Welding joins materials by melting workpieces and adding a filler material. Soldering involves melting a filler metal to join components without altering the workpieces.
Understanding the differences between welding and soldering is crucial for selecting the appropriate method for joining materials. Welding is a fabrication process that fuses materials, typically metals or thermoplastics, by using high heat to melt the parts together and allowing them to cool, causing fusion.
It is commonly used in industrial construction and metal fabrication for creating strong, permanent bonds. Soldering, on the other hand, is a lower-temperature process that bonds metal surfaces with a filler metal having a lower melting point than the adjoining metal. Perfect for electronics and circuit boards, soldering creates strong electrical contacts while preserving the integrity of the components. Selecting between the two depends on the desired strength of the join, the materials involved, and the intended application.
Welding
Welding joins pieces of metal by melting them together. It opens up a world of possibilities for creating and repairing metal items. This high heat process fuses materials to form a strong bond as it cools. Understanding the ins and outs of welding will help determine if it’s the right technique for your project.
Process Overview
The welding process starts by applying intense heat to the metal parts to be joined. This heat melts the materials along the joining area. Often, a filler material is added to form a pool of molten material that cools to become a sturdy joint. A shielding gas also protects against contaminants in the air, which could weaken the weld.
Types Of Welding
- MIG Welding – Uses a wire welding electrode on a spool.
- TIG Welding – Known for precision, joining metals like aluminum.
- Stick Welding – Uses an electrode stick, suitable for windy conditions.
- Arc Welding – A common, versatile method.
Advantages
- Strong Joints: Welding creates very strong connections.
- Versatility: Joins a variety of metals and thicknesses.
- Speed: Welding can be quicker than other joining methods.
Disadvantages
Disadvantage | Details |
---|---|
Skill Required | Operators need training and practice. |
Equipment Cost | Initial investment can be high. |
Safety Concerns | Requires protective gear and knowledge. |
Soldering
Soldering stands as a pivotal joining technique in various industries.
Process Overview
Process Overview
The soldering process begins with heating. A soldering iron heats the metal parts. The solder – a filler metal – then melts. It flows into the joint, fusing the pieces upon cooling.
Types of Soldering
Types Of Soldering
Diverse soldering methods exist. Soft soldering, common and low temperature. Hard soldering includes brazing, requiring higher temperatures.
Advantages
Advantages
- Low-Temperature Process: Protects sensitive components from heat damage.
- Energy-Efficient: Consumes less energy than welding.
- Versatility: Useful for electronics, crafts, and plumbing.
Disadvantages
Disadvantages
- Strength Limitations: Soldered joints are not as strong as welded joints.
- Heat Sensitivity: Joints can degrade at high temperatures.
- Electrical Resistance: Not ideal for high-current applications.
Differences In Equipment
The right equipment makes all the difference – whether you’re welding or soldering. Each process uses distinct tools designed for precision and efficiency. Below, dive into what sets the gear apart for welding versus soldering.
Welding Equipment
Welders require heavy-duty equipment capable of high temperatures. Essential tools include:
- Welding machines that supply power
- Welding helmets for eye protection
- Gloves and aprons made of fire-resistant material
Other tools necessary include:
Equipment Type | Purpose |
---|---|
Electrodes | Create the weld |
Clamps | Hold pieces together |
Grinders | Smooth the weld |
Soldering Equipment
Soldering requires less intense heat. Key tools for this delicate process include:
- Soldering irons or guns to heat
- Soldering stations for temperature control
- Wire strippers to prepare cables
Must-have accessories:
Accessory | Function |
---|---|
Solder wire | Joins components |
Flux | Cleans metal surfaces |
Desoldering tools | Remove solder |
You will find welding equipment in auto and construction work. Soldering tools are common in electronics and jewelry making.
Materials Used
Materials used in both welding and soldering are critical for successful bonds in metalwork. While both processes create a strong joint between two materials, they use different materials to achieve the final bond. Let’s dive into what makes these materials unique to each process.
Welding Materials
Welding requires a combination of materials that can withstand immense heat. Common welding materials include:
- Base Materials: Usually metals or thermoplastics.
- Filler Metals: Added to the weld to ensure strength.
- Shielding Gas: Protects the weld from contamination.
- Flux: Can be coated on filler materials to prevent oxidation.
- Electrodes: Conduct current and can act as filler material.
Soldering Materials
Soldering involves more delicate materials suited for electronics and detailed metalwork:
- Solder: A metal alloy with a low melting point, often lead-tin.
- Flux: Cleans and prepares surfaces for bonding.
- Wire: Thin soldering wire for precision work.
- Paste: Mixture of flux and solder used in small amounts.
- Cleaning Agents: Ensure dirt-free surfaces for a strong bond.
Joint Strength And Durability
Understanding the difference between welding and soldering is crucial when selecting a method for joining materials. Two critical factors to consider are joint strength and durability. The right choice ensures a robust and long-lasting connection.
Welding Joint Strength
Welding creates immensely strong joints, capable of withstanding heavy loads and stress. This process melts the base materials together with a filler material, forming a solid bond upon cooling:
- Resistance to high pressure and impacts
- Often stronger than the materials being joined
- Durability in harsh environments, including outdoors
Common welding types include MIG, TIG, and stick welding, each providing different strengths for various applications.
Soldering Joint Strength
Soldering uses a filler metal with a lower melting point than the workpieces. The joint strength is generally:
- Good for small parts and delicate electronics
- Suitable for creating electrical connections
- Not designed for high-stress applications
While soldered joints are not as strong as welded ones, they serve well in many electronic projects where the strength of the bond is less critical.
Feature | Welding | Soldering |
---|---|---|
Strength | Very high | Moderate to low |
Durability | Excellent | Good, with some limitations |
Typical Use | Construction, heavy machinery | Electronics, jewelry making |
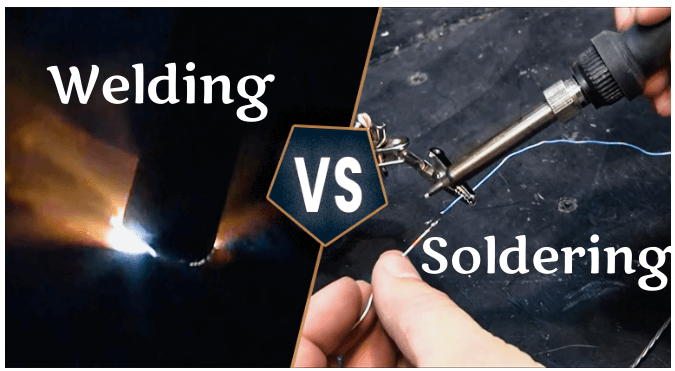
Credit: www.electronicshub.org
Heat And Energy Requirements
Understanding Heat and Energy Requirements is key in differentiating welding from soldering. Both processes join materials together. They use heat. Yet, they have distinct energy needs. Let’s explore the heat sources each method uses.
Welding Heat Sources
Welding requires intense heat. This heat melts metal pieces to join them. Various sources can produce this heat. Let’s list some common ones:
- Gas flames: Use a mix of gases to create a hot flame.
- Arc welders: Generate heat through electrical arcs.
- Laser welders: Focus a high-energy laser to melt materials.
- Plasma torches: Create heat with ionized gas.
Soldering Heat Sources
In soldering, the heat isn’t as high as welding. Here’s how we get the heat:
- Soldering iron: Heats up to melt solder, a filler material.
- Hot-air guns: Blow hot air to melt and flow the solder.
- Induction soldering tools: Use electromagnetic fields to heat.
Every source serves a unique task. The choice depends on the material and the project.
Safety Considerations
Working with metals needs care. Welding and soldering have risks. It’s vital to know how to stay safe. This section tells you safety measures to follow. Keep yourself and others safe while working.
Welding Safety Measures
Welding requires high heat and exposes you to bright light and hazardous fumes. Following these safety measures is essential:
- Wear Protective Gear: Gloves, mask, and apron shield your skin and eyes.
- Use Proper Ventilation: Avoid breathing in toxic fumes; work in a well-ventilated space or use a fume extractor.
- Guard Your Eyes: Use a helmet with a proper filter shade to protect against intense light.
- Handle Equipment With Care: Check tools for damage. Use them correctly to prevent accidents.
- Keep a Fire Extinguisher Nearby: Be ready for any fire by having an extinguisher within reach.
Soldering Safety Measures
Soldering has its risks too, primarily from hot tools and toxic fumes. These key pointers ensure a safer experience:
- Wear Safety Glasses: Protect your eyes from splashes of molten solder.
- Use Smoke Absorbers: Minimize inhalation of harmful fumes.
- Avoid Direct Contact: Soldering irons can burn. Handle them with care.
- Work in a Clean Space: Keep your workspace tidy to prevent accidents.
- Handle Lead-Free Solder: It’s less hazardous than lead-based solder.
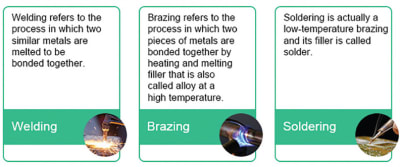
Credit: www.techbriefs.com
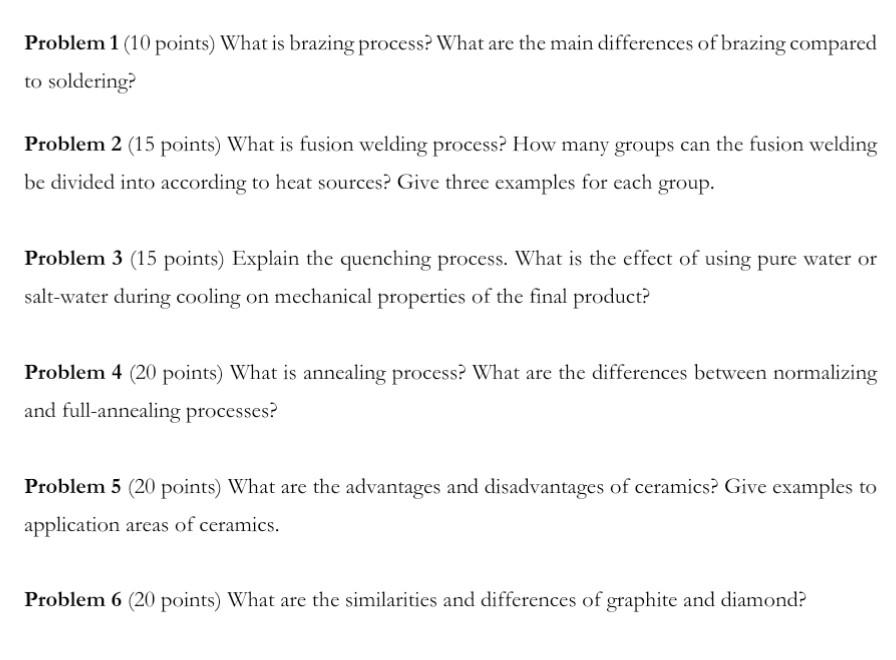
Credit: www.chegg.com
Frequently Asked Questions Of Welding Vs Soldering
What Is Better Welding Or Soldering?
Welding creates stronger joints and is suited for metal construction. Soldering offers less strength but is ideal for delicate electronics due to lower temperatures. Choose based on material strength needs and heat sensitivity.
Why Is Soldering Preferred Over Welding?
Soldering offers lower temperature processing than welding, preserving delicate electronics and components. It’s less expensive and requires simpler equipment, making it accessible for small-scale or intricate work where precision is essential.
Is Soldering Tiny Welding?
No, soldering is not tiny welding. It involves melting a filler metal to join components without melting them, unlike welding which fuses parts together directly.
Is Soldering The Same Process As Welding?
Soldering and welding are different processes. Soldering uses a lower temperature to join metals without melting the base materials. Welding fuses materials by melting them together at high temperatures.
Conclusion
Welding and soldering each offer distinct advantages for metal joining projects. Your choice hinges on material, strength needs, and project intricacy. Both methods stand as pillars in the construction of durable structures and intricate circuitries. By understanding their differences, craftsmen can select the most appropriate technique for a lasting bond.
Choose wisely, and your creations will stand the test of time.