for your welding machine’s capabilities.
When To Use 1/16 Flux Core Wire?
Use 1/16 Flux Core Wire for medium gauge materials, especially when working outdoors or in drafty conditions. It’s ideal for construction, shipbuilding, and repair work where gas shielding is impractical.
Conclusion
Selecting the correct settings for your 1/16 flux core wire is crucial. Achieve optimal welding results by fine-tuning your voltage, amperage, and wire feed speed. Remember, practice makes perfect. Embrace the guidelines shared, and you’ll master the art of flux core welding.
Your projects await your enhanced skillset.