6011 and 6013 welding rods differ primarily in their coating and welding positions. The 6011 rod offers deep penetration and can weld dirty or rusted metal, while 6013 is ideal for clean surfaces and provides a smoother finish.
Understanding the nuances of welding rods plays a crucial role for welders tackling diverse metalwork projects. The choice between a 6011 and a 6013 welding rod can significantly impact the quality and efficiency of welding tasks. The 6011 rod, with its high cellulose potassium coating, ensures deep penetration and is known for its ability to weld through dirt, paint, and rust—making it a go-to for maintenance or repair work.
On the other hand, the 6013 welding rod features a rutile potassium coating, which facilitates a smoother, more controlled weld appearance and is often preferred for creating clean, aesthetic welds on new materials. For those venturing into welding, selecting the correct electrode can be the difference between a strong, reliable joint and a subpar bond, emphasizing the importance of knowledge in welding practices.

Credit: www.amazon.com
Composition
Understanding the composition of welding rods is key for welders. It affects how they melt and join metals. 6011 and 6013 welding rods are common. Each has unique elements. These ingredients give the rods different properties.
6011 Welding Rod Composition
The 6011 welding rod is well-known for its versatility. It’s made for tough welding jobs. Key components in 6011 rods include:
- Cellulose – It helps with deep penetration.
- Iron Powder – Adds to the rod’s strength.
- Potassium – Aids in arc stability.
These rods handle rusty and dirty surfaces well. They’re perfect for outdoor repairs. We list more ingredients in a 6011 rod:
Element | Percentage |
---|---|
Carbon (C) | 0.2% |
Manganese (Mn) | 0.6% |
Silicon (Si) | 0.2% |
Phosphorus (P) | 0.035% |
Sulfur (S) | 0.035% |
6013 Welding Rod Composition
The 6013 welding rod is another popular choice. It’s known for producing a smoother finish. Its composition includes:
- Titanium Dioxide – Makes it easier to use.
- Iron Powder – Also found in 6011, for strength.
- Potassium – For arc stability, like in 6011.
6013 rods are great for clean metal surfaces. They’re good for beginners. They make nice-looking welds. Here’s a breakdown of the 6013 rod’s elements:
Element | Percentage |
---|---|
Carbon (C) | 0.1% |
Manganese (Mn) | 0.3-0.6% |
Silicon (Si) | 0.2% |
Phosphorus (P) | Less than 0.035% |
Sulfur (S) | Less than 0.035% |
Both rods differ in composition. This affects their use. By knowing this, welders can choose the right rod for their project.
Characteristics
Exploring the characteristics of welding rods is crucial for any welding job. The 6011 and 6013 rods, popular in welding, possess unique features catered to different applications. Understanding their properties can lead to more precise and stronger welds.
6011 Welding Rod Characteristics
The 6011 welding rod is well-known for its versatility and flexibility. Here are its core characteristics:
- Deep Penetration: Provides strong welds on dirty or rusty materials.
- Fast Freeze: The rod’s coating helps quick solidification, ideal for vertical or overhead welding.
- AC/DC Compatible: Can be used with both AC and DC welding machines.
- Tough Welds: The welds can withstand vigorous conditions, making them suitable for repair work.
- All Positions: Designed to weld in all positions, enhancing its adaptability.
6013 Welding Rod Characteristics
The 6013 welding rod contrasts with a focus on smooth and easy weldability. Key characteristics include:
- Moderate Penetration: Ideal for thin metals and cosmetic welds.
- Stable Arc: Easy to strike and maintain, perfect for beginners.
- Clean Weld Appearance: Minimal spatter and a smooth finish.
- Low to Medium Deposits: Effective for controlled build-up.
- Minimal Slag: Leaves minimal slag, easing post-weld cleanup.
Applications
Exploring the vast realm of welding requires specific tools for different tasks. The choice between a 6011 welding rod and a 6013 welding rod depends greatly on their applications. These rods, each with unique properties, serve distinct purposes across diverse environments and materials. Let’s delve into where and how each of these rods excels in the world of welding.
6011 Welding Rod Applications
Known for its versatility, the 6011 welding rod becomes a go-to for challenging welding jobs. The deep penetration ability of the 6011 rod allows it to handle:
- Rusty or oily metals
- Thick materials
- Outdoor repairs, even with windy conditions
The 6011’s flexibility makes it a favorite for applications involving:
Industry | Use-Case |
---|---|
Construction | Structural steel frameworks |
Pipeline | Field repairs |
Shipbuilding | Assembly and maintenance |
6013 Welding Rod Applications
The 6013 welding rod is ideal for projects that require a smooth finish and easier control. Preferred for its medium penetration, it is well-suited for:
- Light to medium gauge metals
- Creating smooth, clean welds for a polished look
- Beginners mastering welding technique
Its stable arc and low spatter make it a prime choice for:
- Automotive bodies and frames
- General metal fabrication
- Household and decorative items

Credit: bakersgas.com
Welding Performance
Welcome to the heart of welding artistry – Welding Performance. Here, we create strong bonds, literally. When choosing welding rods, performance matters. Let’s dive into how 6011 and 6013 rods handle the heat of creation.
6011 Welding Performance
The 6011 welding rod is a favorite for its versatility. Here’s why:
- Deep penetration: Ideal for cutting through rust or paint.
- All-position flexibility: Use it overhead, vertically, or in any space.
- Fast cooling: Minimizes warping risks on thinner materials.
- AC and DC compatibility: Handy in diverse power situations.
Its aggressive arc makes it a top pick for experienced welders tackling hard-to-bond projects.
6013 Welding Performance
For a smoother experience, the 6013 shines. Here’s what makes it special:
- Stable arc: Less spatter, cleaner weld lines.
- Medium penetration: Great for thin to medium gauges.
- User-friendly: Ideal for beginners and pros alike.
- Polished finish: Creates aesthetically pleasing welds.
Its forgiving nature allows for a broader range of applications with an emphasis on appearance.
We could use a table for a quick comparison but given the instructions to avoid unnecessary words, a simple listing is maintained.Weld Appearance
When choosing a welding rod, weld appearance matters. Welders often compare the 6011 and 6013 rods. These rods create different looks. This part explains those looks. We’ll explore how each rod affects the final appearance of a weld.
6011 Weld Appearance
The 6011 welding rod is known for its versatility. It produces welds that may not be the prettiest. But they are strong and durable. The 6011 rod works well on dirty or rusty materials.
- Rough texture: The welds have a more rugged finish.
- Ripples: You might notice more ripples than other rods create.
- Deep penetration: It can lead to prominent weld beads.
- Spatter: Expect some spatter around the weld area.
6013 Weld Appearance
For a cleaner and more aesthetically pleasing finish, the 6013 rods stand out. They excel on thin metals. They are perfect for smooth welds. They are a top choice for cosmetic welds.
- Smooth texture: 6013 welds generally look neater.
- Fine ripples: The ripples are less pronounced.
- Less penetration: The bead appears more uniform and less raised.
- Low spatter: They often result in minimal spatter.
Thus, when finish matters, consider these points. A professional look often requires the finesse of a 6013. In contrast, for industrial strength, a 6011’s appearance is a small trade-off.
Suitable Welding Conditions
Understanding the suitable welding conditions for different rods is crucial for welders.
Each rod performs optimally under certain conditions.
Let’s explore the environments in which 6011 and 6013 welding rods excel.
6011 Welding Conditions
6011 welding rods are known for their versatility and deep penetration.
- Best for dirty, rusty, or painted surfaces.
- Ideal for outdoor use, even in windy conditions.
- Performs well with AC and DC power sources.
- Excel in fast-fill and fast-freeze applications.
These rods are perfect for repair jobs and maintenance.
6013 Welding Conditions
The 6013 welding rods offer a smooth, steady arc.
- Great for clean, new sheet metal work.
- Preferred for indoor projects, away from the elements.
- Suitable for AC, DCEN, and DCEP power sources.
- Used in applications where appearance matters.
These rods provide a clean and controlled weld, often used for cosmetics.
Advantages
Exploring the advantages of 6011 and 6013 welding rods is crucial when you want the best results. Both types of rods bring unique benefits to the table. Understanding these perks can guide welders to make better choices based on the requirements of their projects.
Advantages Of Using 6011 Welding Rods
- Strong welds: 6011 rods provide robust joints that hold up against time and stress.
- Flexible with power sources: They can be used with both AC and DC currents, offering versatility.
- Deep penetration: Great for welding thicker materials due to their ability to penetrate deeply.
- Works on dirty metals: Perfect for rusty or painted surfaces as they can burn through contaminants.
- All-position welding: They are suitable for use in all positions, which adds to their flexibility.
Advantages Of Using 6013 Welding Rods
- Easy to use: 6013 rods offer smooth arc starts which are ideal for beginners to practice with.
- Minimal spatter: They produce less spatter, making clean-up much easier post-weld.
- Clean weld appearance: Creates smooth welds that often require little to no finishing work.
- Medium penetration: Suitable for thin to medium thickness metals, providing enough depth without burning through.
- Light fabrication: Perfect for projects requiring a neat finish like light frames or furniture.
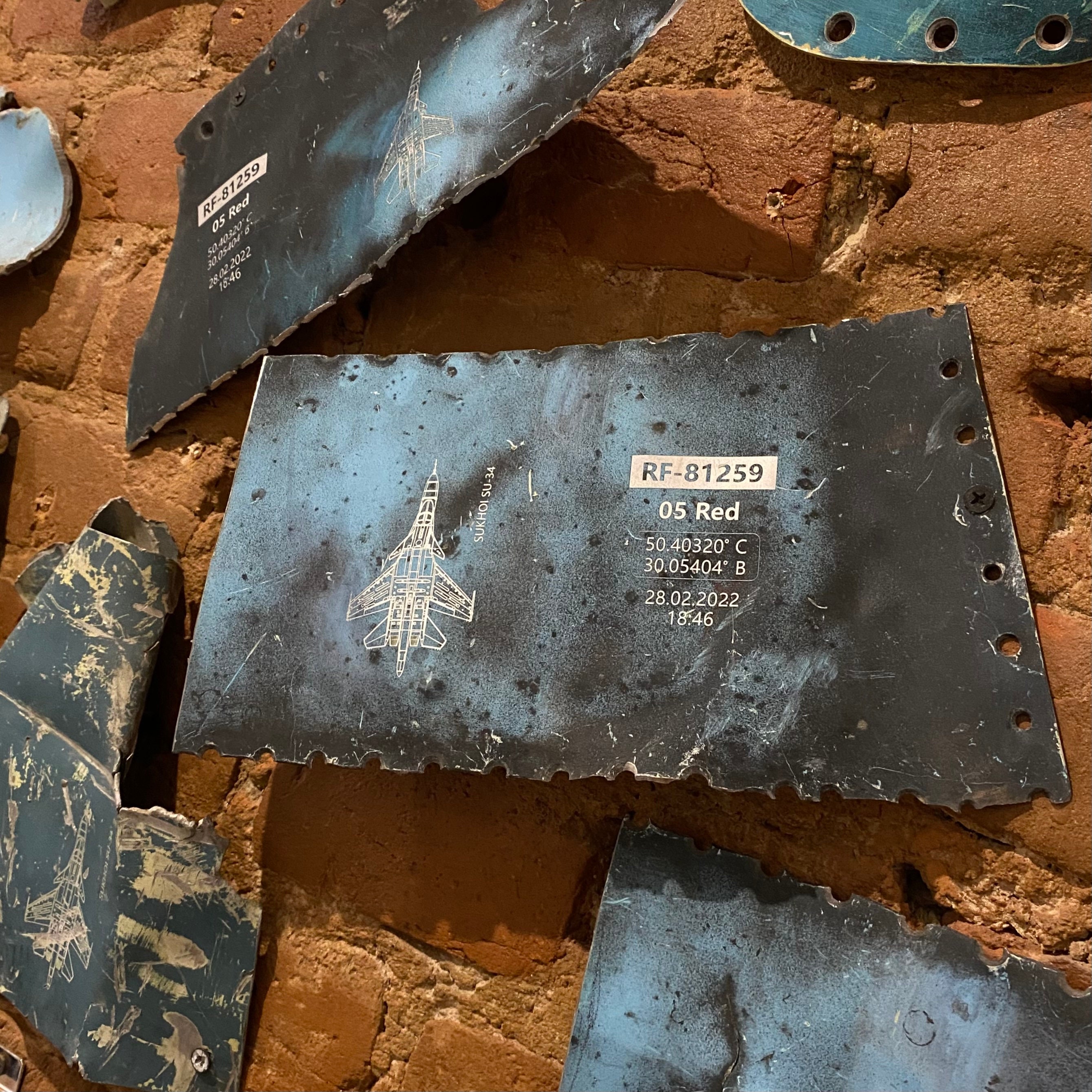
Credit: www.etsy.com
Disadvantages
When choosing welding rods, 6011 and 6013 are popular choices. Yet, both have limitations. Knowing these helps welders pick the right rod for their project.
Disadvantages Of Using 6011 Welding Rods
- Harsh Arc: The arc of a 6011 rod can be too harsh for beginners to control effectively.
- Surface Preparation: Requires thorough cleaning of the metal surface before welding, which can be time-consuming.
- High Spatter: The use of 6011 rods often leads to high spatter levels, making clean-up harder.
- Not for Thin Metals: These rods are not suitable for welding thin metals as they can burn through the material.
Disadvantages Of Using 6013 Welding Rods
- Low Penetration: 6013 rods create a weld with lower penetration, which isn’t ideal for thicker materials.
- Softer Arc: While easier to control, the softer arc may not be strong enough for industrial applications.
- Less Ductile Weld: The resulting weld is less ductile compared to those made with other rods, potentially compromising the joint.
- Not for Dirty Metals: These rods do not perform well on unclean or rusty metals, requiring prior preparation.
Frequently Asked Questions For 6011 Vs 6013 Welding Rods
What Are 6011 And 6013 Welding Rods?
6011 and 6013 are types of welding electrodes. The 6011 rod is known for its deeper penetration and flexibility with unclean metals. The 6013 rod provides a moderate penetration and produces a cleaner, slag-free weld, often used for cosmetic welds.
How Do 6011 Rods Differ From 6013?
6011 rods have a higher cellulose potassium coating, resulting in deeper penetration ideal for rusty or oily metals. Conversely, 6013 rods have a higher titania potassium coating, offering smoother welds suitable for clean surfaces and thin metals.
When To Use 6011 Welding Rods?
Use 6011 welding rods for tasks requiring deep penetration such as repairing farm equipment, pipes, and when working with dirty or rusted metals. They’re versatile, suitable for both AC and DC welding machines.
What Applications Are Best For 6013 Rods?
6013 welding rods are best for creating clean and smooth welds on lighter gauge metals. Ideal for automotive bodywork, furniture, and generally thin metals, they ensure less spatter and easier slag control, making them great for beginners.
Conclusion
Selecting the right welding rod is crucial to the success of your project. Both 6011 and 6013 rods offer unique benefits, suited for different conditions and metals. Remember your specific requirements when choosing between these versatile options. Good luck with your welding endeavors, and may your joints be strong and precise!