Welding copper with flux core process is technically possible but is not the most common method. Specialized equipment and techniques are generally required to achieve a successful weld.
Welding, particularly with copper, demands precise methodology for supreme results. Copper’s high thermal conductivity necessitates using processes that can manage its unique properties and the challenges they present. Flux core welding, usually associated with mild or stainless steel, can be adapted for copper.
This requires understanding the proper flux to use and the control of welding parameters to prevent burn-through and ensure strong joins. For hobbyists or those new to welding, mastering the technique can be an uphill task, but professionals often find viable paths to success with the right gear and expertise. When approached with caution and the correct settings, flux core welding can join copper for various applications, though it may not be the first choice for those seeking efficiency and convenience.
Understanding Flux Core Welding
Flux-core welding, or FCAW (Flux-Cored Arc Welding), is a versatile welding process well-suited for joining metals such as copper. This method harnesses the power of a continuously fed tubular electrode containing flux. The process is often likened to MIG welding but differs due to using a special tubular wire filled with change. Let’s explore how flux core welding works and examine its advantages and limitations when working with copper.
How Flux Core Welding Works
Flux core welding operates on the principle of creating an electric arc between the workpiece and a continuously fed consumable tubular electrode wire. The internal flux in the wire has multiple functions:
- Shielding Gas Production: Upon heating, the flux generates a gas that protects the weld puddle from contaminants in the atmosphere.
- Slag Formation: As the weld cools, the flux creates a layer of slag on top, which can be easily chipped off post-weld, thus aiding the cleaning process.
- Stabilizing the Arc: Flux helps to stabilize the welding arc, making the process more forgiving and smoother for the welder.
In the context of welding copper, an adequately chosen flux core wire assists in mitigating common issues such as oxidation and ensures a stronger bond.
Advantages Of Flux Core Welding
Flux core welding offers several benefits, significant when welding materials like copper:
- High Efficiency: FCAW is faster than traditional welding methods due to the continuous wire feed system and higher deposition rates.
- Flexibility: This method is suitable for various positions, including vertical and overhead welding, providing versatility on the job.
- No Need for External Gas: Because the flux within the core generates its shielding gas, FCAW is advantageous in outdoor conditions where the wind might disperse a shielding gas.
- Welds Thick Sections: FCAW can handle thicker sections of metal without the need for multiple passes.
Welders often find flux core welding more straightforward to master, with less splatter and cleaner results, which is particularly useful when working with challenging materials.
Limitations Of Flux Core Welding
Despite its various advantages, flux core welding also comes with certain limitations:
Limitation | Explanation |
---|---|
Equipment Costs | Initial investment in FCAW equipment may be higher due to the specialized wire and capable welding machine. |
Cleanup | Post-weld slag removal is necessary, which adds an extra step to the welding process. |
Portability | The heaviness of the welding system can limit its portability compared to other, lighter processes. |
Sensitivity to Parameters | Correct parameter settings are crucial, as minor deviations may result in poor weld quality. |
While flux core welding may present challenges, such as extra post-weld cleaning and a learning curve in parameter settings, its ability to create strong bonds in copper and various metals underscores its value in the welding toolkit.
Can You Weld Copper With Flux Core?
Welding copper presents unique challenges due to its high thermal conductivity and low melting point. While traditional welding methods can be challenging, flux core welding offers a distinct approach. This section explores the mysterious possibility of joining copper using flux core welding and sheds light on the compatibility, techniques, and critical considerations one must know.
Compatibility Of Flux Core With Copper
Whether you can weld copper with a flux core largely depends on the material’s compatibility with the process. Flux core welding is designed to overcome the common barriers to welding non-ferrous metals. However, choosing the correct type of wire and compatible equipment is paramount for a successful bond.
- Copper alloys: Certain alloys of copper are more amenable to flux core welding.
- Wire selection: Opting for a wire designed explicitly for copper or high thermal conductivity metals is essential.
Flux core welding of copper requires precision and the adoption of specialized techniques to ensure strong and durable welds.
- Control heat input: Managing the high thermal conductivity of copper is crucial to prevent warping.
- Clean the surface: Properly clean the copper surface to remove contaminants that interfere with the weld.
- Joint preparation: Proper standard configuration is critical to accommodating the fill material.
Considerations For Successful Copper Welding
Consideration | Detail |
---|---|
Machine Settings | Adjusting amperage and voltage to suit the thickness and type of copper. |
Welding Environment | Maintain a clean, controlled environment to prevent contamination. |
POPE | Use appropriate personal protective equipment to handle the high glare and spatter. |
Considering these aspects and carefully preparing, the flux core welding copper process can lead to impressive results that wouldn’t be possible with conventional means. With the proper technique and preparation, the once daunting task of copper welding becomes an accessible and reliable fabrication process.
Choosing The Right Flux Core Wire For Copper
When working with metals as conductive and thermally sensitive as copper, selecting the appropriate welding wire is crucial. Flux core welding offers unique advantages for copper joining tasks, particularly in terms of convenience and effectiveness. Let’s delve into the specifics of choosing the ideal flux core wire for copper to guarantee intense, clean, and precise welds.
Characteristics Of Ideal Flux Core Wire For Copper
The quest for the perfect flux core wire for copper begins with understanding the essential characteristics that make the wire suitable for the material. The correct wire should provide the following:
- Proper melting point compatibility – closely aligning with copper to prevent warping or damage.
- Enhanced electrical conductivity – to handle the current without degradation.
- Corrosion resistance – to maintain the integrity of the weld over time.
- Sufficient tensile strength – ensuring the joint can support the required load.
Suitable Flux Core Wire Types For Copper
The market supplies diverse flux core wire options, yet not all are compatible with copper. Here’s a brief rundown:
Wire Type | Composition | Applications |
---|---|---|
Aluminum Bronze | A mix of aluminum and bronze that provides excellent thermal conductivity. | It is best for joining copper to aluminum or for surfacing. |
Silicon Bronze | It contains silicon to enhance flow and reduce fuming. | Suitable for welding different types and grades of copper. |
Phosphor Bronze | Phosphorus addition increases wear resistance and minimizes porosity. | They are applied in fabricating copper alloys and marine components. |
The optimal flux core wire is vital for producing robust, reliable welds in copper applications. It’s essential to balance the wire’s compatibility with the properties of copper and the job’s specific requirements. Even in challenging copper welding scenarios, you can achieve professional results with the correct wire.
Preparing Copper For Flux Core Welding
Welding is a skillful art, and when it comes to working with copper using the flux core method, preparation is critical. While predominantly used for steel, flux core welding can also be applied to copper, known for its excellent thermal and electrical conductivity, ensuring compelling and durable joins. However, copper presents unique challenges, unlike welding steel, due to its higher thermal conductivity. Thus, meticulous preparation is essential to achieve solid and clean welds on copper. Our step-by-step guide dives into how to prepare copper for flux core welding.
Surface Cleaning And Preparation
Before you strike an arc, cleansing the copper surface is paramount. Exposing a clean surface ensures that the weld takes well and the joint strength is optimal. Follow these key steps:
- Begin by mechanically removing any oxide layer present on the copper with a wire brush or sandpaper.
- Wipe away any surface contaminants such as grease or dirt using a solvent like acetone or a specialized metal cleaner.
- Ensure the copper is completely dry before proceeding; even a tiny amount of moisture can lead to porosity in the weld.
The Importance Of Flux And Gas Selection
Flux plays a critical role in preventing oxidation during the welding process. It guards against atmospheric contamination and helps with metal flow. When welding copper:
- Select a flux core wire compatible with copper to enhance its action during welding.
- Also, consider using a shielding gas to protect the weld puddle from the surrounding atmosphere. Argon, or mixtures of argon with helium or carbon dioxide, can be effective.
Proper Joint Fit-up For Flux Core Welding
Ensuring a precise joint fit-up is vital for a successful weld. For copper flux core welding, it is essential to:
- Match the pieces that need to be joined with minimal gaps. Copper’s high thermal conductivity requires tight fit-ups to prevent heat loss.
- Be mindful of joint design. A bevel on thicker sections of copper can help achieve deep penetration and a stronger weld.
- Tack the pieces in place to prevent movement due to copper’s expansion when heated.
Welding Techniques For Copper With Flux Core
Welding copper with a flux core process can be problematic for many crafters and professionals. Unlike more commonly welded materials like steel, copper presents unique challenges due to its high thermal conductivity and lower melting point. However, with the advent of flux core welding, there is now a viable way to join copper components effectively. Understanding the correct techniques is crucial for a successful weld. Let’s explore how to master the art of welding copper with flux core through essential steps and considerations.
Setting The Correct Welding Parameters
Achieving a strong and clean copper weld with a flux core requires precision in setting your welding parameters. The key factors to adjust include voltage, amperage, and wire feed speed. The settings typically need to be higher for copper due to its heat dissipation properties. Start with the machine’s recommendations for copper, then make fine adjustments based on the thickness of the material and the weld’s requirements. Using a trial-and-error approach on scrap pieces first can save your project from costly mistakes.
Welding Position And Angle Considerations
- The position of the copper workpieces and the angle at which you weld are pivotal for penetration and overall weld quality. Flux core welding often requires a drag or pull technique, and maintaining a consistent 15- to 20-degree angle with the torch can help achieve a uniform weld bead.
- For overhead or vertical welding, settings need to be readjusted, and a steady hand is more critical to prevent sagging or dripping.
Managing Heat Input And Control
One of the most significant challenges when welding copper is managing its high thermal conductivity. Heat input and control are integral for producing a high-quality weld without burning through the material or creating a weak joint.
Implementing a stitch welding technique, wherein short lengths of welds are laid down with cooling periods in between, can be immensely beneficial. This technique reduces the overall heat input and minimizes the warping and distortion of the copper. Additionally, utilizing a backing material to dissipate heat can further enhance control during the welding process.
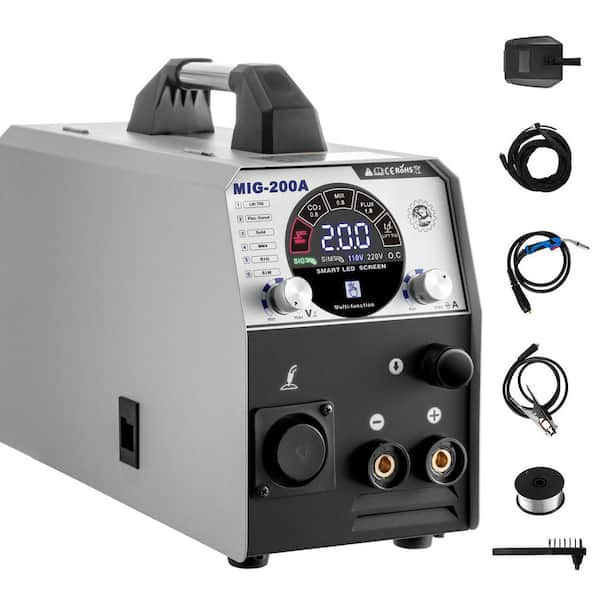
Credit: www.homedepot.com
Quality Control And Post-welding Considerations
Completing a successful flux core welding project on copper involves meticulous attention far beyond the welding process itself. Once the bead is laid, quality control and post-welding considerations come into play to ensure the final product’s structural integrity and visual appeal. Understanding how to inspect and test the welds, clean and finish the welded joint, and address potential defects is crucial for a cohesive and reliable outcome.
Inspecting And Testing The Flux Core Copper Welds
Inspection and testing are paramount to assess the quality of a flux-core copper weld. Here are vital techniques to ensure your welded assembly meets the standards:
- Visual Inspection: Begin with a detailed visual examination to spot any surface irregularities or inconsistencies.
- Non-Destructive Testing (NDT): Employ ultrasonic, radiographic, or eddy current tests to detect subsurface defects without damaging the weld.
- Destructive Testing: In some instances, sacrificing a sample weld for physical testing can provide insight into the weld’s overall strength and performance.
Post-welding Cleaning And Finishing
Upon completion of welding, it’s essential to execute proper cleaning and finishing to protect the weld integrity and enhance the appearance. This involves:
- Slag Removal: Carefully remove any residual slag left from the welding process to prevent corrosion and enable accurate inspections.
- Surface Cleaning: Use appropriate cleaning agents and techniques to eliminate contaminants such as oxides, oils, and dust.
- Polishing and Grinding: This step smoothes out any rough spots and brings a uniform finish, which is vital for aesthetic and functional purposes.
Addressing Common Welding Defects And Issues
Despite best efforts, defects can arise, necessitating prompt attention and remediation. Common issues include:
Defect | Description | Remediation Strategy |
---|---|---|
Porosity | Gas pockets are trapped within the weld. | Modify welding parameters and technique and ensure clean base materials. |
Cracking | Cracks appearing in the weld or heat-affected zone. | Review preheat and post-heat procedures, as well as filler material selection. |
Undercut | Material erosion along the weld toe. | Adjust the welding speed and angle to distribute the heat more evenly. |
Incomplete Fusion | Lack of proper bonding between weld metal and base metal. | Check joint design and ensure proper welding technique with correct parameters. |
Best Practices And Safety Measures For Flux Core Welding Copper
While versatile and robust for various metals, Flux core welding is not traditionally associated with copper due to the metal’s high thermal conductivity. Nonetheless, with professional skill and adherence to stringent safety protocols, welding copper using flux core techniques effectively under the right circumstances is possible. This section delves into the best practices and critical safety measures you must adopt for successful flux core welding of copper.
Safety Precautions For Flux Core Welding
Adhering to safety measures is paramount before, during, and after the flux core welding process. Ensure you have:
- Protective Gear: Wear auto-darkening welding helmets, fire-resistant gloves, and long-sleeve jackets.
- Ventilation: Ensure proper ventilation to avoid fume inhalation.
- Equipment Check: Inspect your welder and accessories for any damage before starting.
- Electrical Safety: Avoid electric shocks by ensuring all equipment is properly grounded.
Environmental Considerations For Copper Welding
Environmental factors can drastically affect the quality of the weld. Key concerns include:
Factor | Considerations |
---|---|
Temperature | Excellent, stable environments prevent overheating. |
Humidity | Low humidity levels reduce oxidation risk. |
Air Quality | Clean air free of contaminants ensures a better weld. |
Ensuring Occupational Health In Flux Core Welding
To maintain high standards of occupational health during flux core welding:
- Use respiratory protection when necessary.
- Adopt ergonomic practices to prevent physical strain.
- Implement regular breaks to reduce fatigue.
- Conduct consistent training sessions on safety protocols.
Precision and caution are your allies in the challenging craft of flux core welding copper. By respecting the material qualities and being vigilant about personal safety and environmental conditions, you can achieve integrity and strength in your copper welds.
Frequently Asked Questions On Can You Weld Copper With Flux Core
Can You Successfully Weld Copper With A Flux Core Welder?
Flux core welding is not typically recommended for copper due to its high thermal conductivity. Specialized equipment and filler materials are usually required to weld copper effectively to ensure proper bonding and strength.
What Type Of Welding Is Best For Copper?
TIG (Tungsten Inert Gas) welding is considered the best method for welding copper. It allows for precise heat control and provides a high-quality finish, essential due to copper’s high thermal conductivity.
Is Flux Required When Welding Copper?
Yes, flux is necessary when brazing copper to prevent oxidation and ensure a clean join. However, welding processes like TIG may not need change because an inert gas shields the weld.
Are There Any Special Considerations When Welding Copper?
Welding copper requires managing its high thermal conductivity and expansion rate. Preheating, proper joint design, and choosing the suitable filler material are crucial steps to avoid weld defects such as cracking.
Conclusion
With the proper technique and tools, welding copper with a flux core is achievable. This method extends the capabilities of welders, offering flexibility for various projects. Remember, safety and precision are vital. Embrace the challenge, and your copper-welding skills may shine as brightly as the metal.