The wire feed motor in a MIG welder is responsible for pushing the welding wire through the torch. It plays a crucial role in ensuring a steady and consistent feed of the wire during the welding process, ultimately impacting the quality of the weld.
The wire feed motor is critical in maintaining proper welding parameters and achieving desirable results. Understanding its function and importance is essential for welders and fabricators to ensure smooth and efficient welding operations. We will delve into the significance of the wire feed motor in MIG welding, its function, joint issues, and troubleshooting methods to maintain optimal performance.
Whether you are a beginner or an experienced welder, grasping the fundamentals of the wire feed motor can significantly enhance your welding proficiency.
What Is A Wire Feed Motor?
Regarding MIG welding, the wire feed motor plays a crucial role. Understanding what a wire feed motor is, its function, types, and importance in MIG welding can help welders make informed decisions when choosing equipment and optimizing their welding performance.
Function
In MIG welding, the wire feed motor is responsible for pulling the welding wire from the spool and feeding it through the welding gun at a controlled speed. This process ensures a consistent and accurate wire supply to the welding arc, facilitating smooth and precise welds.
Types
Wire feed motors come in various types, including standard DC motors and advanced servo motors. The classic DC motors are commonly used in entry-level MIG welders, offering reliable wire feeding capability. On the other hand, servo motors provide enhanced control, accuracy, and speed regulation, making them well-suited for professional-grade MIG welding applications.
Importance In Mig Welding
The wire feed motor is a critical component of MIG welding equipment, contributing to the overall efficiency and quality of the welding process. Its precise control over wire feed speed directly impacts the weld’s deposition rate, bead appearance, and penetration depth, ultimately influencing its strength and dh. Therefore, selecting a wire feed motor that meets the specific requirements of a welding task is essential for achieving optimal results.
Components Of A Wire Feed Motor
When it comes to understanding the effectiveness and functionality of a MIG welder wire feed motor, it is crucial to delve into its components. Each component plays a key role in ensuring the smooth and precise wire feeding process, ultimately influencing the quality of the weld. In this post, we will explore the essential components of a wire feed motor, shedding light on the drive rollers, motor assembly, and tensioning mechanism.
Drive Rollers
The drive rollers are instrumental in ensuring the smooth and continuous feeding of the welding wire. These rollers have grooves that grip the wire and propel it forward, guiding it toward the welding torch. The material and condition of the drive rollers significantly impact the overall feeding performance and wire integrity during the welding process. Regular inspection and maintenance of the drive rollers are critical to prevent slippage and ensure consistent wire feed.
Motor Assembly
The motor assembly serves as the powerhouse of the wire feed system, providing the necessary torque and speed to drive the wire through the welding gun. It consists of a robust motor, gearbox, and associated components that harmonize to maintain a constant and reliable wire feed rate. The reliability and precision of the motor assembly directly influence the weld quality, making it a pivotal component of the wire feed motor.
Tensioning Mechanism
The tensioning mechanism regulates the tension applied to the welding wire as it passes through the feed system. Proper tensioning is crucial to prevent wire slippage, bird-nesting, and erratic feeding behavior. This mechanism typically incorporates adjustable tension settings, ensuring compatibility with various wire diameters and welding applications. A well-calibrated tensioning tool contributes to smooth wire delivery and minimizes the risk of feed-related issues during welding.
Factors Affecting Wire Feed Motor Performance
Several factors come into play when it comes to achieving optimal performance with a MIG welder wire feed motor. Understanding these factors is crucial for welders to ensure smooth and consistent wire feeding, leading to high-quality welds. Let’s examine the critical variables affecting wire feed motor performance.
Wire Diameter And Type
The wire diameter and type used in the welding process directly impact the performance of the wire feed motor. Different wire diameters and types require varying levels of feeding speed and force. For instance, thicker wires generally demand higher feed speeds and more robust motors to ensure steady and uniform wire delivery.
Voltage And Amperage Settings
The voltage and amperage settings selected on the welding machine are critical in wire feed motor performance. When the voltage and amperage are not set correctly, the motor may struggle to maintain consistent wire speed, leading to irregular and poor-quality welds. Welders must ensure that the settings align with the wire feed motor’s capabilities, disruptions in the welding process.
Material Thickness And Joint Configuration
The material thickness and joint configuration impact the workload and demand on the wire feed motor. Thicker materials and complex standard designs require a more robust and powerful engine to push the wire through the welding gun effectively. Understanding how these variables affect motor performance is essential for achieving precise and reliable welds.
Common Issues And Troubleshooting
When using a MIG welder, encountering issues with the wire feed motor can be frustrating. It can disrupt your work, leading to delays and subpar welds. Understanding the common issues and troubleshooting techniques can help prevent downtime and ensure smooth and efficient welding operations.
Wire Jamming
Wire jamming can occur for various reasons, such as improper alignment of the wire, debris accumulation, or issues with the wire drive mechanism. To troubleshoot wire jamming:
- Check the alignment of the wire spool and ensure it feeds smoothly.
- Clear any debris or obstructions from the wire path.
- Inspect the wire drive mechanism for any damage or misalignment.
- Adjust the tension settings on the wire feeder to ensure proper wire feeding.
Inconsistent Feed Speed
Inconsistent feed speed can lead to poor weld quality and irregular bead patterns. To address this issue:
- Inspect the wire feed motor for any signs of wear or damage.
- Check the wire feeding mechanism for obstructions or misalignment.
- Adjust the wire feed speed settings according to the manufacturer’s remanufacturer to ensure the wire spool is aligned correctly and tensioned to maintain consistent feed speed.
Motor Overheating
Motor overheating can be detrimental to the longevity of the wire feed motor and may result from prolonged use at high speeds or inadequate cooling. To troubleshoot motor overheating:
- Allow the motor to cool down if running continuously for an extended period.
- Clean the motor and surrounding components to remove any accumulated debris or dust that may impede cooling.
- Check the motor’s ventilation motors for blockages and ensure proper airflow.
- If applicable, review the welding parameters and adjust the settings to reduce the load on the wire feed motor.
Maintenance Tips For Optimal Performance
Regular Lubrication
Regular lubrication of the wire feed motor ensures smooth and efficient operation. Lubricating the motor parts such as bearings, gears, and shafts helps reduce friction and wear, thus extending the motor’s lifespan and maintaining its performance at an optimal level. Use a high-quality lubricant recommended by the manufacturer, and follow the specified intervals for applying lubrication to keep the motor running smoothly.
Tension Adjustment
Proper tension adjustment on the wire feeder is essential for consistent and accurate wire feeding. Regularly check the tension settings and adjust as needed to ensure that the wire is fed smoothly without snagging or slipping. Maintaining the correct tension also improves weld quality and prevents issues such as erratic wire feed and bird-nest formations. Refer to the user manual for specific guidelines on tension adjustment and follow them diligently.
Wire Speed Calibration
Calibrating the wire speed is a critical aspect of maintaining optimal welding performance. Periodically calibrate the wire speed settings to match the specific welding parameters and material. Proper calibration enhances weld quality, minimizes spatter, and promotes a stable arc. Utilize the wire speed calibration feature on your welder and make adjustments as necessary based on the welding requirements to achieve precise and consistent wire feeding.
Upgrading And Modifying The Wire Feed Motor
When it comes to maximizing the performance of a MIG welder, upgrading and modifying the wire feed motor can make a world of difference. Whether aiming for precision, speed, or versatility in your welding projects, enhancing the wire feed motor can unlock a new level of efficiency and control.
Aftermarket Options
Upgrading the wire feed motor with aftermarket options provides a range of benefits, including the potential for increased speed, precision, and reliability. Aftermarket wire feed motors often feature advanced design and construction, delivering smoother wire feeding and improved control over the welding process. The compatibility with various welding machines and the ability to adapt to different wire types make aftermarket options popular for welders seeking to take their welding performance to the next level.
Integration With Welding Systems
Modifying the wire feed motor for seamless integration with welding systems is essential for welders looking to optimize their welding setup. A well-integrated wire feed motor ensures smooth operation and responsiveness, allowing precise control over the wire feed speed and consistency. Integrating the wire feed motor with welding systems can also enhance the overall efficiency and productivity of the welding process, leading to superior weld quality and reduced downtime.
Future Trends In Wire Feed Motor Technology
The future of wire feed motor technology is rapidly evolving, driving significant changes in the welding industry. From innovative motor designs to automation and connectivity, the future trends in wire feed motor technology are poised to revolutionize the welding process. Let’s explore eLet’s developments in wire feed motor technology that are shaping the future of welding.
Innovative Motor Designs
Innovative motor designs are at the forefront of future wire feed motor technology trends. Manufacturers are exploring advanced motor technologies that improve efficiency, precision, and durability. These innovative designs aim to enhance the wire feeding process, ensuring consistent and reliable performance. By integrating cutting-edge motor designs, welders can expect smoother wire feeding, reduced downtime, and improved productivity.
Automation And Connectivity In the Welding Industry
Automation and connectivity are revolutionizing the welding industry, and wire feed motor technology is no exception. Integrating automation features in wire feed motors enhances the welding process by enabling remote monitoring, control, and adjustment of wire feeding parameters. Furthermore, connectivity capabilities allow seamless communication between welding equipment and centralized control systems, paving the way for enhanced efficiency and real-time data analysis.
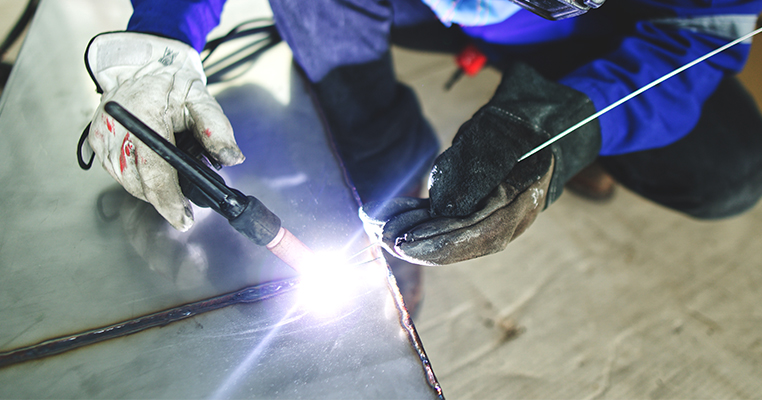
Credit: blog.red-d-arc.com
Frequently Asked Questions Of Mig Welder Wire Feed Motor
What Is A Wire Feed Motor In A Mig Welder?
A wire feed motor in a MIG welder is responsible for continuously feeding welding wire through the welding gun. It ensures a consistent and smooth wire feed, essential for achieving high-quality welds.
How To Troubleshoot Wire Feed Motor Issues?
Check for any wire obstructions and proper tension on the feed roller, and ensure the wire spool is seated correctly. Inspect the motor for wear or damage, and consult the user manual for specific troubleshooting steps.
Why Is The Wire Feed Motor Important In Welding?
The wire feed motor is crucial as it regulates the speed and consistency of the welding wire, directly impacting the quality of welds. It ensures a steady and controlled welding wire feed, contributing to the overall welding performance.
Can I Upgrade The Wire Feed Motor In My Mig Welder?
Yes, you can upgrade the wire feed motor in your MIG welder to improve performance or replace a faulty unit. Ensure compatibility with your welder model, and consider consulting a professional if unsure about your installation process.
Conclusion
The wire feed motor plays a crucial role in the performance of a MIG welder. It ensures smooth and consistent wire feeding, contributing to high-quality welds. Proper maintenance and the right motor selection are essential for optimal welding results. Understanding its function and importance can help users maximize the efficiency of their welding projects.